CMF is the abbreviation for Color-Material-Finish, summarizing color, material, and surface finishing. It represents the organic integration of these three elements and is a design approach in industrial design that utilizes color, material, and process as design elements. Common surface treatment processes include IMD, OMD, spray coating, PVD, electroplating, NCVM, printing, laser engraving, etching, PPVD deposition, electrophoresis, sandblasting, rolling, etc. The purpose of surface treatment is to meet requirements for corrosion resistance, wear resistance, aesthetics, or other specific functions.
1. Surface Treatment Process — IMD
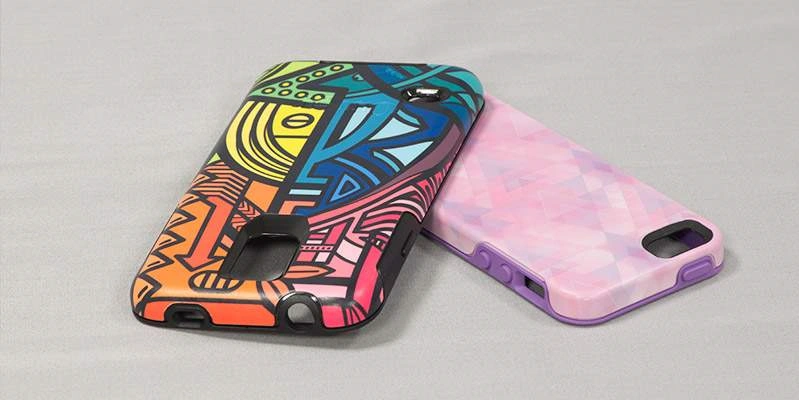
IMD (In-Mold Decoration), or non-painting technology, involves placing a pre-printed film into a metal mold, injecting resin into the mold, and fusing the printed film with the resin to form a single product. The surface consists of a hardened transparent film, a printed pattern layer in the middle, and a backing injection layer. This structure provides resistance to wear and scratches, ensuring vibrant colors that do not fade over time.
Features:
IMD simplifies production steps and reduces assembly components. Products made using IMD technology are corrosion-resistant, wear-resistant, non-peeling, brightly colored, and offer customizable patterns. They provide excellent surface decoration effects and are widely used in automotive, home appliances, consumer electronics, and medical electronics. IMD is an efficient and cost-effective processing technology.
2. Surface Treatment Process — OMD
OMD (Out-Mold Decoration) is an extension of IMD. It combines printing, texture, and metallization to create 3D surface decoration effects such as simulated metal brushing, wood grain, leather, and stone textures. It is suitable for 3D curved products with substantial height differences.
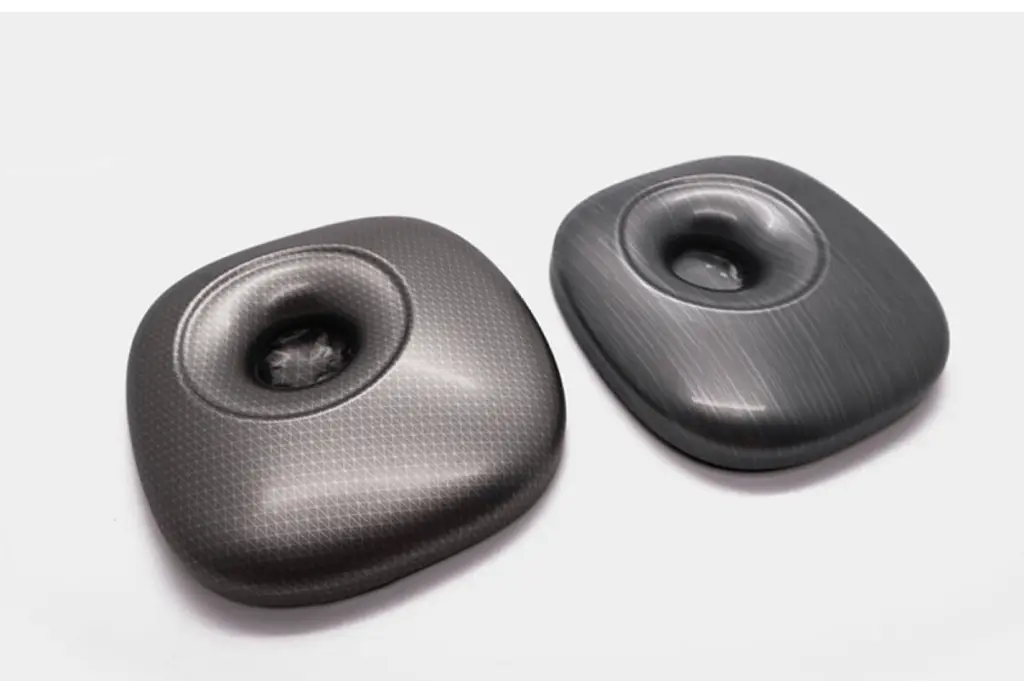
Features:
OMD is not limited by base material and can be applied to both metals and plastics. It enables 3D shaping and can integrate internal structures for smaller products in a single processing step. However, the equipment cost is high, and it cannot achieve very complex 3D shapes.
