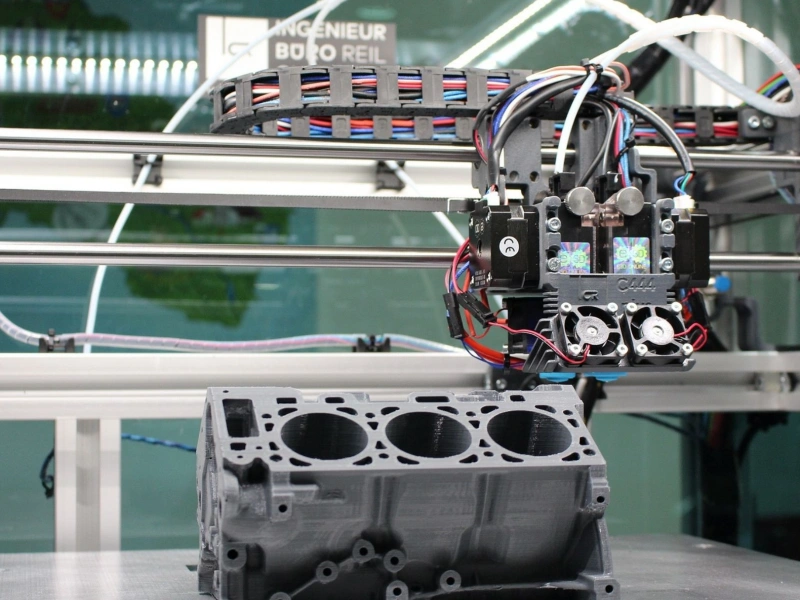
Injection Molding and 3D Printing, Which is Right for Your Project? consider these key factors.
Part Quantity
The quantity of parts required is a key factor in determining the process. Injection molding is renowned for its effectiveness in large production runs (1,000+ parts per run). For small batches (under 10), 3D printing is more suitable and cost-effective. For simple 3D printing processes like FDM or SLS and affordable plastics such as ABS, PC, or nylon, 3D printing is undoubtedly the better choice for single parts or low volumes (similar or varied parts). MJF is a popular and viable option for medium quantities, ranging from 10 to 1,000 parts.
Recommendation: For high-volume production, injection molding is a perfect choice, while 3D printing is suitable for small-batch production.
Design Complexity
Injection molding requires creating a mold based on the desired part design (as opposed to the part itself). Designing a CAD model for injection molding is complex due to the numerous critical factors involved. For instance, sharp angles in the design can hinder smooth part removal from the mold, while delicate features require careful attention to avoid potential damage. However, 3D printing excels at handling complex designs. No matter how complex the design, 3D printing can make it possible with minimal effort.
Recommendation: Check if your design is feasible for injection molding. If not, adjust the design or consider using 3D printing.
Turnaround Time
Injection molding requires a longer turnaround time because it involves design analysis and creating the perfect mold based on the design (10-20 days). Compared to injection molding, the turnaround time for 3D printing is very short. At Rilong, you can receive high-quality 3D-printed parts in as little as 2 days.
Recommendation: If you need the part immediately, opt for 3D printing.
