One, Overview
Die casting is a metal casting process in which molten metal is pressed into a mold and cooled to solidify into the desired shape of a part. Among the two metals, zinc alloy and aluminum alloy are commonly used for die casting production due to their good fluidity, mechanical properties, and economic advantages. In this article, we will delve into the differences between zinc alloy die casting and aluminum alloy die casting and their respective advantages.
Two. Differences Between Zinc Alloy Die Castings and Aluminum Alloy Die Castings
1. Chemical composition and physical properties: Zinc alloy is an alloy made of zinc and other metals such as aluminum and copper. Aluminum alloy, on the other hand, is an alloy based on aluminum and usually contains other metal elements such as copper and magnesium. The physical properties (such as density and thermal conductivity) of the two alloys are different, leading to differences in their areas of application.
2. Process characteristics: During the die casting process, the cooling time of zinc alloy castings is relatively short, and the solidification speed is faster, so the thermal stress on the mold is higher during production. Aluminum alloy castings have a longer cooling time, which is beneficial for producing more complex shapes and larger sizes.
3. Application areas: Due to different physical properties and process characteristics, zinc alloy and aluminum alloy have different areas of application. Zinc alloy is often used to produce lightweight, high-strength components, such as automotive components and electronic equipment housings. Aluminum alloy, on the other hand, is widely used in aviation, automotive, and construction industries due to its good corrosion resistance, recyclability, etc.
Three. Advantages of Zinc Alloy Die Casting and Aluminum Alloy Die Casting
1. Advantages of Zinc Alloy Die Casting:
(1) High strength and lightweight: Zinc alloy has a relatively low density, but it has high strength, which makes zinc alloy castings lightweight, allowing for a reduction in the overall weight of the product.
(2) Good mechanical properties: Zinc alloy has good ductility, impact resistance, and wear resistance, which makes it perform well in situations where heavy loads and impacts are present.
(3) Excellent casting properties: Zinc alloy has good fluidity, making it easy to fill complex shapes in molds, which is beneficial for producing structurally complex parts.
(4) Cost advantage: Compared to aluminum alloy, zinc alloy is relatively cheaper, which helps reduce production costs.
2. Advantages of aluminum alloy die casting:
(1) Corrosion resistance: Aluminum alloy has good corrosion resistance and can be used for a long time in humid and corrosive environments without easily rusting.
(2) Recyclability: Aluminum alloy can be recycled, which is in line with the green and environmentally friendly production concept.
(3) High precision and surface quality: Aluminum alloy castings have high dimensional accuracy and surface quality, which can meet the production needs of high-quality parts with high requirements.
(4) Good thermal conductivity and electrical conductivity: The thermal conductivity and electrical conductivity of aluminum alloy are good, making it suitable for applications that require good electrical and thermal conductivity.
Four. Conclusion
In summary, zinc alloy and aluminum alloy castings have their own unique features and advantages. The choice of which material to use for casting production depends on specific application requirements, performance requirements, and cost considerations. With the advancement of technology and process improvements, the use of these materials in casting will become more widespread, providing more high-quality parts for various industries.
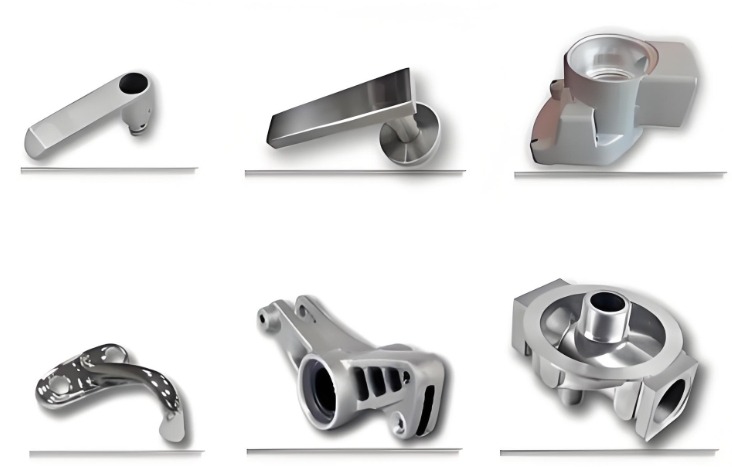