3. Surface Treatment Process — Spray Coating
Spray coating involves atomizing paint using spray guns or similar tools and applying it to the surface of workpieces. The paint is dispersed into fine droplets using pressure or centrifugal force, ensuring an even application on the surface.
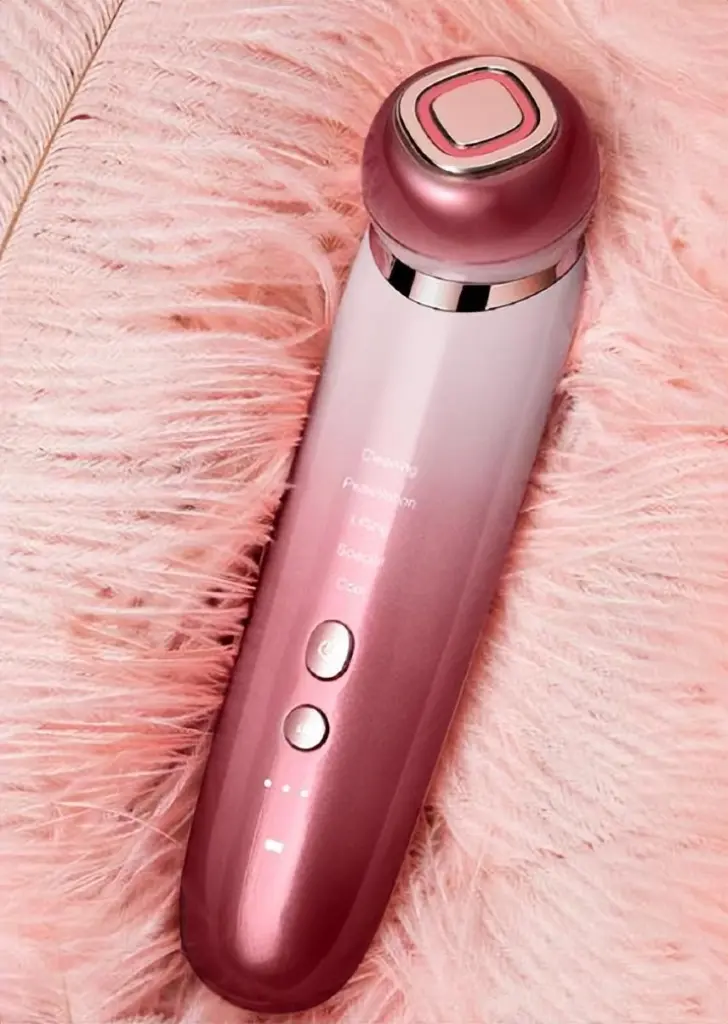
4. Surface Treatment Process — PVD
PVD (Physical Vapor Deposition) refers to a vacuum deposition process that uses low-voltage, high-current arc discharge technology. It ionizes the evaporated material and reactive gas, and the ions are accelerated by an electric field to deposit onto the workpiece, forming a coating.
