Molds are tools used in industrial production to create desired products through various methods such as injection molding, blow molding, extrusion, die casting, forging, smelting, and stamping. In simple terms, molds are tools designed for shaping items. They are made up of various parts, with each mold requiring different components. Molds primarily change the physical state of the material to shape the product, earning them the title “Mother of Industry.”
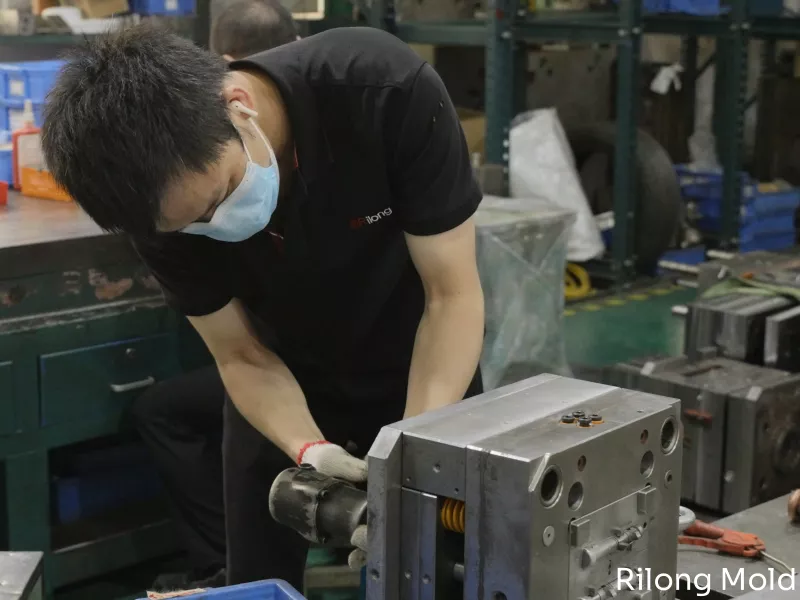
Types of Molds
Molds come in many types and can be classified according to the material processed and the process applied:
- Metal Processing Molds
- Non-metal and Powder Metallurgy Molds: These include plastic molds (like two-color molds, compression molds, and extrusion molds), rubber molds, and powder metallurgy molds. Based on structural features, molds can be divided into flat punching dies and cavity molds. Most molds are produced individually or in small batches.
Production Process
mold is essentially a model used to create products according to its shape. But how is a mold produced? Besides mold professionals, most people might not be able to answer this. Molds have become indispensable in our lives, with most of our daily items relying on them. Items like computers, telephones, fax machines, keyboards, and cups are all produced using molds, not to mention the outer covers of car and motorcycle engines. For a single car, more than 20,000 different molds are needed. Thus, the role of molds in modern life is irreplaceable. As long as there is mass production, molds are essential.
Steps in Modern Mold Production:
- Early Supplier Involvement (ESI): At this stage, technical discussions occur between the customer and supplier about product design and mold development, ensuring mutual understanding of design intent and manufacturing feasibility.
- Quotation: This includes mold price, lifespan, turnover process, machine requirements, and delivery timeline.
- Purchase Order (PO): The issuance and acceptance of the order and payment.
- Production Planning and Scheduling: Scheduling the delivery date for the mold.
- Design: Design software such as Pro/Engineer, UG, SolidWorks, AutoCAD, and CATIA are commonly used.
- Material Procurement
- Machining: This includes turning, milling, heat treatment, grinding, CNC machining, EDM, wire cutting, jig grinding, laser engraving, and polishing.
