Je nach Struktur und Anforderungen des Kunststoffprodukts unterscheidet sich auch die Struktur der Spritzgussform. Zu den gängigen Spritzgussformen gehören: Einfache Trennebenenspritzgussformen, Mehrfach-Trennebenenspritzgussformen, seitliche Kernzug-Spritzgussformen mit Schrägführungssäule, innere Kernzug-Spritzgussformen mit Schrägstift sowie Heißkanal-Spritzgussformen.
1. Einfache Trennebenenspritzgussform
Diese Form wird auch als Zwei-Platten-Form bezeichnet und ist häufig bei Spritzgussformen mit großen Angüssen zu finden. Sie zeichnet sich durch eine einfache Konstruktion und hohe Praktikabilität aus, weshalb sie weit verbreitet ist. Der Nachteil ist jedoch, dass der Anguss groß ist, was oft einen zusätzlichen Schritt zur Entfernung erfordert und Angussmarken auf der Oberfläche des Produkts hinterlässt. Daher eignet sich diese Form für Spritzgussteile, bei denen die Oberflächenqualität keine hohe Priorität hat.
2. Mehrfach-Trennebenenspritzgussform
Diese Form verfügt über zwei oder mehr Trennebenen, wobei die doppelte Trennebene am häufigsten vorkommt. Die doppelte Trennebenenspritzgussform, auch als Drei-Platten-Form bekannt, wird häufig für Produkte mit Punktanguss verwendet und daher auch als Feinangussform bezeichnet. Diese Form wird häufig für Einzelkavitäten- oder Mehrkavitätenformen mit Punktanguss, Formen mit seitlichen Trennmechanismen auf der festen Formseite und Formen mit speziellen Kunststoffstrukturen, die eine sequenzielle Trennung erfordern, eingesetzt.
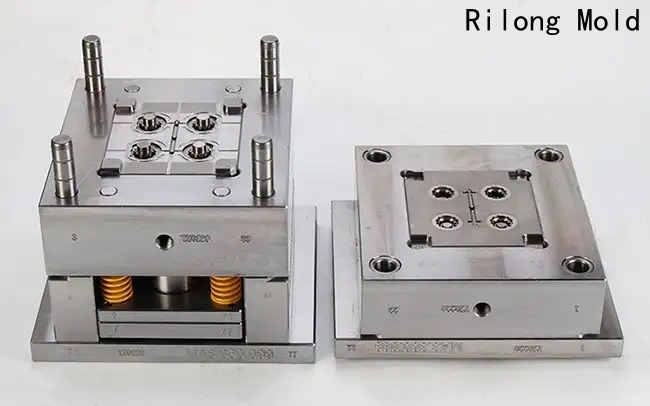
Der erste Trennvorgang dient dazu, das erstarrte Material im Angusskanal herauszuziehen, während der zweite Trennvorgang den Einguss vom Material und dem Kunststoffteil trennt, sodass kein zusätzlicher Schritt zur Entfernung des Angusses erforderlich ist.
3. Schrägführungsseitige Kernzieh-Spritzgussform
Wenn die Seitenwand eines Kunststoffteils Durchgangslöcher, Vertiefungen oder Vorsprünge aufweist, müssen die Formelemente seitlich beweglich sein. Der gesamte Mechanismus, der den Kern seitlich bewegt, wird als seitlicher Kernziehmechanismus oder Querkernziehmechanismus bezeichnet. Es gibt viele Arten solcher Mechanismen, darunter schrägführungsseitige Kernziehung, hydraulische Kernziehung und pneumatische Kernziehung. Am häufigsten ist die schrägführungsseitige Kernziehung, wie in Abbildung 3.25 dargestellt. Beim Öffnen der Form bewegt die Schräge zuerst den Schieber nach außen. Sobald der Seitenkern vollständig aus dem Produkt gelöst ist, setzt der Auswerfermechanismus ein und stößt das geformte Teil aus.