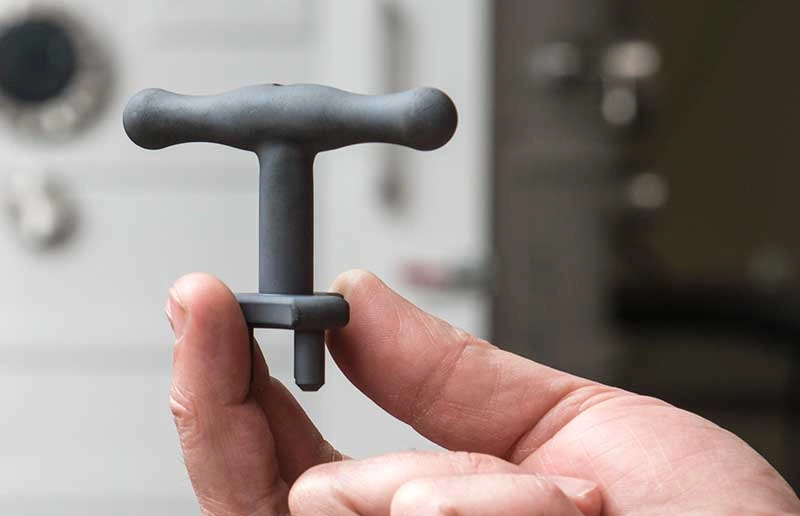
5. Surface Treatment Process — Electroplating
Electroplating provides a metallic surface effect on plastic components at a high yield and low cost. Unlike PVD, which relies on physical principles, electroplating is a chemical process. It includes vacuum plating and water electroplating.
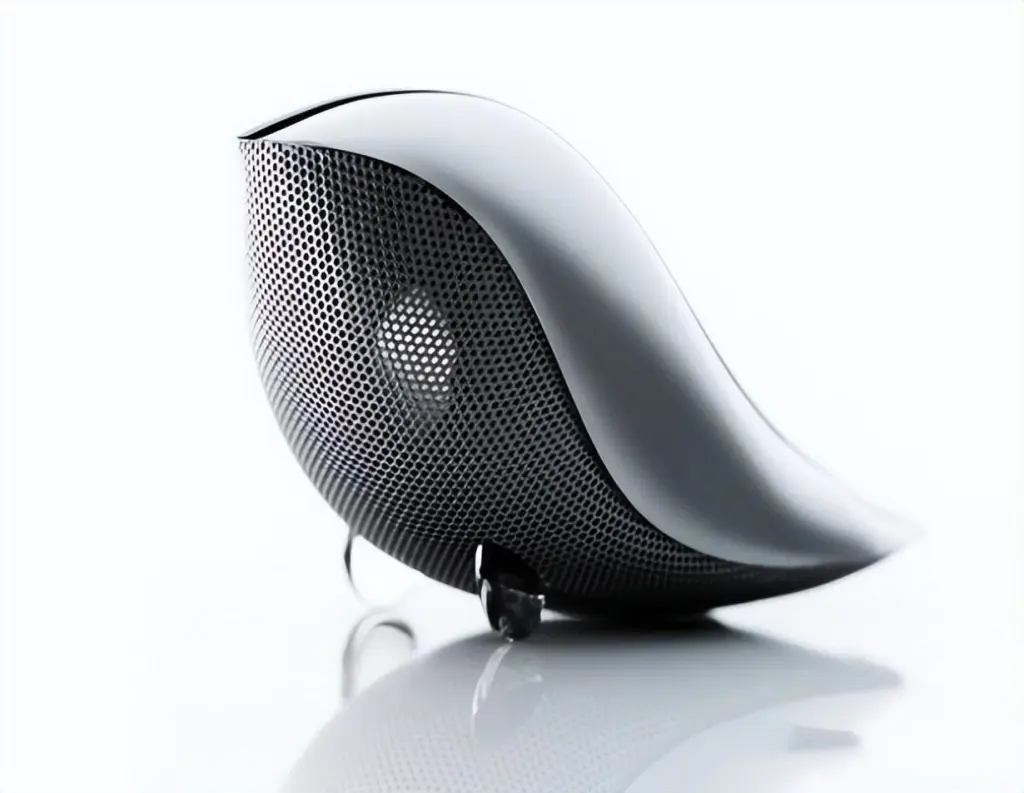
6. Surface Treatment Process — NCVM
NCVM (Non-Conductive Vacuum Metallization), also known as discontinuous or non-conductive plating, deposits thin films of metal and insulating compounds. The resulting product has a metallic appearance without interfering with wireless communication.
