Zinc alloys are alloys based on zinc and composed of other elements. Common alloying elements are aluminum, copper, magnesium, cadmium, lead, titanium and other low-temperature zinc alloys.
First, “the characteristics of zinc alloy
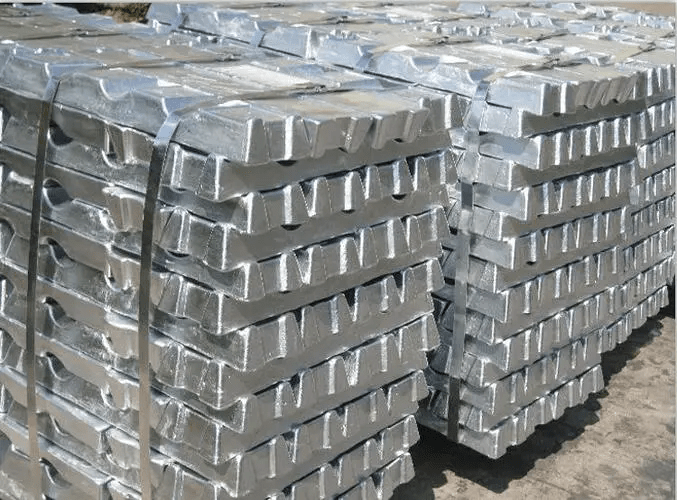
1. The ratio is significant;
2. Good casting performance, can die casting complex shape, thin wall precision parts, casting surface smooth;
3. Surface treatment: electroplating, spraying, painting, electrophoresis, polishing, water transfer, etc.
4. When melting and die casting, it does not absorb iron, does not corrode the mold, does not stick the mold;
5. Good mechanical properties and wear resistance at room temperature;
6. Low melting point, melting at 385℃, easy to die casting.
Second, the problems that need attention during the use of zinc alloy
1. Poor corrosion resistance. When the impurity elements of lead, cadmium and tin in the alloy composition exceed the standard, the casting is deformed due to aging, manifested as volume expansion, mechanical properties, especially plasticity, and even rupture for a long time. Lead, tin, cadmium in zinc alloy solubility is very small, so concentrated in the grain boundary and become the cathode, aluminum-rich solid solution becomes the anode, in the presence of water vapor (electrolyte) conditions, promote intergranular electrochemical corrosion. Die castings age due to intergranular corrosion.
2. Aging effect. The microstructure of zinc alloy is mainly composed of zinc rich solid solutions containing Al and Cu and Al rich solid solutions containing Zn, and their solubility decreases with the decrease of temperature. However, due to the extremely fast solidification rate of die casting, the solubility of the solid solution is greatly saturated at room temperature. After a certain period of time, this supersaturation phenomenon will gradually be lifted, and the shape and size of the casting will change slightly.
3. Zinc alloy die casting parts should not be used in high temperature and low temperature (below 0℃) working environment. Zinc alloy has good mechanical properties at room temperature. However, the tensile strength and impact performance at low temperature both decrease significantly.
Third, the type of zinc alloy
Zamak 3: Good fluidity and mechanical properties. It is applied to castings with low mechanical strength, such as toys, lamps, decorations, and some electrical parts.
Zamak 5: Good fluidity and good mechanical properties. It is used in castings with certain requirements for mechanical strength, such as auto parts, electromechanical parts, mechanical parts, electrical components.
Zamak 2: Used for mechanical parts with special requirements for mechanical properties, high hardness requirements and general dimensional accuracy requirements.
ZA8: Good fluidity and dimensional stability, but poor fluidity. It is used for die-casting workpiece with small size, high precision and mechanical strength, such as electrical parts.
Superloy: Best fluidity, applied to die casting thin-wall, large size, high precision, complex shape of the workpiece, such as electrical components and their shells.
Different zinc alloys have different physical and mechanical properties, which provides room for choice in die casting design.
