Injection molding has long been a stalwart of manufacturing, offering unparalleled efficiency, precision, and versatility. However, the landscape of injection molding is constantly evolving, driven by a relentless pursuit of innovation and technological advancement. In this blog, we’ll explore some of the latest breakthroughs and advancements in injection molding technology that are reshaping the industry.
- 3D Printing Integration: One of the most exciting developments in injection molding technology is the integration of 3D printing, also known as additive manufacturing. By combining 3D printing with traditional injection molding processes, manufacturers can create custom molds with intricate geometries and complex cooling channels that were previously impossible or impractical to produce using conventional methods. This convergence of technologies offers greater design freedom, reduced lead times, and cost savings in tooling production.
- Automation and Robotics: Automation has been a game-changer in injection molding, streamlining production processes, reducing labor costs, and improving efficiency. Advanced robotics and automation systems are being increasingly deployed in injection molding facilities to handle tasks such as part removal, quality inspection, and packaging. Collaborative robots, or cobots, are also being used to work alongside human operators, enhancing safety and productivity on the factory floor.
- Sustainable Initiatives: In response to growing environmental concerns, the injection molding industry is embracing sustainable practices and eco-friendly materials. Manufacturers are adopting closed-loop recycling systems to minimize waste and improve resource efficiency. Bio-based and recycled materials are being incorporated into injection molding processes, reducing reliance on virgin plastics and mitigating environmental impact. Additionally, advancements in energy-efficient machinery and processes are helping to lower carbon emissions and promote sustainability throughout the supply chain.
- Digital Twin Technology: Digital twin technology is revolutionizing the way injection molding tools are designed, simulated, and optimized. By creating a virtual replica, or digital twin, of the injection molding process, manufacturers can conduct real-time simulations to predict and optimize part quality, cycle times, and material usage. Digital twins enable iterative design improvements, allowing engineers to fine-tune mold designs and process parameters before physical production begins, reducing time-to-market and minimizing costly errors.
- Smart Manufacturing and IoT Integration: The rise of Industry 4.0 has ushered in a new era of smart manufacturing in the injection molding industry. IoT (Internet of Things) sensors embedded within injection molding machines and molds collect real-time data on key process parameters such as temperature, pressure, and cycle times. This data is then analyzed using advanced analytics and machine learning algorithms to optimize production efficiency, prevent defects, and maximize equipment uptime. Predictive maintenance algorithms can also anticipate equipment failures before they occur, reducing downtime and minimizing disruption to production schedules.
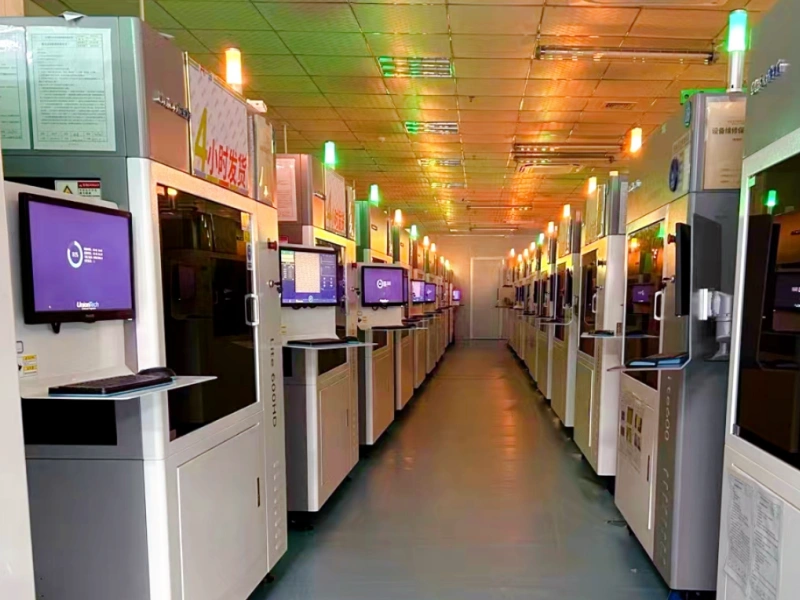
Conclusion: As we look to the future of injection molding, the pace of technological innovation shows no signs of slowing down. From 3D printing integration and automation to sustainability initiatives and digital twin technology, these advancements are driving efficiency, quality, and sustainability across the injection molding industry. By embracing these cutting-edge technologies, manufacturers can stay ahead of the curve and unlock new possibilities for innovation and growth in t