- Assembly
- Trial Run
- Sample Evaluation Report (SER)
- Approval of SER
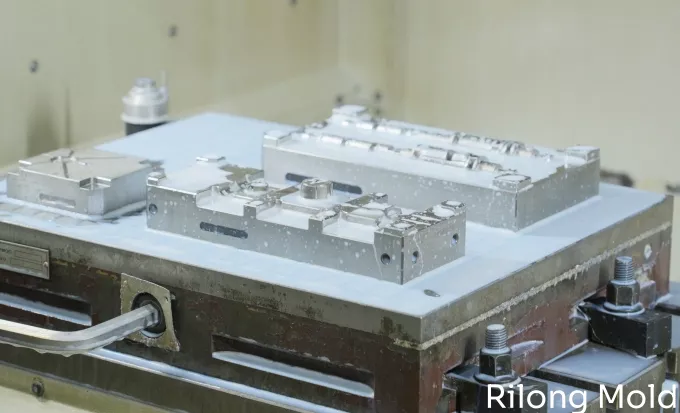
Mold Manufacturing
The requirements for mold design and manufacturing are as follows: precise dimensions, smooth surfaces, reasonable structure, high production efficiency, easy automation, ease of manufacturing, long lifespan, and low cost. The design should meet process requirements and be economically efficient.
When designing mold structure and selecting parameters, factors such as rigidity, guidance, ejection mechanisms, positioning methods, and clearance sizes must be considered. Replaceable components should be easy to swap out. For plastic and die-casting molds, factors such as a well-designed gating system, the flow behavior of molten plastic or metal, and the position and direction of entry into the cavity should also be taken into account. Multi-cavity molds can be used to improve production efficiency and reduce runner material waste, allowing multiple identical or different products to be produced in a single mold. High-efficiency, high-precision, and long-lasting molds are recommended for mass production.
Progressive stamping molds should use multi-station progressive designs or hard alloy inserts to enhance durability. In small-batch production or the trial production of new products, simpler molds that are quick to manufacture and low in cost are preferable, such as modular punches, sheet punches, polyurethane rubber molds, low-melting-point alloy molds, zinc alloy molds, and superplastic alloy molds. Computer-aided design (CAD) is now widely used for optimizing mold design, marking a key development in mold design.
Based on structural characteristics, molds are classified into planar blanking molds and cavity molds. Planar blanking molds rely on precise matching of punch and die dimensions, sometimes requiring zero clearance. Other forging molds, such as cold extrusion molds, die-casting molds, powder metallurgy molds, plastic molds, and rubber molds, are all cavity molds used for shaping three-dimensional parts. Cavity molds have dimensional requirements in length, width, and height, are complex in shape, and are challenging to manufacture. Mold production is typically single-item or small-batch with strict accuracy requirements, often utilizing precise machining equipment and measuring instruments.
Planar blanking molds can use electric discharge machining (EDM) for preliminary shaping, followed by contour grinding and jig grinding for enhanced precision. Contour grinding can be done on optical projection curve grinders, flat grinders with profile shaping, or precision surface grinders using specialized grinding tools. Jig grinders can precisely position molds, ensuring hole diameter and spacing accuracy. CNC coordinate grinders can also be used to grind complex curves for punches and dies. Cavity molds often use profiling mills, EDM, and electrolytic machining. The integration of profiling milling with CNC and the addition of three-way head movement to EDM can enhance cavity processing quality. Inflated electrolytic processing improves efficiency in electrolytic machining.
Common Software
- Plastic Molds: EMX, NXMoldWizard, CimatronE, DelcamMoldmaker, TopsolidMold, MoldDesign, Manusoft’s IMOLD, MoldWorks
- Metal Molds: PDX, NXProgressiveDieDesign, Logopress3, 3DQuickPress, MoldWorks, TopsolidProgress.
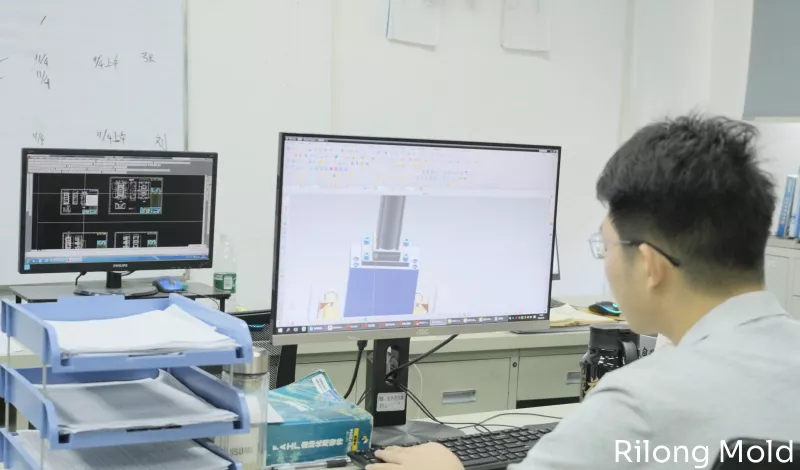
Process Performance
The manufacturing of molds generally involves several processes, such as forging, machining, and heat treatment. To ensure mold quality and reduce production costs, the material should possess good forgeability, machinability, hardenability, hardenability depth, and grindability. It should also exhibit low sensitivity to oxidation, decarburization, and quenching deformation and cracking.