Fourth, the choice of zinc alloy
The choice of which zinc alloy is mainly considered from three aspects
1. The use of the die casting itself needs to meet the performance requirements
(1) Mechanical properties, tensile strength, is the maximum resistance when the material breaks; Elongation is a measure of brittleness and plasticity of materials. Hardness is the resistance of the surface of the material to the plastic deformation caused by the pressing or friction of hard objects.
(2) Working environment state: working temperature, humidity, workpiece contact medium and air tightness requirements.
(3) Accuracy requirements: the accuracy and dimensional stability that can be achieved.
2. Good process performance
(1) Casting process (2) machining process (3) surface treatment process
3. Good economy
The cost of raw materials and requirements for production equipment (including melting equipment, die casting machines, molds, etc.), as well as production costs. Zinc alloy composition control the effect of each element in the alloy composition, the effective alloy elements: aluminum, copper, magnesium; Harmful impurity elements: lead, cadmium, tin, iron.
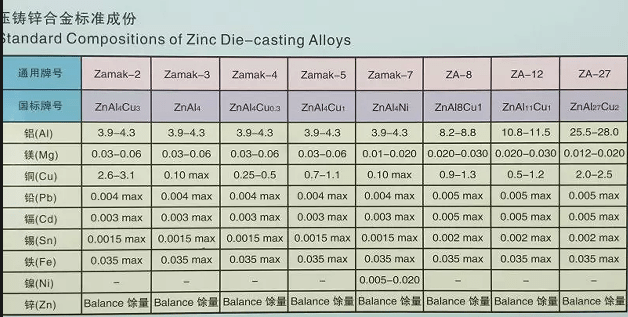
(1) Aluminum action
A. Improve the casting performance of the alloy, increase the fluidity of the alloy, refine the grain, cause solid solution strengthening, improve the mechanical properties.
B. Reduce the reaction ability of zinc to iron and reduce the erosion of iron materials, such as gooseneck, mold and crucible. The aluminum content is controlled at 3.8 ~ 4.3%. The main consideration is the required strength and flow, and good flow is the necessary condition for obtaining a complete, accurate size and smooth surface casting.
(2) Copper action
A. Increase the hardness and strength of the alloy;
B. Improve the wear resistance of the alloy;
C. Reduce intergranular corrosion.
D. When the copper content exceeds 1.25%, the size and mechanical strength of the die-casting parts will change due to failure; Reduces the extensibility of the alloy.
(3) Magnesium action
A. Reduce intergranular corrosion
B. Refine the alloy structure to increase the strength of the alloy
C. Improve the wear resistance of the alloy
D. Disadvantage: when the magnesium content is > 0.08%, it will produce hot brittleness, toughness and fluidity; Easy oxidation loss in the molten state of the alloy.
(4) impurity elements
Lead, cadmium and tin make the intergranular corrosion of zinc alloy become very sensitive, accelerate the intergranular corrosion in the warm and wet environment, reduce the mechanical properties, and cause the casting size change. When the impurity elements in zinc alloy lead, cadmium content is too high, the workpiece just die casting molding, the surface quality is normal, but after storage at room temperature for a period of time (eight weeks to several months), the surface bubbling.
(5) Impurity element iron
A. Iron reacts with aluminum to form Al5Fe2 intermetallic compounds, resulting in the loss of aluminum and the formation of scum.
B. Hard points are formed in die casting parts, affecting post-processing and polishing.
C. Increase the brittleness of the alloy. The solubility of iron in the zinc solution increases with the increase of temperature, and every change in the temperature of the zinc solution in the furnace will cause the iron element to be supersaturated (when the temperature drops) or unsaturated (when the temperature rises). When the iron element is supersaturated, the supersaturated iron will react with the aluminum of the alloy, resulting in an increase in the amount of scum. When the iron element is unsaturated, the corrosion of the alloy on the zinc pan and gooseneck material will be enhanced to return to the saturated state. A common result of the two temperature changes is the eventual consumption of aluminum and the formation of more scum.
Fifth. Problems that need attention in the production of zinc alloy
1. Control alloy composition From the purchase of alloy ingot, alloy ingot must be based on ultra-high purity zinc, plus ultra-high purity aluminum, magnesium, copper alloy ingot, the supplier has strict composition standards. High quality zinc alloy material is the guarantee of producing high quality castings.
