En la industria del moldeo por inyección, especialmente al trabajar con materiales especiales y productos de gran tamaño, existen costos ocultos y desafíos significativos. Muchos pueden no darse cuenta de que el moldeo por inyección no es solo un proceso de producción simple; implica una preparación, ajustes y afinaciones sustanciales para garantizar la calidad y estabilidad del producto. Esto es especialmente cierto durante la fase de producción de prueba, donde las fábricas enfrentan una presión tremenda.
- Los desafíos de los materiales especiales
Los materiales especiales, como las resinas resistentes a altas temperaturas, reforzadas con fibra de vidrio u otros plásticos funcionales, a menudo tienen puntos de fusión más altos y malas propiedades de flujo. Estas características requieren un control de temperatura más preciso y una fuerza de inyección adecuada durante el proceso de moldeo.
Estos materiales también tienen costos de compra y procesamiento más altos, y los equipos necesitan ser más especializados y ajustados finamente.
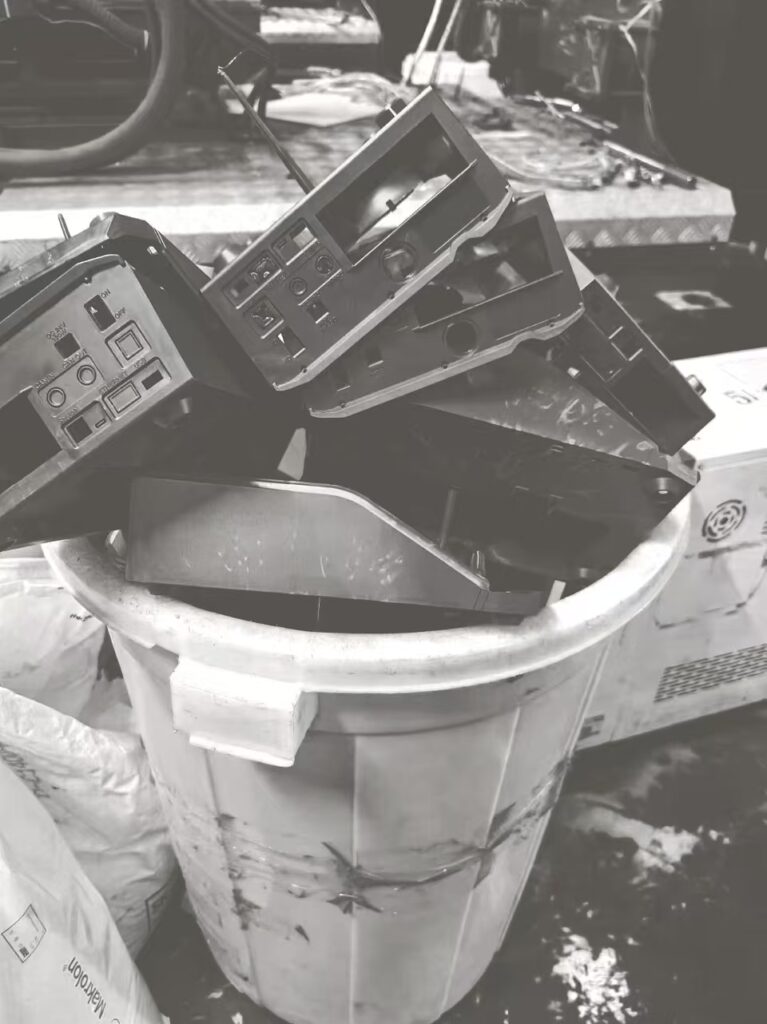
2. La complejidad de los productos de gran tamaño
Para los productos más grandes, la elección y ajuste de las máquinas de moldeo por inyección se vuelven más complejos. Las máquinas grandes no solo consumen más energía y requieren más mantenimiento, sino que también necesitan más tiempo para garantizar un funcionamiento estable.
A medida que aumenta el tamaño del producto, el diseño y la fabricación del molde se vuelven más complicados, lo que a menudo requiere múltiples modificaciones y ajustes.
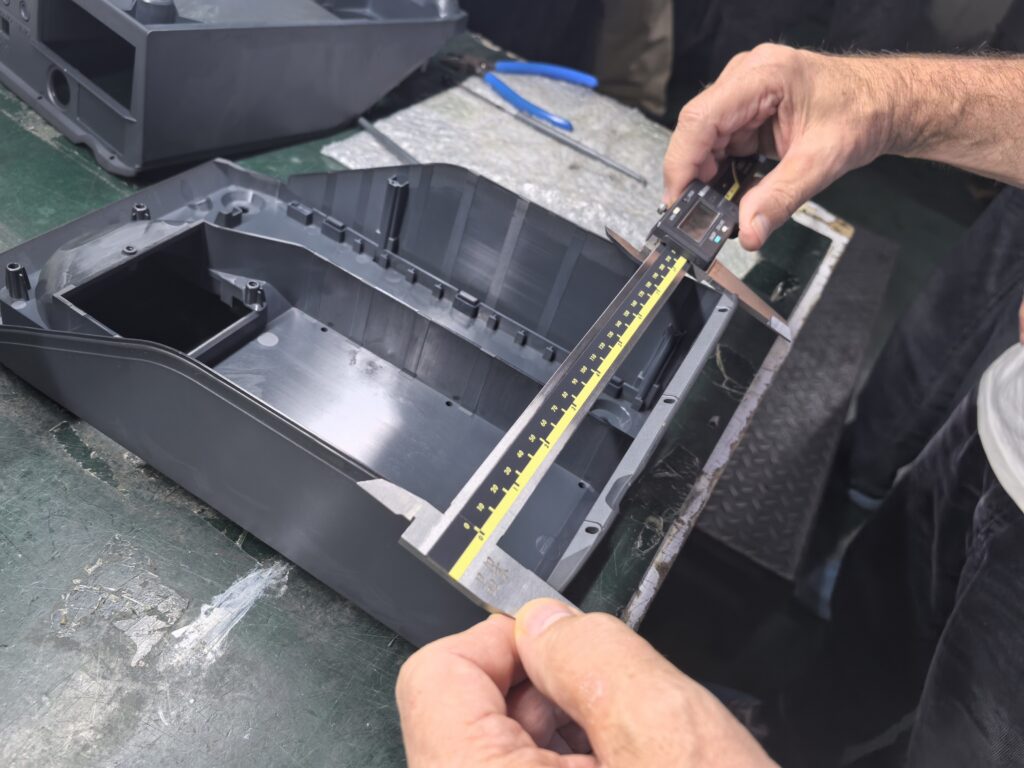
3. El costo de la producción de prueba
Durante la fase de producción de prueba, se consumen grandes cantidades de materias primas para ajustar los parámetros de la máquina. En el caso de materiales especiales, cada ajuste y optimización pueden generar desperdicio de material.
