When designing parts, it’s best to consider the manufacturing process in advance and optimize the design accordingly for that process.
For plastic parts, the most common manufacturing methods are CNC machining and injection molding. So, how do we choose between these two processes?
1. CNC Machining
CNC machining generally starts with a solid block of material and removes material through multiple stages to achieve the desired shape.
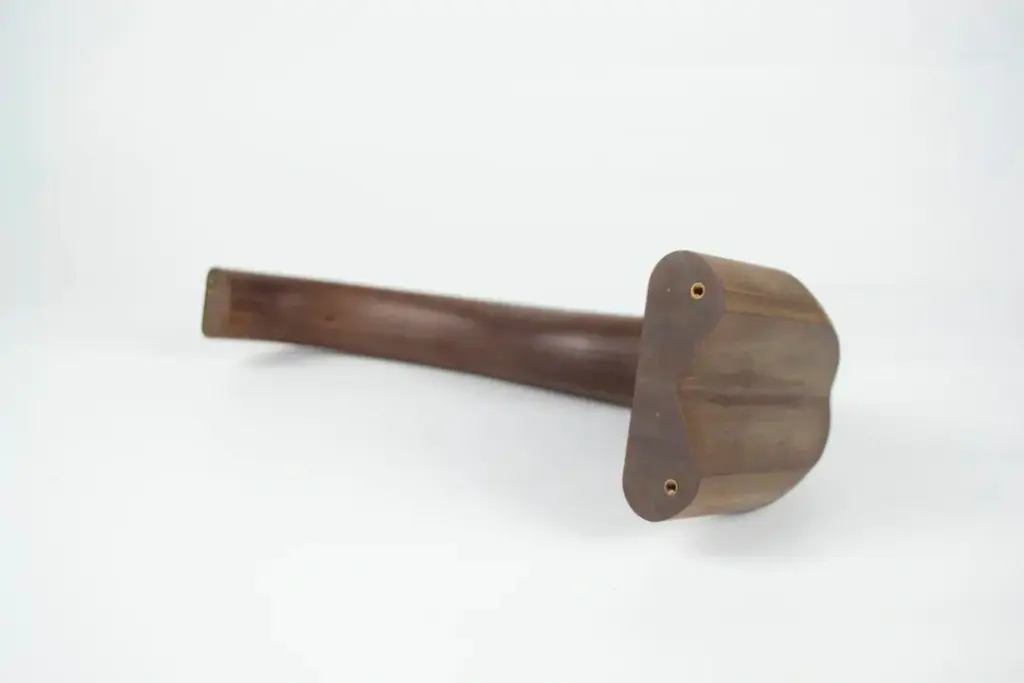
CNC plastic machining is one of the main methods for making prototype models, commonly using materials like ABS, PC, PA, PMMA, and POM to produce the desired physical samples.
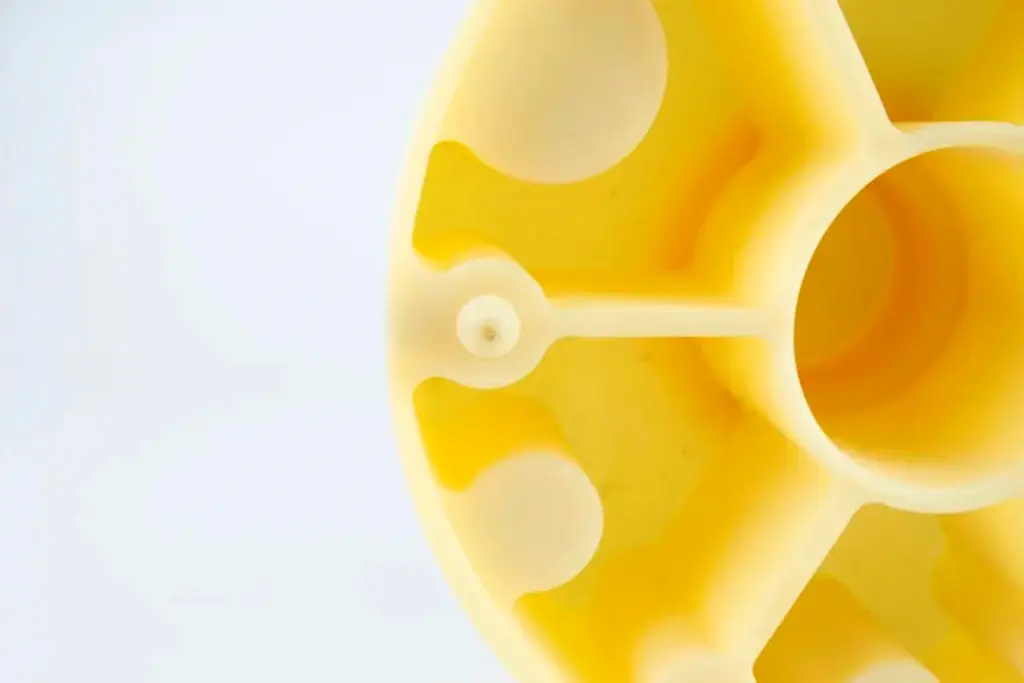
CNC-machined parts offer advantages such as larger forming size, high strength, good toughness, and low cost, making it a mainstream approach for prototyping.