2. The purchased alloy ingots should be guaranteed to have a clean and dry stacking area to avoid white rust caused by long-term exposure to humidity, or be polluted by factory dirt and increase the production of slag, and also increase the metal loss. A clean factory environment is very helpful for the effective control of alloy composition.
3. The ratio of new material and water inlet return charge, return charge should not exceed 50%, general new material: old material = 70:30. Continuous refusion of aluminum and magnesium gradually reduced.
4. When remelting the nozzle material, it is necessary to strictly control the remelting temperature not to exceed 430 ° C to avoid the loss of aluminum and magnesium.
5. Conditional die-casting plant is best to use a centralized furnace to melt zinc alloy, so that alloy ingot and return charge uniform ratio, flux can be more effective use, so that alloy composition and temperature remain uniform and stable. Electroplating waste and fine chips should be melted separately.
Sixth, the treatment of common defects of zinc alloy die casting parts
Since the cause of each defect comes from a number of different influencing factors, so in the actual production to solve the problem, in the face of many reasons in the end is the first adjustment machine? Or refueling first? Or modify the mold first? It is suggested to deal with it according to the degree of difficulty, first simple and then complex, in the order:
1. Clean the parting surface, clean the cavity and clean the ejector rod; Improve the coating, improve the spraying process; Increase the clamping force and increase the amount of cast metal. These are simple measures that can be implemented.
2. Adjust the process parameters, injection force, injection speed, filling time, mold opening time, pouring temperature, mold temperature, etc.
3. Refuelling, select high-quality aluminum alloy ingot, change the proportion of new material and return charge, and improve the smelting process.
4. Modify the mold, modify the pouring system, add the inner gate, add the overflow groove, exhaust groove, etc.
For example, the causes of flash in die casting are:
1) Die casting machine problem: the clamping force is not adjusted correctly.
2) Process problems: the injection speed is too high, resulting in high pressure impact peak.
3) Mold problems: deformation, debris on the parting surface, inserts and sliders are not worn evenly, and the strength of the template is not enough.
The sequence of measures to solve the flash: cleaning the parting surface → improving the clamping force → adjusting the process parameters → repairing the wear parts of the mold → improving the stiffness of the mold. From easy to difficult, each step of improvement, first test its effect, and then carry out the second step.
Seventh. Smelting of zinc alloys
Alloy melting is an important part of the die casting process, the melting process is not only to obtain molten metal, more importantly, the chemical composition is in line with the requirements, can make the die casting to get a good crystal structure and gas, inclusions are very small metal liquid. In the melting process, the interaction between metal and gas and the interaction between metal and the crucible causes the composition to change, resulting in inclusions and inspirations. Therefore, formulating the correct melting process procedures and strictly implementing them is an important guarantee for obtaining high-quality castings.
1. Interaction between metal and gas In the smelting process, the gases encountered are hydrogen (H2), oxygen (O2), water vapor (H2O), nitrogen (N2), CO2, CO, etc., which are either dissolved in liquid metal, or chemically react with it.
2. Gas source Gas can enter the alloy liquid from the furnace gas, furnace lining, raw materials, flux, tools and other ways.
3. Interaction between metal and crucible When the melting temperature is too high, the reaction between iron crucible and zinc liquid is accelerated, and iron oxidation reaction occurs on the surface of the crucible to produce oxides such as Fe2O3; In addition, the iron element also reacts with the zinc solution to form the FeZn13 compound (zinc slag), which is dissolved in the zinc solution. The wall thickness of the iron crucible is continuously reduced until it is scrapped.
Eighth, zinc alloy melting temperature control
1. Die casting temperature
The melting point of zinc alloy used in die casting is 382 ~ 386℃, and the appropriate temperature control is an important factor in the composition control of zinc alloy. In order to ensure the good fluidity of the alloy liquid filling cavity, the metal liquid temperature in the zinc pan of the die-casting machine is 415 ~ 430 ° C, and the die-casting temperature of thin-walled parts and complex parts can be upper limit. Thick wall parts, simple parts can be lower limit. The temperature of molten metal in the central melting furnace is 430 ~ 450℃. The temperature of the liquid metal entering the gooseneck tube is basically the same as the temperature inside the zinc pan.
