In the world of precision manufacturing, mold-making is a cornerstone that supports numerous industries, including automotive, electronics, medical devices, and consumer goods. As products become more complex, so do the molds that are required to create them. One of the most innovative advancements in this space is the high-precision mold with a multi-slide structure. This technology allows for the production of highly detailed and intricate parts, offering unparalleled accuracy, efficiency, and versatility.
In this blog, we will delve into the significance of multi-slide mold technology, its benefits, and its growing importance in today’s precision-driven industries.
What is a Multi-Slide Mold Structure?
Traditional molds usually consist of two halves – a core and a cavity. These are sufficient for simple part geometries, but they fall short when it comes to creating complex shapes with undercuts or parts that require high dimensional accuracy. This is where the multi-slide mold (or multi-cavity mold) comes into play.
A multi-slide mold, also known as a multi-action or multi-directional mold, incorporates multiple sliding sections (or “slides”) that move in different directions to create more complex geometries. Instead of only two mold halves closing in a linear direction, multi-slide molds use additional moving components to form intricate shapes that would otherwise be impossible or cost-prohibitive to manufacture.
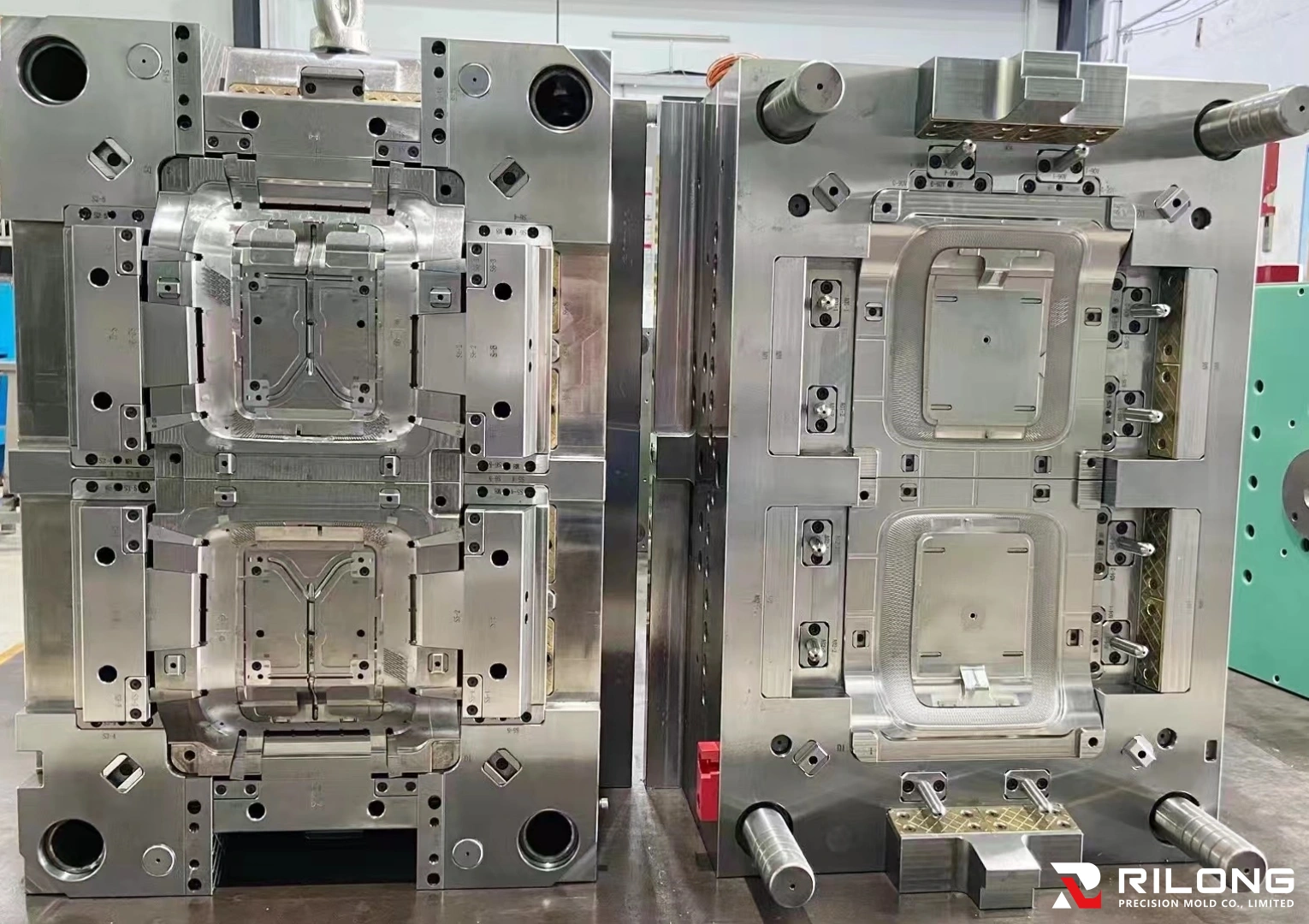
These sliding sections are generally driven by hydraulic or mechanical systems, and they move in synchrony during the molding process, allowing for multiple parts features to be formed in one shot.
