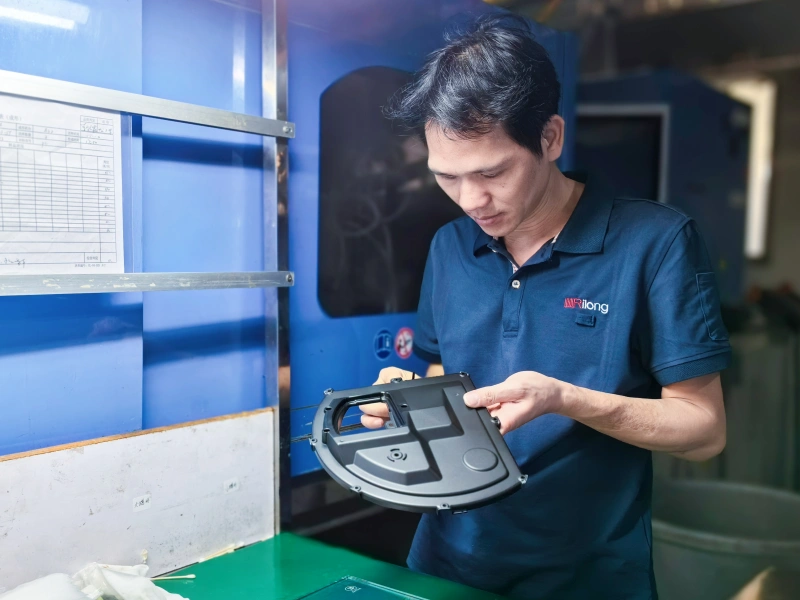
Working Principle and Operation of Plastic Injection Molding Machines
The plastic injection molding machine utilizes the thrust of a screw (or plunger) to inject molten (viscous flow state) plastic into a closed mold cavity. After solidification and shaping, the finished product is obtained. Injection molding is a cyclical process, with each cycle primarily including the following steps: quantitative feeding, melting and plasticizing, pressure injection, mold filling and cooling, mold opening, and part removal. Once the part is removed, the mold closes again to start the next cycle.
Plastic Injection Molding Process Steps:
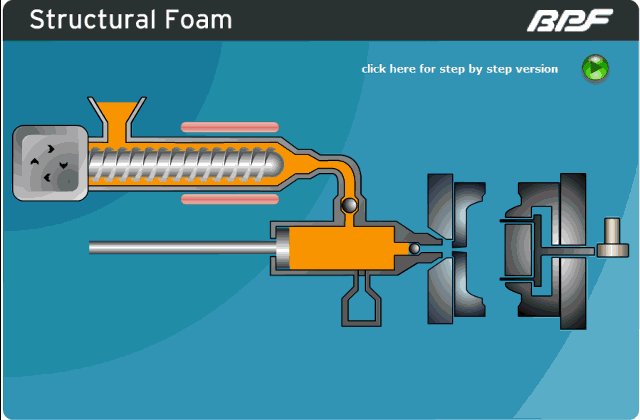
- Mold Clamping
The movable mold plate quickly approaches the fixed mold plate. Once confirmed that no foreign objects are present, the system applies high pressure to lock the mold. - Injection Unit Advancing
The injection unit advances to the designated position. - Plastic Injection
The system controls the screw with multiple adjustable settings for speed, pressure, and stroke to inject melted plastic from the barrel into the mold cavity. - Cooling and Holding Pressure
Pressure is maintained on the barrel at preset levels and time intervals while the mold cavity cools and shapes the product. - Cooling and Plasticizing
The product continues to cool inside the mold cavity, while a hydraulic motor drives the screw to rotate, pushing plastic pellets forward. The screw retracts under controlled back pressure. Once it reaches the preset position, the screw stops rotating. The injection cylinder retracts slightly, completing the plasticizing process. - Injection Unit Retracting
After plasticizing, the injection unit retracts to its designated position. - Mold Opening
The mold plates open, returning to their original position. - Ejection
Ejector pins push the finished product out of the mold.