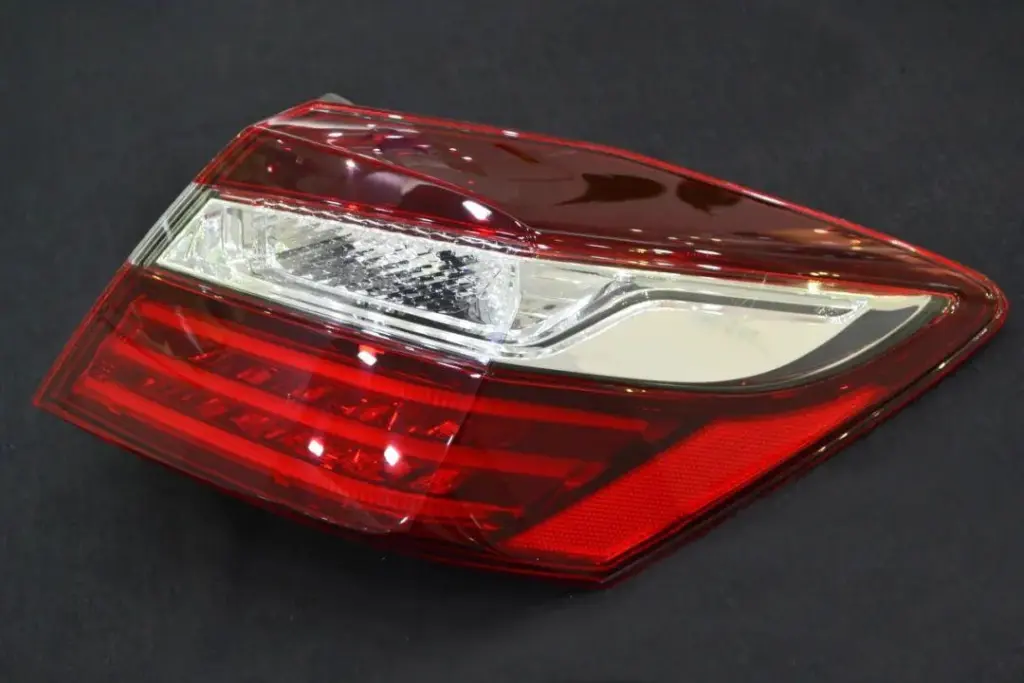
However, for complex plastic parts, CNC machining may encounter limitations or higher costs due to manufacturing constraints.
2. Injection Molding
Injection molding involves melting plastic pellets and injecting the liquid plastic into a mold under high pressure to create parts once it cools.
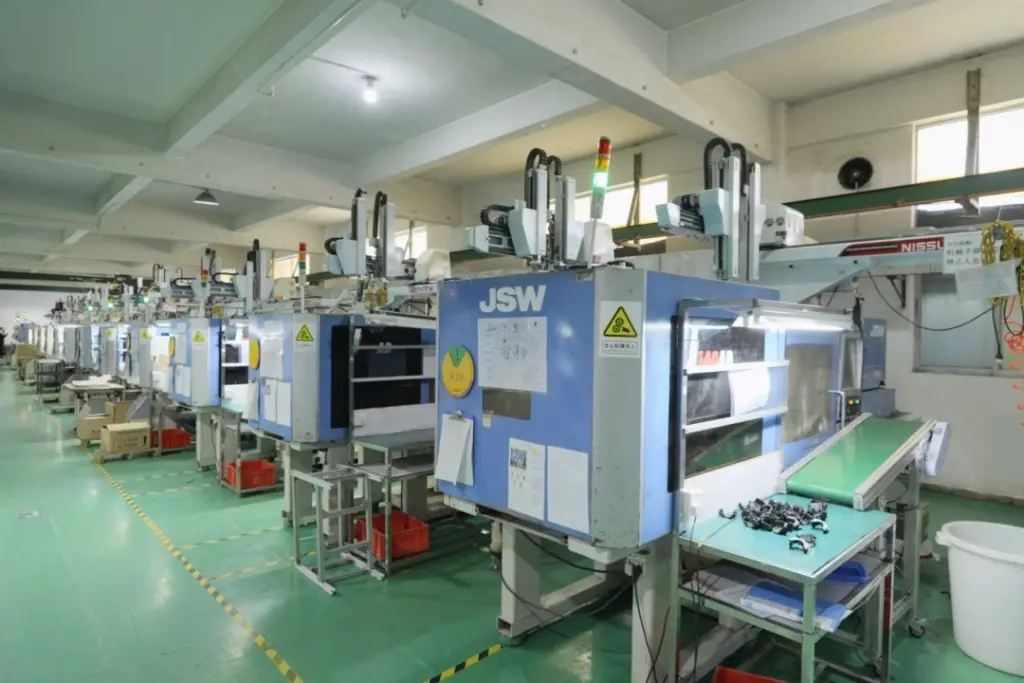
Advantages of Injection Molding:
- Suitable for high-volume production.