Key Features of High-Precision Molds with Multi-Slide Structure
1. Complex Geometry Capability
Multi-slide molds excel in creating intricate and complex parts with multiple undercuts, threads, and other challenging features that are difficult or impossible to achieve using conventional two-part molds. The additional slide movements allow for precision molding of parts that require fine detail and close tolerances.
2. Precision and Accuracy
One of the most important aspects of a high-precision mold is its ability to maintain extremely tight tolerances. Multi-slide technology enables mold makers to achieve higher precision in dimensions, which is critical in industries such as automotive and medical, where even the smallest deviations can lead to failure or suboptimal performance.
3. Reduced Assembly and Post-Processing
By using a multi-slide mold, manufacturers can often reduce or even eliminate the need for secondary operations such as machining, assembly, or post-processing. Because the mold can produce more complex parts in one shot, the entire manufacturing process becomes more streamlined, reducing labor costs and production times.
4. Increased Efficiency
While traditional molds require complex tooling changes or multiple manufacturing stages to achieve similar results, multi-slide molds consolidate multiple steps into a single cycle. This significantly increases the production efficiency and lowers the cycle time. This is particularly valuable in high-volume production scenarios where efficiency translates directly to cost savings.
5. Longer Tool Life
High-precision molds with a multi-slide structure are engineered to last longer. The ability to create complex parts in one step, along with the use of advanced materials and coatings for the mold components, results in reduced wear and tear, leading to an extended lifespan for the mold.
The key components of a multi-slide mold include:
- Guide Pins: Ensure precise alignment and movement of the slides.
- Slide Bodies: Provide structural support and house the sliding mechanisms.
- Wear Plates: Reduce friction and wear between moving parts.
- Press Blocks: Exert pressure to facilitate smooth sliding action.
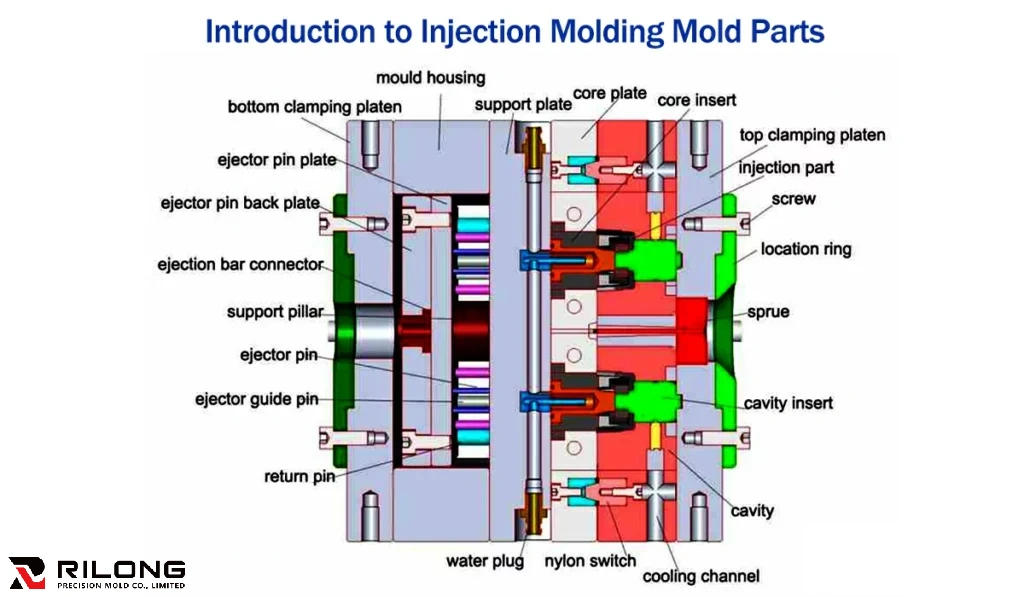
The Role of Automation and Digitalization
As with many areas of manufacturing, the integration of automation and digital technologies has enhanced the capabilities of high-precision molds with multi-slide structures. Computer-Aided Design (CAD) and Computer-Aided Manufacturing (CAM) technologies have streamlined the design and production process, allowing for faster prototyping and iteration. Moreover, automation systems can now control the slide movements with incredible accuracy, ensuring repeatable and consistent part quality.