PC Plastic Characteristics
PC plastic offers high mechanical strength, a wide operating temperature range, excellent electrical insulation properties, dimensional stability, and transparency.
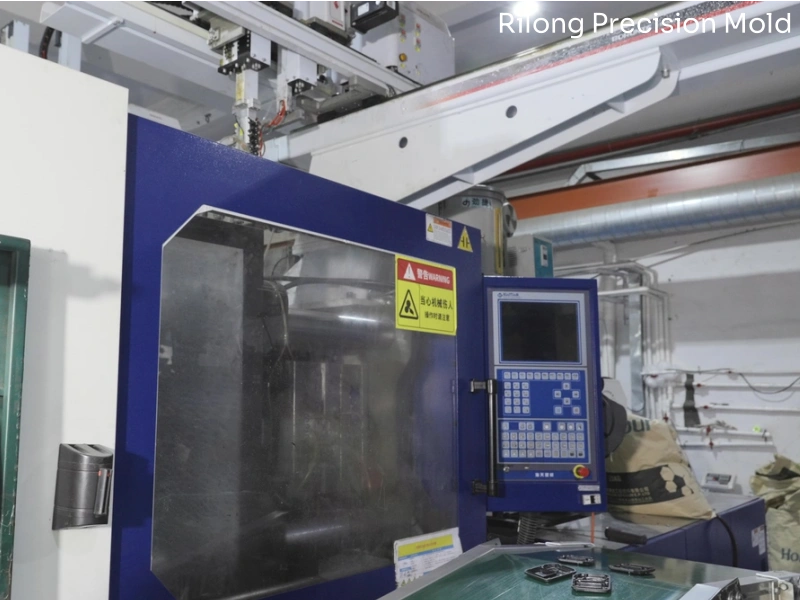
- Material Handling
- PC absorbs moisture at a high rate, so you must preheat and dry it before processing.
- Pure PC: Dry at 120°C.
- Modified PC: Typically dried at 110°C for over 4 hours, but not exceeding 10 hours.
- Adequate drying can be checked using an air-extrusion test.
- Recycled material usage can reach 20%, and in some cases, up to 100%, depending on product quality requirements.
- When using recycled material, avoid mixing different masterbatches, as this can severely compromise product properties.
- PC absorbs moisture at a high rate, so you must preheat and dry it before processing.
- Selection of Injection Molding Machine
- Cost and other considerations commonly lead manufacturers to use modified PC materials, such as Chimei 757. Electrical products require flame retardancy.
- For flame-retardant PC or plastic alloy products, the injection molding machine’s plasticizing system must ensure excellent mixing and resistance to corrosion.
- Standard screws may not suffice, so communicate the specifications before purchasing equipment.
- Mold and Gate Design
- Typical mold temperature:
- Standard: 80-100°C.
- Glass-fiber reinforced: 100-130°C.
- Use needle gates for small products, ensuring a depth of around 70% of the thickest section. Other gate types include ring or rectangular gates.
- Larger gates reduce excessive shearing and associated defects.
- Vent depth: Less than 0.03-0.06 mm.
- Runners should be as short and round as possible.
- Draft angle: Typically around 30′-1°.
- Typical mold temperature:
- Melt Temperature
- The melt temperature can be determined using the air-injection method.
- Typical processing temperatures:
- Standard PC: 270-320°C.
- Modified or low molecular weight PC: 230-270°C.
- Injection Unit Retracting
- Higher injection speeds are commonly used, especially for items like electrical switches.
- Typical sequence: Slow to fast injection speed.
- Back Pressure
- Typical back pressure is around 10 bar, but you can lower it if there are no gas streaks or color issues.
- Residence Time
- Prolonged residence time at high temperatures can degrade the material, causing CO₂ release and yellowing.
