Hemos adquirido una amplia experiencia en sellado impermeable, y a continuación se presentan varios casos exitosos que esperamos ayuden a usted y a su equipo a explorar la solución más adecuada para sus productos.
Caso 1: Caja de policarbonato con sellador K31 FIPFG Para este producto, utilizamos el sellador K31 FIPFG (Form-In-Place Foam Gasket) aplicado a una parte de la caja de policarbonato y comprimido por una parte trasera de fundición a presión de aluminio. Después de que los componentes materiales reaccionan, la junta de espuma se vuelve libre de adhesión y se puede instalar en los componentes de acoplamiento. La función de sellado se logra comprimiendo aproximadamente el 30-60% de la junta de espuma curada, asegurando una clasificación de impermeabilidad IP67.
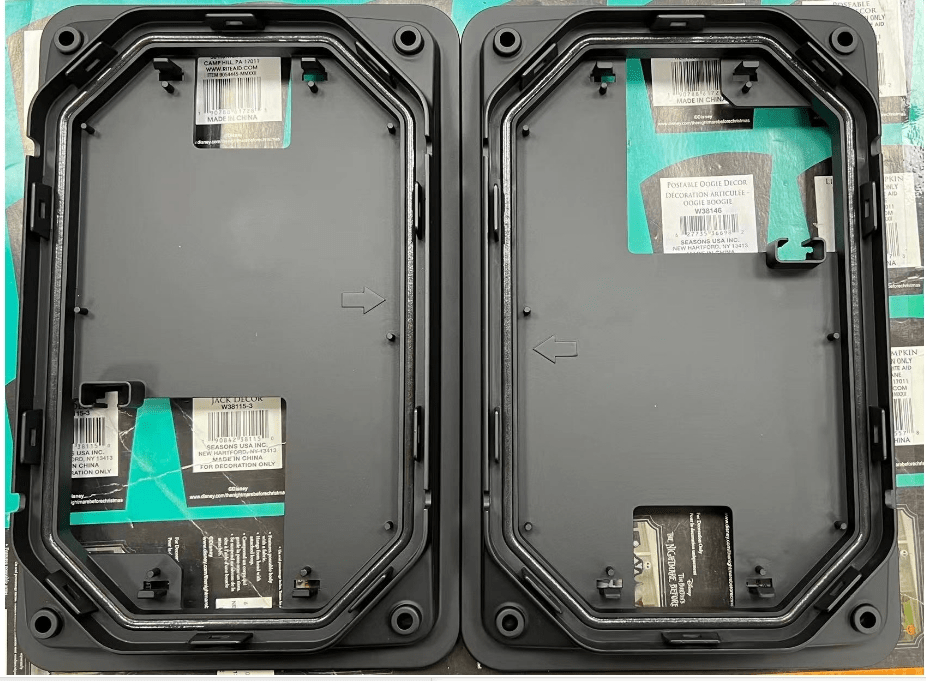
Caso 2: Cubierta de pantalla de grado marino – Resistencia a UV, agua salada y vibración Para las cubiertas de pantalla destinadas a aplicaciones marinas, que están expuestas a luz solar intensa, agua salada corrosiva y condiciones severas, seleccionamos cuidadosamente materiales adecuados para ambientes exteriores y marinos. Las propiedades clave incluyen resistencia a UV, resistencia al agua salada, alta fluidez, y resistencia a choques y vibraciones. Estos factores son cruciales en el diseño del molde, ya que afectan directamente el rendimiento y la contracción del producto final. Además, garantizar la planicidad de las superficies de sellado es esencial para un sellado confiable, especialmente al tratar con pantallas de vidrio o LCD. Los insertos para tornillos deben ser sobre moldeados con cuidado para evitar grietas, manchas o defectos, asegurando una integración sin costuras con la carcasa.