Additionally, Industry 4.0 advancements such as smart molds equipped with sensors are now becoming more common. These molds can monitor the molding process in real-time, ensuring optimal conditions and reducing downtime due to maintenance.
What materials are commonly used for multi-slide molds?
Multi-slide molds are typically made from materials that offer high durability, wear resistance, and the ability to withstand the pressures and temperatures involved in the molding process. Here are some commonly used materials:
Hardened Steel: Similar to tool steel, hardened steel provides excellent wear resistance and durability. It’s commonly used for high-volume production molds where longevity is crucial.
Tool Steel: Known for its hardness and resistance to wear, tool steel is a popular choice for multi-slide molds. It can endure the high pressures and temperatures of the molding process, ensuring longevity and precision.
Aluminum: While not as hard as tool steel, aluminum is lightweight and offers good thermal conductivity. It’s often used for prototype molds or low-volume production runs where quick heat dissipation is beneficial.
Beryllium Copper: This material is valued for its excellent thermal conductivity and strength. Beryllium copper is often used in areas of the mold that require rapid cooling or are subject to high wear.
These materials are selected based on the specific requirements of the molding process, including the type of plastic being molded, the complexity of the part, and the expected production volume.
Key Design Considerations for High-Precision Multi-Slide Molds
- Slide Design: The design of the slides must be precise and robust to ensure accurate movement and prevent wear and tear.
- Slide Guidance: Proper guidance mechanisms are essential to maintain slide alignment and prevent binding or jamming.
- Material Selection: The materials used for the mold components must be high-quality and capable of withstanding the rigors of the manufacturing process.
- Mold Base: The mold base should be designed to accommodate the multiple slides and provide a stable foundation for the mold.
- Ejection System: A reliable ejection system is crucial for preventing part damage and ensuring efficient part removal.
Applications of Multi-Slide Mold Technology
Due to its ability to create parts with intricate details and tight tolerances, multi-slide mold technology has found applications across a wide range of industries:
- Automotive: From engine components to interior elements, multi-slide molds allow for the mass production of complex and durable parts.
- Consumer Electronics: Tiny, highly detailed parts in devices like smartphones and wearables often rely on the precision capabilities of multi-slide molding.
- Medical Devices: Parts used in medical devices, such as connectors or implantable components, require extreme accuracy and the ability to produce complex shapes without compromising material integrity.
- Aerospace: High-precision parts used in aircraft and space technologies, where safety and reliability are paramount, benefit greatly from multi-slide molding technology.