- Avoid using LDPE, POM, ABS, or PA for barrel cleaning; instead, use PS.
- Special Considerations
- Modified PC with excessive recycling or uneven mixing of components can result in dark brown liquid bubbles.
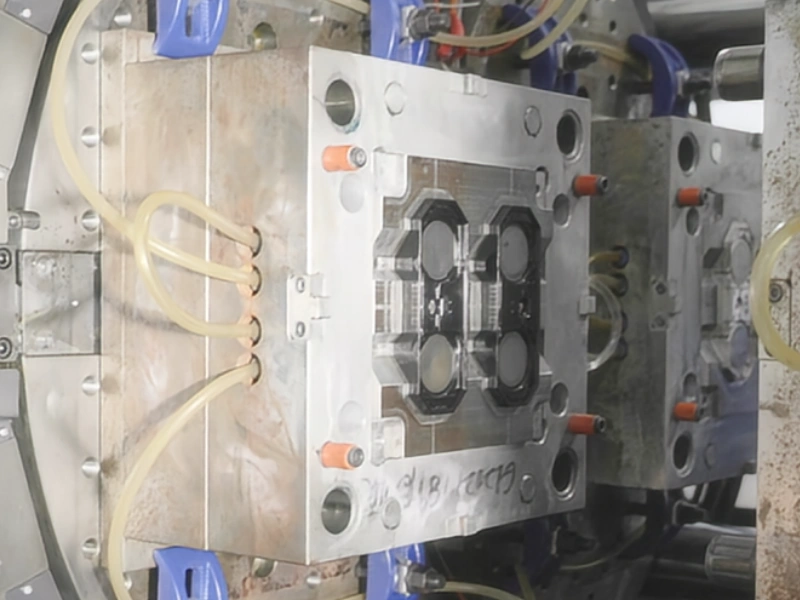
Advantages
Injection molding offers several advantages, including fast production speed, high efficiency, the potential for automation, and a wide variety of designs. It allows for complex shapes, precise dimensions, and products ranging from small to large sizes. Additionally, it facilitates rapid product updates and the production of intricate components. This method is especially suitable for mass production and manufacturing complex-shaped items.
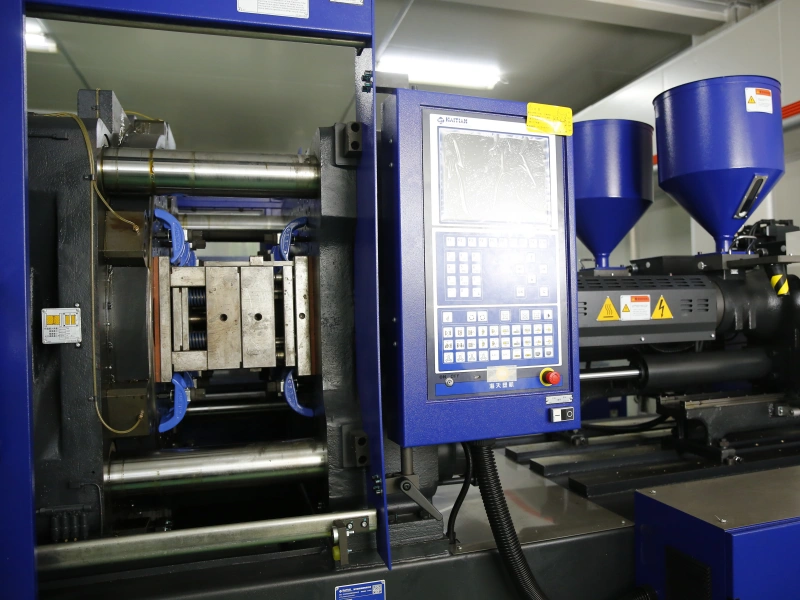
By adhering to these guidelines, the quality of PC plastic products can be ensured while minimizing potential issues in production.
Learn more about Rilong Plastic Injection Molding.