Grindability: The material should cause low wear on grinding wheels, allow high grinding capacity without burning, and have low sensitivity to grinding wheel quality and cooling conditions, with minimal risk of grinding burns or cracks.
Forgeability: The material should have low resistance to deformation during hot forging, good plasticity, a wide forging temperature range, and low tendencies for forging and cold cracking as well as minimal carbide precipitation.
Annealing Processability: It should have a wide spheroidizing annealing temperature range, low annealed hardness with minimal fluctuations, and high spheroidization rates.
Machinability: The material should allow for high cutting volumes, low tool wear, and a low surface roughness after machining.
Oxidation and Decarburization Sensitivity: The material should exhibit good resistance to oxidation at high temperatures, a slow decarburization rate, low sensitivity to the heating medium, and minimal pitting tendencies.
Hardenability: The material should achieve a uniform and high surface hardness after quenching.
Hardenability Depth: The material should achieve a deep hardened layer after quenching, even with mild quenching media.
Tendency for Quenching Deformation and Cracking: The material should exhibit minimal volume change, slight warping, and low tendency for abnormal distortion after conventional quenching, as well as low sensitivity to quenching cracks. It should also be relatively insensitive to quenching temperatures and the shape of the workpiece.
Performance Characteristics
Low Density: Plastics have a low density, which is essential for reducing the weight of machinery and equipment and for saving energy, particularly in vehicles, ships, airplanes, and spacecraft.
High Specific Strength and Stiffness: Although plastics do not have as high absolute strength as metals, their low density gives them a high specific strength (σb/ρ) and specific stiffness (E/ρ). This is especially true for reinforced plastics made with high-strength fibrous, flaky, or powdered metal or non-metal fillers, which offer specific strength and stiffness even greater than metals.
Good Chemical Stability: Most plastics have excellent resistance to acids, alkalis, salts, water, and gases, and they generally do not react chemically with these substances under normal conditions.
Good Electrical Insulation, Thermal Insulation, and Sound Insulation.
Wear Resistance and Self-Lubricating Properties: Plastics have a low friction coefficient, good wear resistance, and self-lubricating properties. Combined with high specific strength and low transmission noise, plastics work effectively under conditions with liquid media, semi-dry, or even dry friction. This makes them ideal for machine parts like bearings, gears, cams, and pulleys, especially in applications with moderate speeds and light loads.
Strong Adhesion Properties.
Good Molding and Coloring Properties.
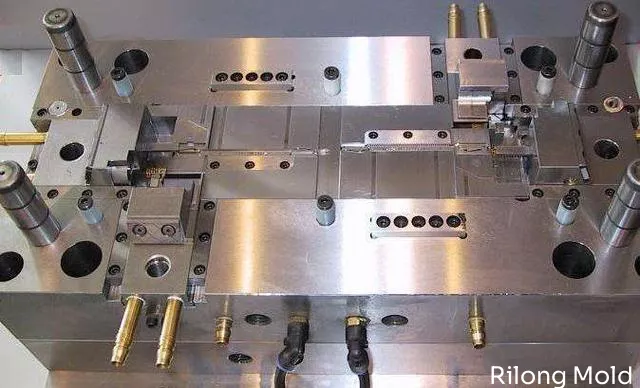
Maintenance and Care
Sharpening the Cutting Edge: After extended use, the cutting edge of the mold must be sharpened. After grinding, the edge must be demagnetized to prevent material blockage due to residual magnetism. Mold users need to keep detailed records and statistics of mold usage, maintenance (lubrication, cleaning, rust prevention), and damage. This helps identify worn or damaged parts and provides data to troubleshoot and improve the molding process, reducing trial time and boosting efficiency. During normal mold operation, test various mold functions and measure the final product’s dimensions to assess the mold’s condition. This information can help locate damage to components like cavities, cores, cooling systems, and parting surfaces, guiding maintenance and repair actions.