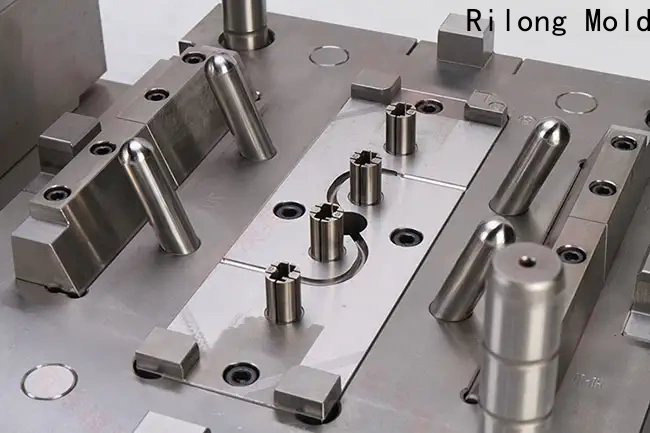
4. Schrägstift-Innenkernzieh-Spritzgussform
Wenn das Innere eines Produkts Hinterschnitte aufweist, werden Schrägstifte benötigt, um diese zu formen. Spritzgussformen mit Schrägstiften für die Innenkernziehung werden als Schrägstift-Innenkernzieh-Spritzgussformen bezeichnet. Diese Formen sind relativ komplex, da sie zusätzliche Schrägstiftmechanismen erfordern. Beim Öffnen der Form trennen sich zuerst die vordere und hintere Formhälfte. Dann bewegt der Auswerfermechanismus der Spritzgießmaschine die Auswerferplatte in Richtung Entformung. In dieser Phase zieht sich der Schrägstift langsam aus dem Hinterschnittbereich des Produkts zurück. Nach vollständigem Austritt wird das Produkt durch den Auswerfermechanismus der Form ausgestoßen.
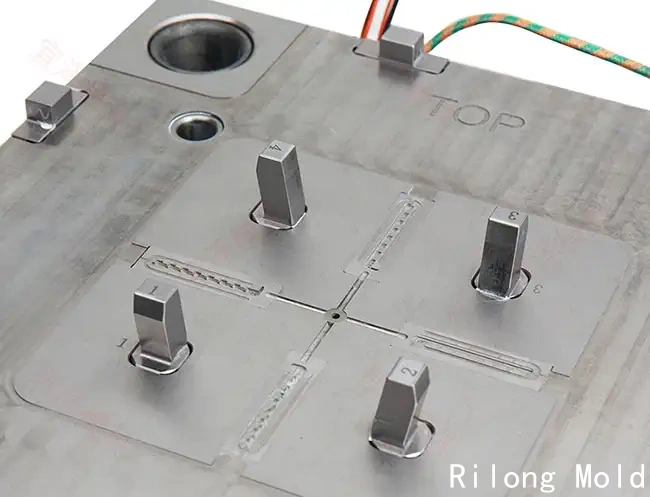
5. Heißkanal-Spritzgussform
Mit der schnellen Entwicklung automatisierter Spritzgießverfahren werden Heißkanal-Spritzgussformen zunehmend eingesetzt. Der Hauptunterschied zu herkömmlichen Formen besteht darin, dass der Kunststoff im Anschnittsystem während des Spritzvorgangs nicht erstarrt und nicht zusammen mit dem geformten Teil ausgeworfen wird. Daher werden diese Formen auch als „anschnittlose Formen“ bezeichnet. Die Hauptvorteile sind:
① Reduzierung des Materialabfalls, wodurch Rohstoffe gespart und der Schritt zur Entfernung des Kaltkanals eliminiert wird.
② Geringerer Druckverlust im Zuführungssystem, wodurch der Spritzdruck optimal genutzt und die Qualität des Kunststoffteils verbessert wird.
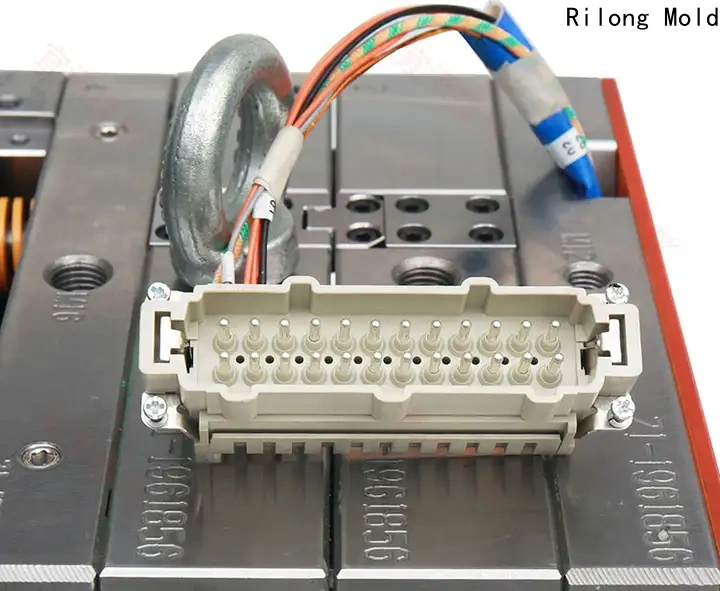
Heißkanal-Spritzgussformen lassen sich leicht identifizieren, da sie in der Regel über Kabel und Anschlusskästen verfügen. Aufgrund ihrer komplexen Struktur, hohen Kosten und strengen Anforderungen an die Temperaturkontrolle sind sie besonders für die Massenproduktion geeignet.