Features:
NCVM products are non-conductive, can withstand high-voltage tests, and offer a metallic appearance with controllable translucency.
7. Surface Treatment Process — Printing
Printing involves transferring patterns onto plastic surfaces using methods such as pad printing, screen printing, transfer printing, and heat transfer.
- Pad Printing: Uses silicone pads to transfer ink from an engraved plate to irregular surfaces.
- Screen Printing: Utilizes a mesh stencil to transfer ink through open areas of the stencil onto the substrate.
- Water Transfer Printing: Applies color patterns from transfer paper or film using water pressure.
- Heat Transfer Printing: Transfers digital patterns from a special transfer paper onto the product using high heat and pressure.
- Hot Stamping: A heat-transfer technique using a heated metal plate to emboss metallic foils onto the surface for decorative effects.
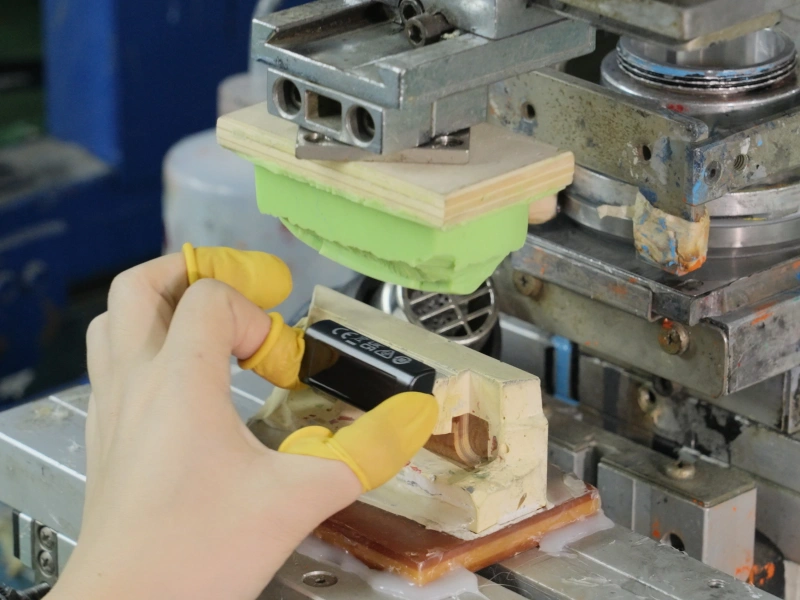
8. Surface Treatment Process — Laser Engraving
Laser Engraving (or Laser Marking) uses optical principles to engrave permanent markings on the surface or interior of transparent materials. It is cost-effective, flexible, precise, and permanent.
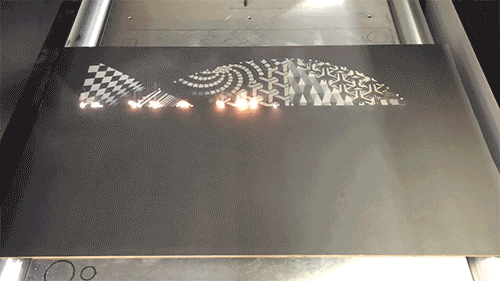
9. Surface Treatment Process — Etching
Etching uses chemical reactions or physical abrasion to remove material, creating textured or embossed designs on metal surfaces.
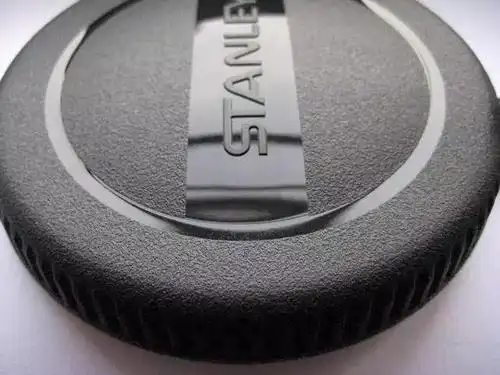
10. Surface Treatment Process — PPVD Deposition
PPVD deposition involves vacuum evaporation followed by selective removal of unwanted areas using film exposure and chemical solutions to create patterns. Commonly used for battery covers.
11. Surface Treatment Process — Electrophoresis
Electrophoresis involves charged particles moving toward an electrode of opposite charge under an electric field, often used for coating applications.