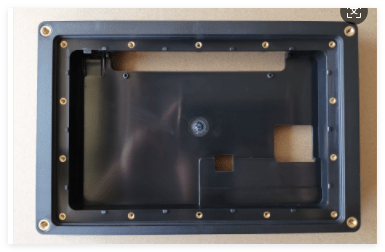
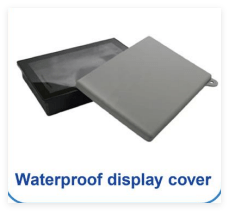
Caso 3: Sobremoldeo de plástico y acero inoxidable con solución impermeable En este caso, inicialmente intentamos soldadura ultrasónica para unir una parte de base de plástico con un componente de acero inoxidable. Sin embargo, debido al peso de la base, el producto se dañó durante el transporte. Para abordar esto, trabajamos estrechamente con el cliente para rediseñar la estructura, reemplazando la soldadura ultrasónica con un mecanismo de bloqueo por tornillo e incorporando una junta de silicona para mejorar la impermeabilidad.
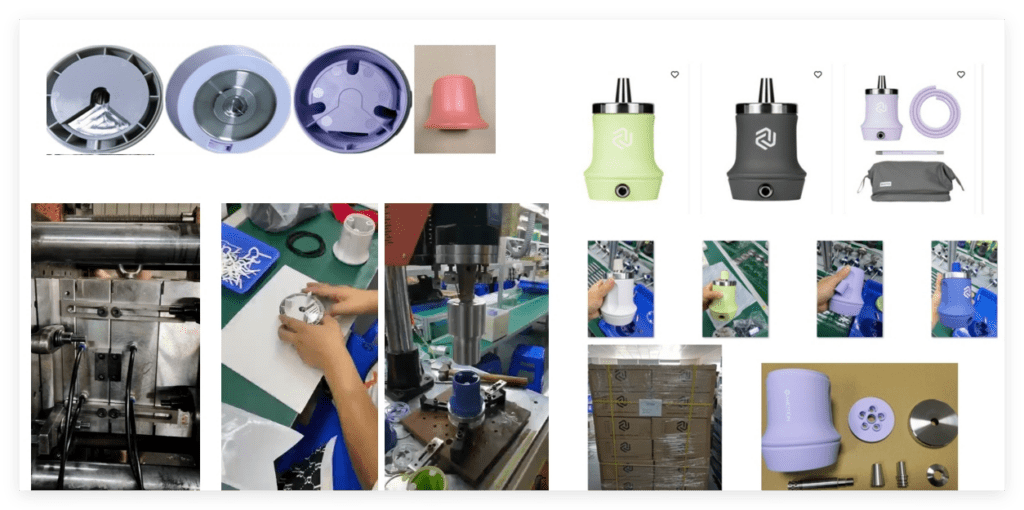
Caso 4: Tapas de goma TPU con sobremoldeo y soldadura ultrasónica Este caso presenta tapas de goma TPU moradas sobre moldeadas con una cubierta superior blanca. Las tuercas se moldean directamente en la tapa, y se utiliza soldadura ultrasónica para la columna de guía de luz. Las tapas de plástico de las teclas se pegan a la almohadilla de goma morada, y se aplica tratamiento UV a los caracteres impresos para aumentar la durabilidad, asegurando que puedan soportar hasta 1 millón de usos.
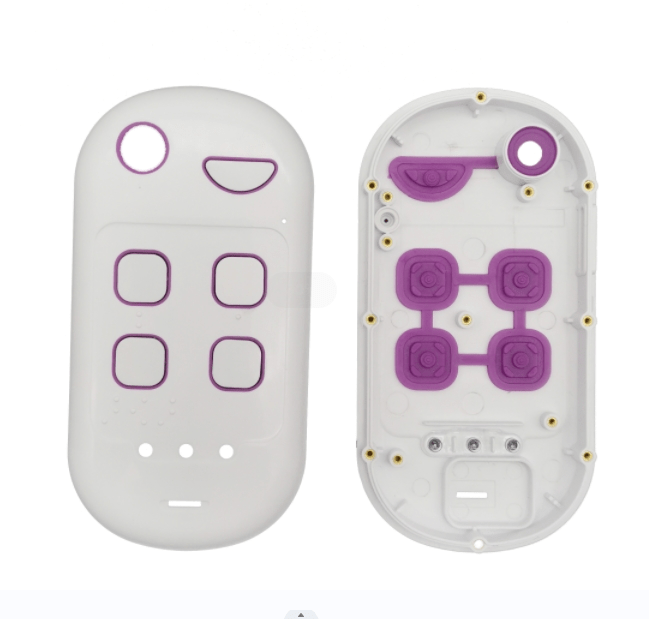