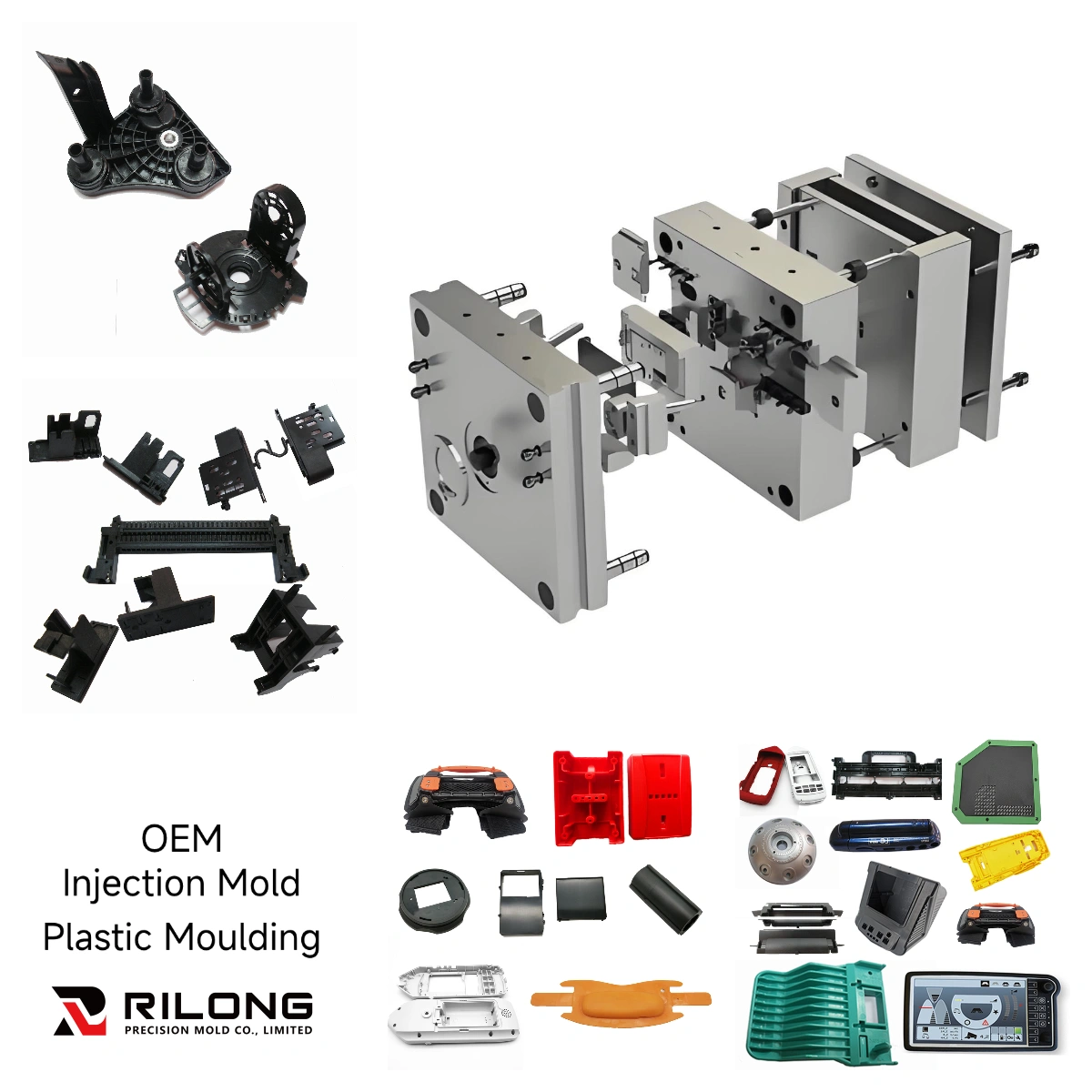
Challenges and Considerations
Despite its many advantages, implementing multi-slide molds in manufacturing presents some challenges. The design and construction of these molds require advanced expertise and engineering precision. The initial cost of developing a multi-slide mold is typically higher than that of a traditional mold, though the long-term benefits in terms of production efficiency and reduced secondary processing often outweigh the upfront investment.
It’s also crucial to consider that the mold-making process must align with the part’s design and functionality. This demands close collaboration between mold makers, designers, and engineers to ensure that the multi-slide system is optimized for both performance and manufacturability.
Conclusion
As industries continue to demand more complex and high-precision parts, multi-slide mold technology offers a robust solution that combines precision, efficiency, and versatility. High-precision molds with multi-slide structures represent the future of injection molding, helping manufacturers meet the ever-increasing demands for quality and complexity while driving down costs.
For businesses looking to stay ahead in competitive industries such as automotive, aerospace, and medical, adopting this technology can be a game-changer. By investing in high-precision multi-slide molds, companies not only improve their production processes but also ensure the delivery of top-quality, intricate products to their customers.