The casting temperature can be accurately controlled by controlling the metal liquid temperature of zinc pot. And do: ① the metal liquid is a clean liquid without oxide; ② Pouring temperature does not fluctuate.
The harm of excessive temperature: ① aluminum and magnesium are burned. ② The metal oxidation rate is accelerated, the burning loss is increased, and the zinc slag is increased. ③ The phenomenon of stuck hammer head will occur during thermal expansion. ④ More iron is fused into the alloy in the cast iron crucible, and the reaction between zinc and iron is accelerated at high temperature. Hard particles of iron-aluminum intermetallic compounds will be formed, causing excessive wear of the hammer head and gooseneck. ⑤ Fuel consumption increases accordingly.
The temperature is too low: the alloy fluidity is poor, which is not conducive to forming and affects the surface quality of die casting parts.
The current die casting machine melting pot or furnace are equipped with temperature measurement and control system, the daily work is mainly to check regularly to ensure the accuracy of the temperature measuring instrument, and regularly measure the actual temperature of the furnace with a portable thermometer (thermometer) to be corrected. Experienced die casters use the naked eye to observe the molten liquid, if the slag scraping feel that the molten liquid is not too viscous, but also clearer, slag is not fast, indicating that the temperature is appropriate; If the liquid is too viscous, the temperature is low; After scraping, a layer of white frost appears quickly on the liquid surface, and the slagging is too fast, indicating that the temperature is high and should be adjusted in time.
2. How to keep the temperature stable
One of the best methods: using a central melting furnace, die-casting machine furnace as a heat preservation furnace, so as to avoid the zinc pot directly added zinc ingots melting caused by large temperature changes. Centralized melting can ensure the stability of alloy composition.
The second best method: The use of advanced liquid metal automatic feeding system, can maintain a stable feeding speed, alloy liquid temperature and zinc pan liquid level.
If the current production conditions are direct feeding in the zinc pot, it is recommended to add the whole alloy ingot at one time instead of adding small pieces of alloy ingot several times, which can reduce the temperature change amplitude caused by feeding.
Nineth. Production and control of zinc slag
By melting the alloy from solid to liquid, this is a complex physical and chemical process. The gas reacts with the molten metal, of which the oxygen reaction is the most intense, and the alloy surface is oxidized to produce a certain amount of scum. The scum contains oxides and intermetallic compounds of iron, zinc, and aluminum, and the scum scraped from the melt surface usually contains about 90% zinc alloy. The reaction rate of zinc slag formation increases exponentially with the increase of melting temperature. Under normal circumstances, the output of the original zinc alloy ingot is less than 1%, in the range of 0.3 ~ 0.5%; The amount of slag produced by remelting water outlet and waste workpiece is usually between 2 and 5%.
1. Zinc slag quantity control
① Strictly control the melting temperature, the higher the temperature, the more zinc slag.
② As far as possible to avoid the stirring of alloy liquid in the zinc pot, any way of agitation will lead to more alloy liquid and oxygen atoms in the air contact, resulting in the formation of more scum.
Do not scavenge too often. When the molten alloy is exposed to air, it will oxidize, forming scum, and keeping a thin layer of scum on the furnace surface will help the liquid in the pot not to further oxidize.
④ When slagging, use a porous (with a diameter of 6 mm) dish-shaped slagging rake, gently scrape under the scum, avoid stirring the alloy liquid as much as possible, lift the scraped slag, slagging rake gently knock on the edge of the zinc pan, so that the metal liquid flows back into the zinc pan.
2. Treatment of zinc slag
Sell back to the raw material supplier or specialized treatment plant, as it may be more expensive to process it yourself.