- Capable of processing soft materials like TPE and rubber.
Disadvantages of Injection Molding:
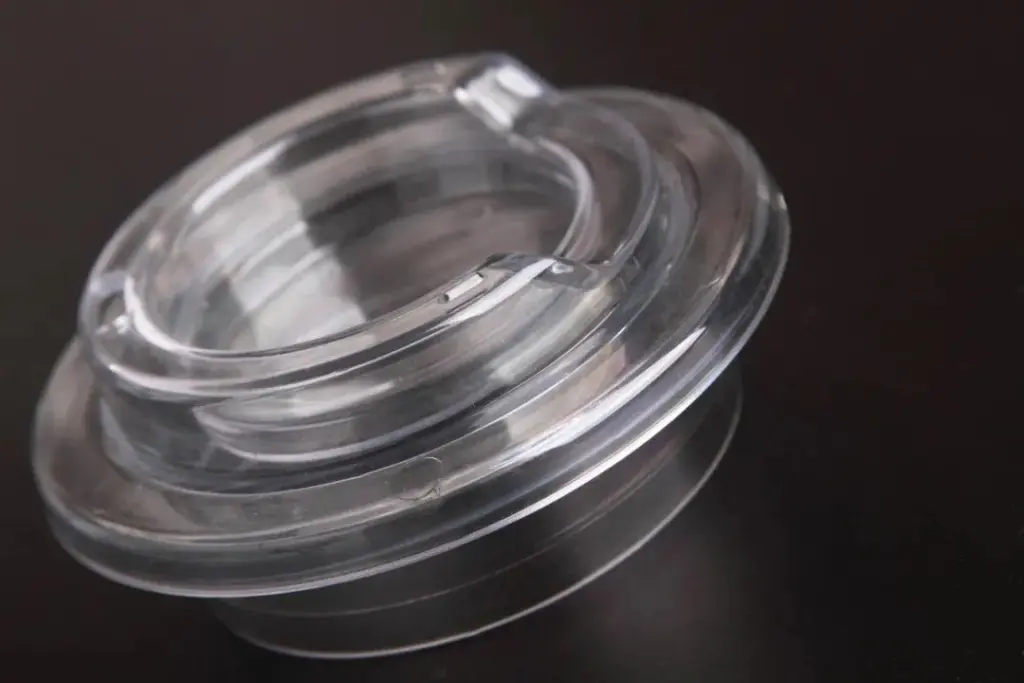
- High mold costs result in higher startup costs. While the per-unit cost decreases with higher production volumes, low quantities can make injection molding expensive per part.
- High part modification costs, as changes require adjustments to the mold.
- If the mold has multiple components, bubbles, and defects may occur during injection.
3. Which Process to Choose
Choosing the right process generally involves balancing factors such as speed/quantity, cost, and material.
01. Speed/Quantity
For small quantities, CNC machining is faster. If you need 10 parts within two weeks, CNC is the way to go. If you need 50,000 parts within four months, injection molding is the better option.

Injection molding requires time to create the mold and ensure parts meet tolerance standards, which can take weeks or even months. Once the mold is ready, however, producing parts is very fast.
02. Cost
Cost efficiency depends on the quantity. For a few to a few hundred parts, CNC is cheaper. When the production volume reaches a certain level, injection molding becomes more cost-effective. Note that injection molding costs need to account for mold expenses.
