In today’s competitive business landscape, managing quality is not just a nice-to-have—it’s a must-have. But what exactly does the Cost of Quality (CoQ) entail, and how can it impact your business?
What is the Cost of Quality (CoQ)?
The Cost of Quality represents the total cost of ensuring products and services meet quality standards. It’s divided into two major categories:
Cost of Conformance
These are the costs associated with preventing defects and ensuring that processes run smoothly, such as training, equipment maintenance, and process controls.
Cost of Non-Conformance
These are the costs that arise when things go wrong, such as rework, scrap, warranty claims, and lost customers. This is where things can get expensive.
The 1:10:100 Rule
This rule illustrates how the cost of quality issues increases exponentially the further along they are detected in the process:
$1 for Prevention: If you invest $1 in preventing issues upfront, whether through employee training or process improvements, you’re setting up the foundation for better results.
$10 for Detection: If you fail to prevent, the cost rises to $10 when defects are detected within the system (e.g., during an internal audit or inspection).
$100 for Failure: If defects are not detected and end up in the hands of the customer, the cost skyrockets to $100 due to rework, recalls, or brand damage. This could even impact customer trust, which is priceless.
Importance of Managing Cost of Quality
1.Improved Customer Satisfaction
Keeping the Cost of Conformance low ensures high-quality products, leading to satisfied customers and repeat business.
2.Boosting Profit Margins
Investing in prevention upfront saves on expensive rework or returns, positively impacting your bottom line.
3.Brand Reputation
Controlling quality costs ensures consistency, which preserves the trust customers have in your brand.
4.Increased Operational Efficiency
When quality is managed effectively, it leads to smoother processes, fewer defects, and improved operational efficiency.
My Perspective: Having worked extensively in quality management, I’ve seen firsthand how organizations that focus on prevention rather than fixing problems later benefit immensely. The 1:10:100 rule serves as a stark reminder that the further an issue goes undetected, the more costly it becomes. Proactively managing the Cost of Quality is essential for long-term success.
Let’s reduce costs and improve customer satisfaction together!
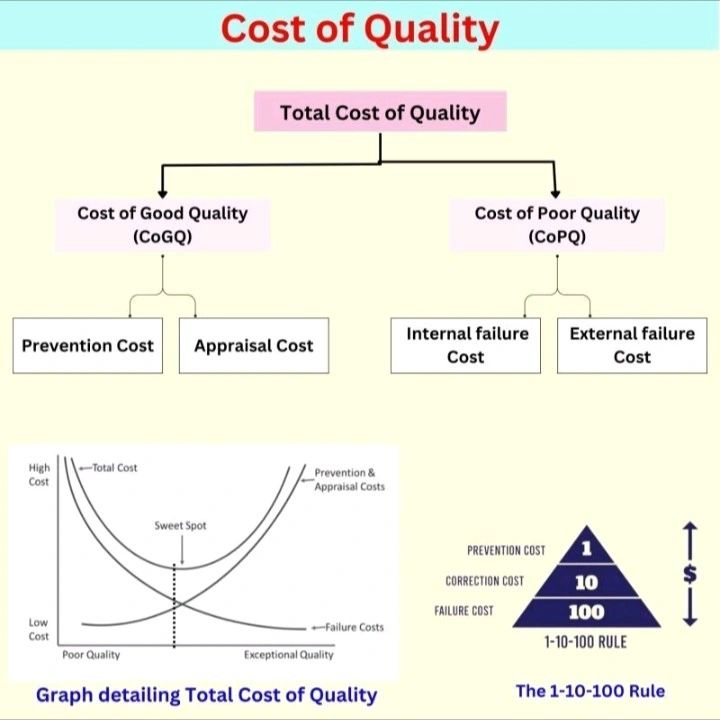