Spring and Elastic Part Replacement: Springs are prone to breakage and deformation. Replace them with springs of the same specification and model, identified by color, outer diameter, and length. Only if all three match should the replacement be made. Imported springs are generally of better quality.
Punch Head and Punch Bushing Maintenance: Punch heads often suffer breakage, bending, and chipping, with punch bushings typically chipping as well. These are generally replaced with parts of the same specifications. Key parameters include working dimensions, mounting dimensions, and overall length.
Fastening Components: Check for loosened or damaged fasteners and replace them with identical parts as necessary.
Pressing and Ejecting Components: Inspect pressing parts like pressure plates and urethane, as well as ejecting components like stripper plates and pneumatic ejectors, for wear or damage. Repair damaged parts, check pneumatic ejection systems for leaks, and replace damaged air hoses as needed.
Monitoring Critical Mold Components: Focus on ejector and guide components, which ensure smooth mold opening, closing, and product ejection. Any damage can lead to production stoppage, so keep ejector pins and guide posts well-lubricated (using suitable lubricants) and check for deformation or surface wear. Replace worn parts immediately.
Rust Prevention and Lubrication After Each Production Cycle: Coat the mold’s working surfaces, moving parts, and guide components with specialized rust-prevention oil. Pay particular attention to gears, rack-bearing areas, and spring force in spring-loaded molds to ensure optimal functionality.
Cooling Channel Maintenance: Over time, cooling channels can accumulate scale, rust, sludge, and algae, reducing the channel size and the heat exchange efficiency. Regular cleaning of these channels is crucial to maintain productivity and control costs.
Heated and Controlled Systems in Hot Runner Molds: Proper maintenance of heating and control systems in hot runner molds is critical to prevent production issues. Regular upkeep is especially important to ensure stable operation.
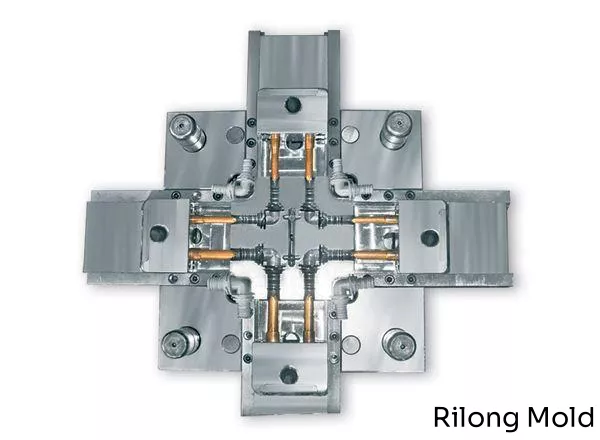
Causes of Wear and Tear
Material Issues with Key Working Parts of the Mold: Poor material selection results in inadequate performance and low wear resistance. Mold steel that has not been properly refined may contain numerous smelting defects. Insufficient forging process adjustments in the blanking process may leave heat treatment risks in both punch and die molds.
Structural Design Problems: Inadequate design of the stamping mold structure can cause issues. For instance, slender punches may lack reinforcement, leading to material buildup due to poor ejection flow. Excessive stripping force can increase the alternating load on the punches, intensifying wear.
Incomplete Mold-Making Process: Deficiencies in manufacturing, particularly in punch and die forging quality, can result in poor internal structure. Issues with heat treatment techniques and processes may lead to incomplete hardening, leaving soft spots and inconsistent hardness. Microcracks or even fractures may develop, and inadequate grinding or polishing may result in a high surface roughness.
Lack of Lubrication or Ineffective Lubrication: Either insufficient lubrication or ineffective lubrication can accelerate wear and tear on the mold.
Learn more about Rilong Mould Design and Manufacturing.