Debido a la complejidad de estos productos, el período de ajuste puede durar desde medio día hasta un día completo. Este tiempo, junto con la pérdida de material, genera mayores costos de producción.
4. Altos costos de mano de obra y equipos
Las fábricas de moldeo por inyección no solo invierten una gran cantidad de mano de obra para los ajustes de las máquinas y la producción, sino que también los costos laborales de los operadores e ingenieros están en constante aumento.
El uso y mantenimiento de grandes máquinas requieren una inversión considerable, y los costos operativos de estas máquinas afectan directamente el precio del producto.
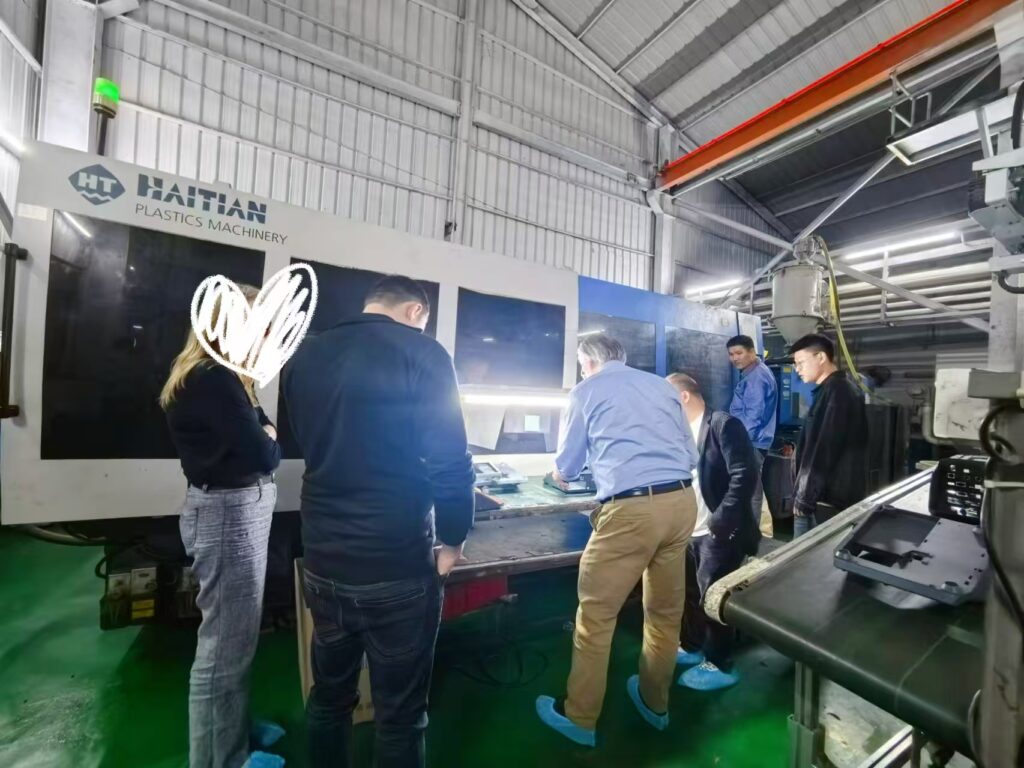
5. El dilema de los pedidos de prueba pequeños
Cuando se trata de pedidos de prueba pequeños, la eficiencia de la línea de producción disminuye significativamente. Debido a los altos costos del moldeo por inyección y el largo tiempo requerido para los ajustes, los pedidos pequeños no suelen ser rentables. A menudo, la fábrica termina ayudando a los clientes con pruebas de mercado a pequeña escala.
La producción en lotes pequeños no solo dificulta el control general de la producción, sino que, desde una perspectiva económica, a menudo no cubre los costos, dejando a las fábricas con pocas o ninguna ganancia.
Ante estos desafíos, las fábricas de moldeo por inyección deben no solo gestionar los altos costos, sino también centrarse en ajustar el control de producción para maximizar la eficiencia y minimizar el desperdicio. Los clientes deben comprender que, durante la producción de materiales especiales y productos de gran tamaño, es esencial una inversión razonable en costos y tiempo para garantizar la calidad del producto y la demanda del mercado.