② Die casting factory processing. A separate furnace is required, and the zinc slag remelting temperature is in the range of 420 ~ 440 ° C. Add the flux at the same time. Melting 100 kilograms of slag, need to add 0.5 to 1.5 kilograms of flux, first evenly distributed in the metal liquid surface, and then use the blender to evenly mix it into the molten metal (about 2 to 4 minutes), after 5 minutes of heat preservation, the surface produces a layer more like dirt, scrape it off.
3. Nozzle material, waste remelting nozzle material, waste material, garbage, scrap workpiece, etc., should not be directly put into the zinc pot of die casting machine for remelting. The reason is that the surface of these mouthpieces oxidizes during the die casting process, and the content of zinc oxide far exceeds the original alloy ingot. When these mouthpieces are remelted in the zinc pan, due to the viscous state of zinc oxide under high temperature conditions, a large number of alloy components will be taken away when they are removed from the zinc pan.
4. Electroplating waste remelting
Electroplating waste should be melted separately from non-electroplating waste, because electroplating waste containing copper, nickel, chromium and other metals are insoluble in zinc, remaining in the zinc alloy will exist as hard particles, bringing polishing and machining difficulties.
Tenth. Precautions in smelting operation
1. Crucible: It must be cleaned before use to remove oil, rust, slag and oxide on the surface. In order to prevent the iron element in the cast iron crucible from being dissolved in the alloy, the crucible should be preheated to 150 ~ 200 ° C, spray a layer of paint on the working surface, and then heated to 200 ~ 300 ° C to completely remove the water in the paint.
2. Tools: The surface dirt should be removed before use, and the parts in contact with the metal must be preheated and painted. The tool should not be stained with water, otherwise it will cause liquid splashing and explosion.
3. Alloy material: Clean and preheat before melting to remove moisture adsorbed on the surface. In order to control the alloy composition, it is recommended to use 2/3 of the new material and 1/3 of the return charge.
4. The melting temperature must not exceed 450℃.
5. Timely clean up the scum on the liquid surface of the zinc pan, timely add zinc material, and maintain the normal height of the molten liquid level (not less than 30 mm of the crucible surface), because too much scum and too low liquid level are easy to cause slag into the gooseneck cylinder, pull the steel, the hammer and the cylinder itself, resulting in the stuck hammer, gooseneck and the hammer scrap.
6. The scum above the molten liquid is stirred calmly with a slag rake to gather it for removal.
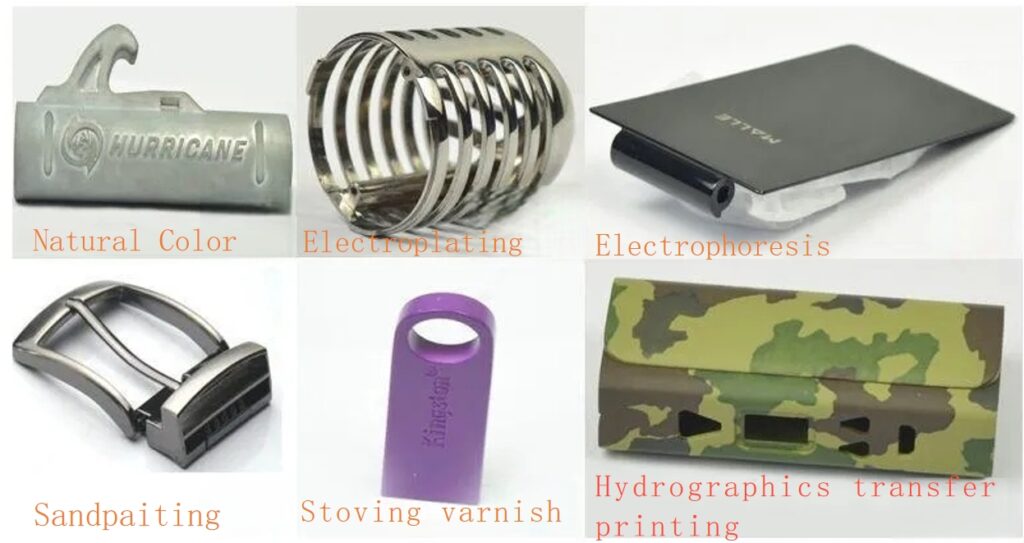