03. Material
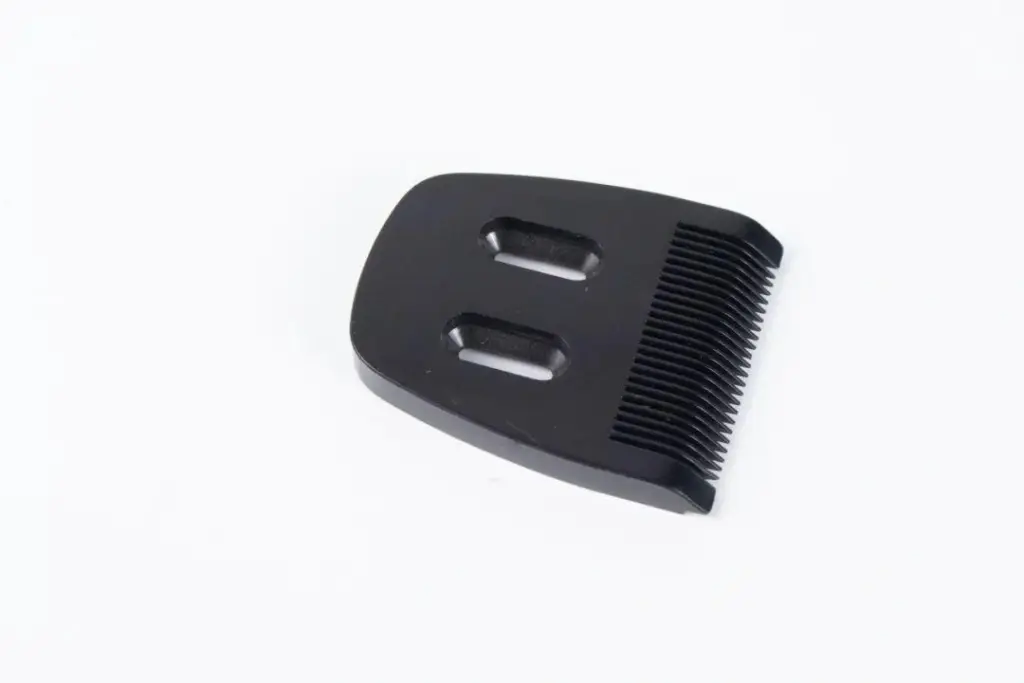
CNC machining supports a broader range of materials, particularly high-performance or specialized plastics, but it struggles with soft materials.
Injection molding supports fewer materials but is effective for processing soft materials.
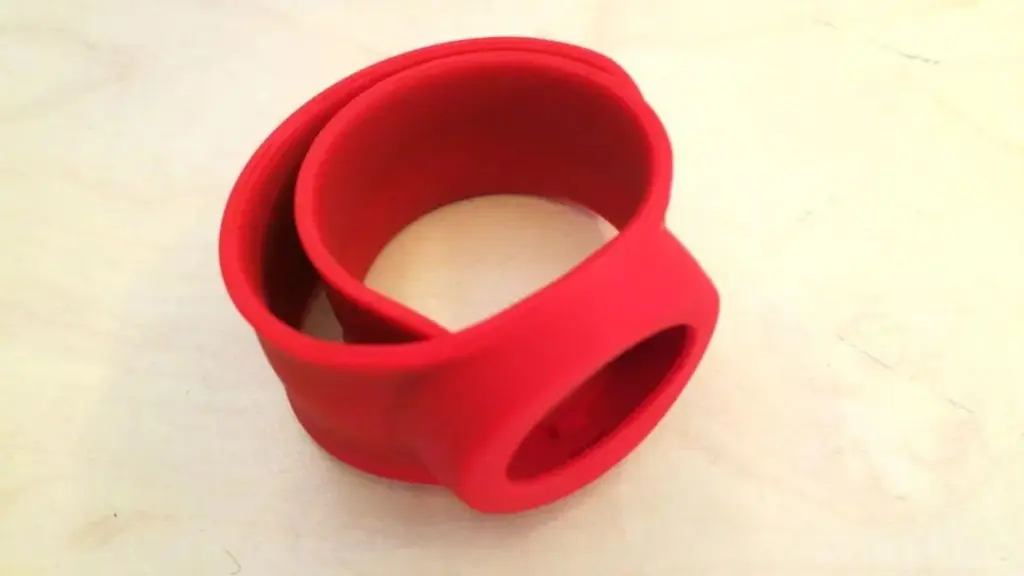
From the above, it’s clear that both CNC and injection molding have distinct advantages and disadvantages. Choosing the right process primarily involves weighing speed/quantity, cost, and material suitability.