Through online meetings, we delve into the design schemes to accelerate the finalization process.
Since 2019, our company has gradually strengthened online video conference exchanges with international clients to update projects in real time, covering all stages of mold manufacturing and production status.
With the deepening of cost reviews and the shortening of delivery times, the significant effects of real-time communication in improving design and manufacturing processes have become increasingly apparent. One of the most successful cases is that we start from the client’s initial design concept, discuss in detail the functions that the product needs to achieve, until the completion of the design sketch, the verification of the 3D printed prototype, and finally enter the mold manufacturing and mass production stages.

We embarked on this project at the tail end of 2020 when a hookah vendor approached us with a request to produce plastic items featuring soft surfaces. We achieved this effect through the application of silicone oil spraying.
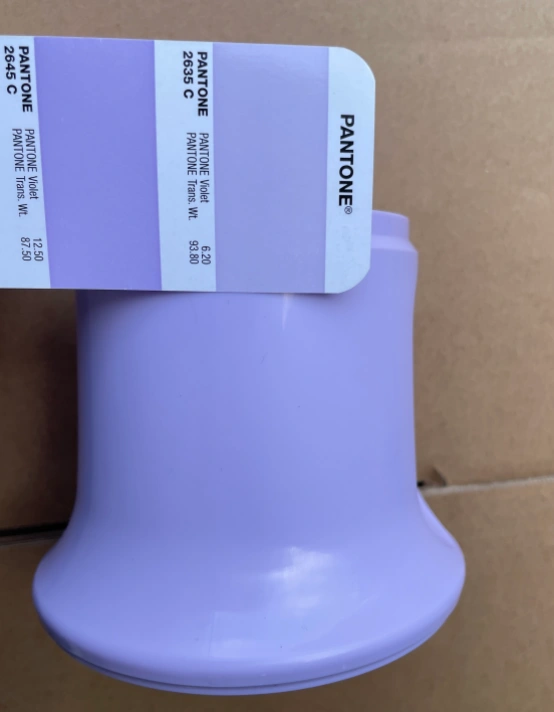
Subsequently, we dispatched several samples treated with silicone oil for the client’s approval. Upon receiving their design, we identified numerous aspects that were impractical for plastic injection molding. Issues included excessive thickness and metal components that were too cumbersome for over-molding.
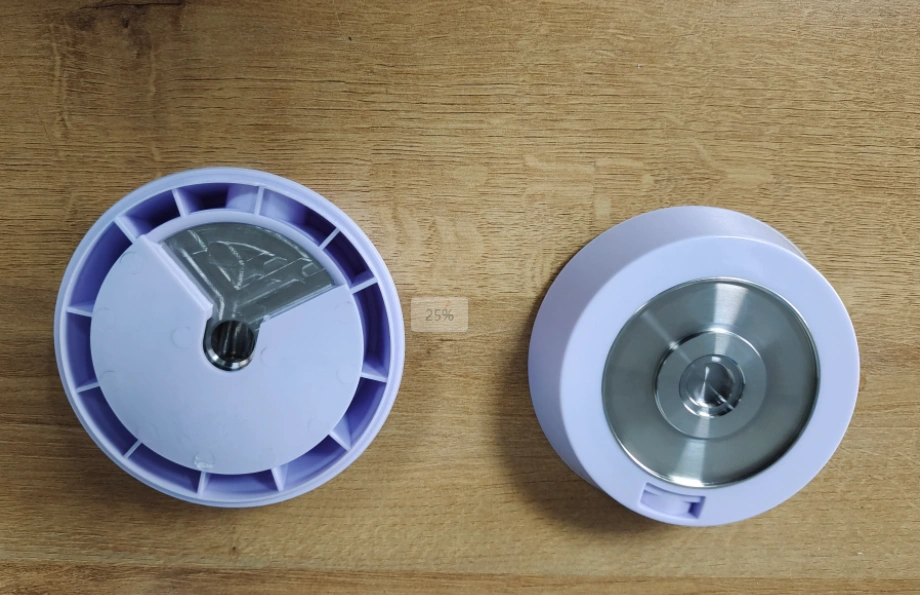
Initially, the client was reluctant to consider modifications, but recognizing the necessity to proceed with the project, we offered our assistance in refining the design. Our improvements were guided by their design philosophy, product assembly needs, and usage environment considerations.
Since 2020, we have repeatedly provided the client with CNC prototypes to test the product design and its effects. Ultimately, after 1 month, the client gave their design the green light, allowing us to commence the production of molds for the entire set.
The components in the below image constitute the foundational aspects of the product, featuring a plastic piece over-molded with a stainless steel element. The following red component serves as the body. Initially, we contemplated utilizing ultrasonic welding for the two parts to attain a waterproof seal. However, due to the excessive weight of the base, the main body and the base component sustained damage during transit. Consequently, we engaged in discussions with the customer through Teams conference to discuss all details, to modify the design, adopting a screw locking mechanism. Additionally, we incorporated a silicone gasket into the base to ensure waterproofing. The processes integral to this project encompass plastic over molding of metal parts, the over molding of soft plastic onto hard plastic, screw assembly, assembly of hardware and various accessories, surface treatment with primer and silicone oil, and LOGO silk screening.
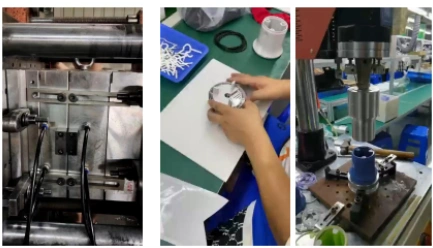
The product’s success was such that the customer expressed great satisfaction, ultimately opting to outsource the assembly and packaging production to our facility for further processing. This achievement was made possible by our web conferencing capabilities, the expertise of our design and engineering teams, the strategic efforts of our marketing team, the collaboration of our customers, and the professionalism of our manufacturing team.