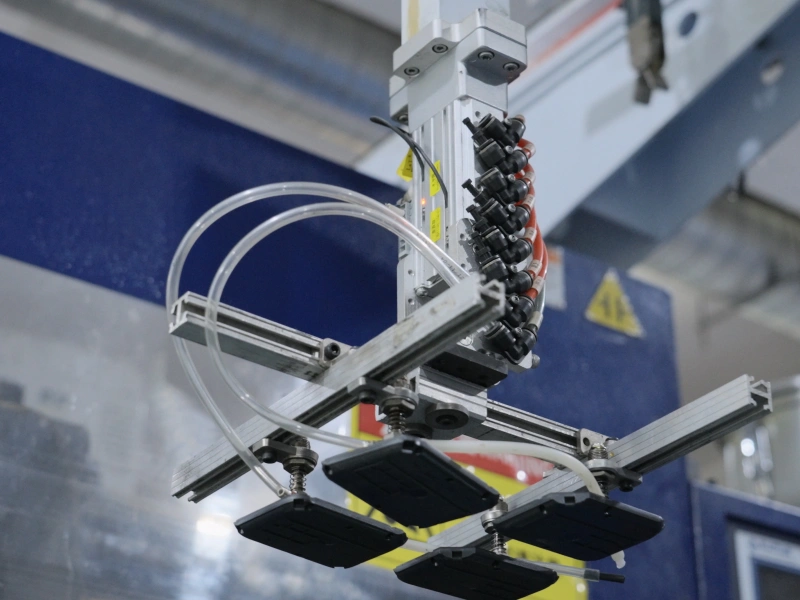
Customization
Creating a mold for injection molding requires considerable time and expense to redesign when modifications are necessary. Injection molding is generally unsuitable for custom parts or changes to an existing design due to the high costs and time involved in retooling. Whatever comes out of the mold is the final part, and modifying it is highly complex. In contrast, 3D printing provides exceptional flexibility for customization; updating the design is as simple as modifying the CAD file. This makes it ideal for prototyping and testing parts.
Recommendation: 3D printing is recommended for prototyping and customization.
Material Strength
Parts made through injection molding consist of a single cast layer, which increases the strength of the shape because there are no cracks or weak points. However, 3D printing builds parts layer by layer, which can impact their overall strength. 3D printing can result in visible ridges and structural defects during the manufacturing process, which are typically absent in plastic injection molding.
Recommendation: If material strength is a priority, choose injection molding.
Surface Finish
Although the layers in 3D printing are thin and closely spaced, they remain noticeable. Regardless of the level of layer detail, this creates a ridged surface on the finished object. This becomes an issue if you intend to produce objects that will come into contact with or rub against other parts, such as moving machinery components. In such cases, smooth post-processing is needed, which is an additional step.
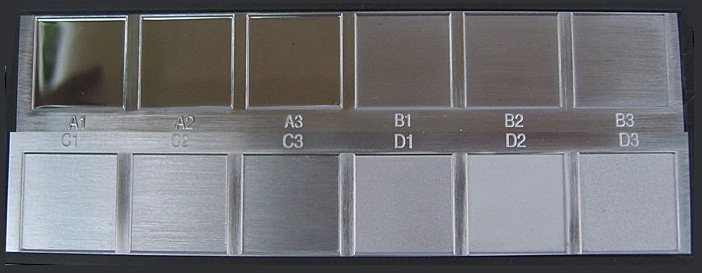
In comparison, injection molding creates a consistently smooth, uniform surface finish by casting the material in a single layer, which removes issues with parting lines or mold layers. Additionally, injection-molded parts allow for efficient post-processing to achieve the desired final appearance and quality.
Recommendation: From the perspective of achieving a good surface finish, injection molding is the preferred choice.
Material Waste: Since injection molding allows the material to fill the mold as completely as possible, it uses precisely the amount of material required for each design, making it a highly efficient method for mass production without waste concerns. On the other hand, some 3D printing technologies lose material when constructing support structures. While material powder can be reused, it can only be reused a limited number of times before its performance degrades.
Recommendation: 3D printing generates minimal waste, such as support structures, and failed prints must be removed in post-production. However, when producing single units or small batches, waste is less significant, whereas in large batches, waste becomes more substantial. Therefore, if your production volume is large, consider using injection molding to avoid material waste concerns.
Choose 3D printing | Choose injection molding |
Small batch printing | Large batch production |
Complex part design | Material strength priority |
Parts needed for immediate printing | High-quality surface finish |
Prototyping and customization | No material waste |
In the manufacturing world, there is a common misconception that 3D printing can replace injection molding and is a standalone winner in every aspect. However, both technologies have their strengths and weaknesses. Rilong Precision Mold offers both injection molding and 3D printing services, with a dedicated team ready to support you. Upload your design now to receive a quote for your project.