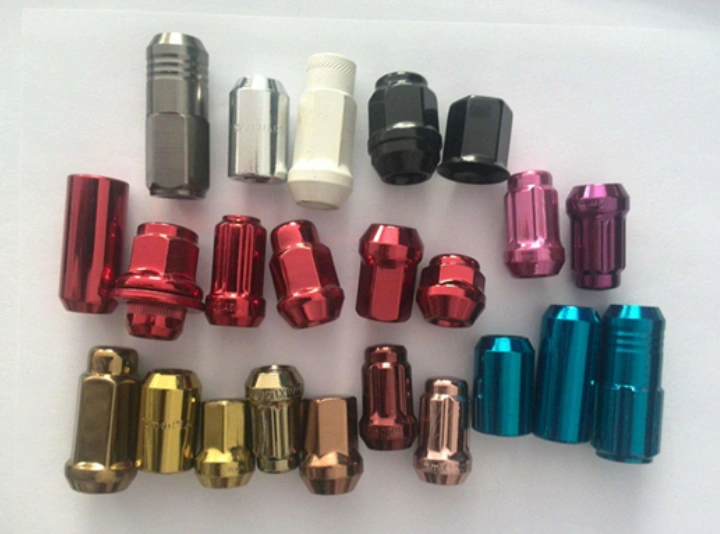
12. Surface Finishing Process – Etching
Etching: The technique of removing materials through chemical reactions or physical impacts. Often referred to as photo-chemical etching, it involves exposing and developing the areas to be etched, then contacting chemical solutions during etching to dissolve the material and create recessed or hollow shapes.
13. Surface Finishing Process – Sandblasting
Sandblasting: Uses compressed air to create a high-speed jet of abrasive materials (such as copper slag, quartz sand, emery, iron sand, and sea sand) to the surface of the workpiece, changing its surface or shape. The abrasive impact and cutting action improve the workpiece’s cleanliness, roughness, and mechanical properties, thus increasing fatigue resistance, coating adhesion, durability, leveling, and decorative quality.
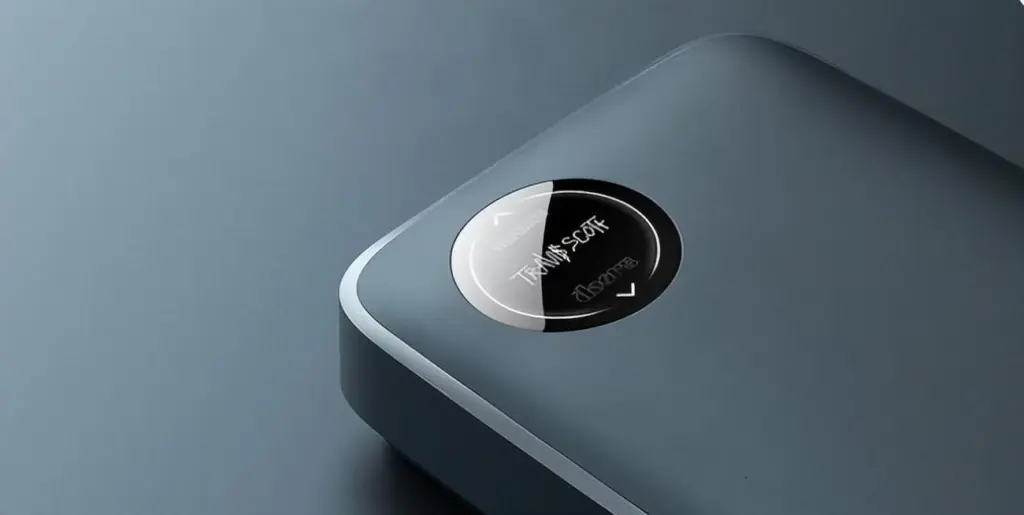
14. Surface Finishing Process – Rolling
Rolling: Also known as calendering. The final process in leather finishing involves utilizing the plasticity of fibers under mixed heating to flatten or create parallel fine lines on the fabric surface, enhancing its luster. After being fed, the material is heated, melted, shaped into sheets or films, and then cooled and rolled. The most commonly used calendering material is polyvinyl chloride. or create parallel fine lines for a glossy finish. Commonly used for PVC and similar materials.