In a recent project, we faced a challenging task: producing a plastic electronic control box for an appliance. During production, we encountered an injection molding defect that required multiple stages of adjustment to resolve. While the process was complex, it proved to be an intriguing journey in optimizing our manufacturing technique.
First, let’s discuss the characteristics of this plastic part:
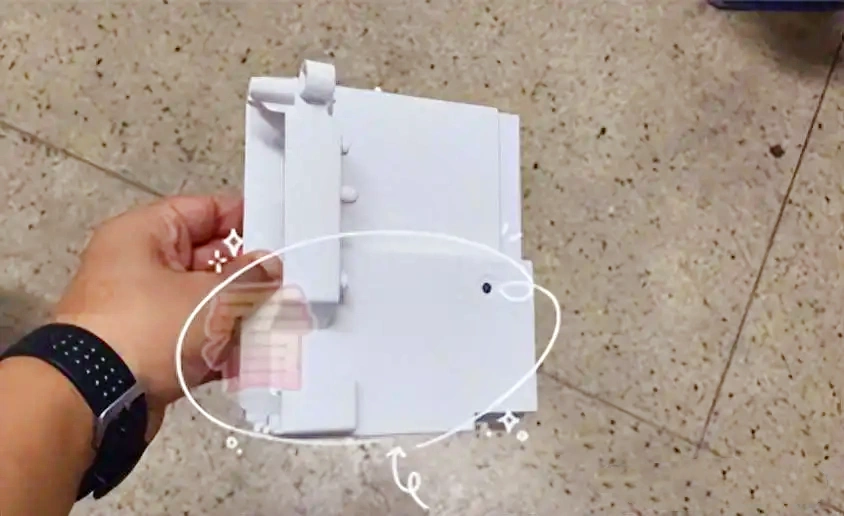
- Material: Flame-retardant ABS, a material known for its brittleness, hardness, and poor toughness.
- Structure: Deep, measuring 180mm.
- Draft angle: Extremely small, less than 1 degree, complicating the demolding process.
Initially, the mold was designed with a straight runner, and due to its large root, we discovered significant demolding resistance during production, resulting in a hollow defect in that area.
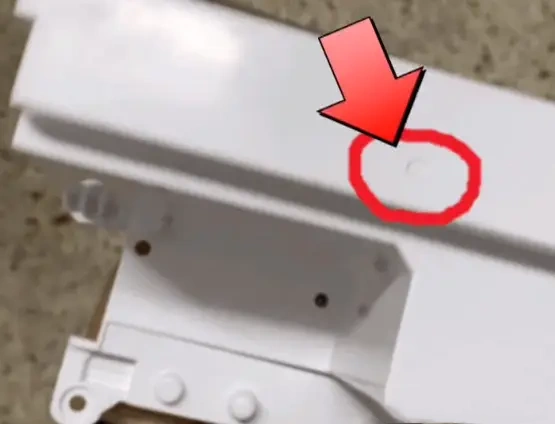
This problem seemed manageable, so we increased the holding pressure time to eliminate the void. However, a new issue arose: the ejector pins were designed with flat edges, and there were seven of them. The increased density of the product caused by our previous adjustments made demolding difficult, and since the brittle ABS didn’t deform, all seven pins broke during ejection. How could we solve this?
To address these issues, we implemented a series of adjustments:
Stage 1: Application of a release agent. This solved the demolding difficulty but compromised surface quality and increased defect rates.
Stage 2: Implementation of two-part ejection parameters. To resolve the broken pins, we conducted multiple tests using two-part ejection parameters. The first part was very slow, with sufficiently low pressure. Later, we increased the pressure to 15 MPa and reduced the speed to 3%, then accelerated after a 5mm distance, which surprisingly worked, and we managed a full day without breaking pins. However, this method was inefficient and not a good choice, so it was just a temporary fix.
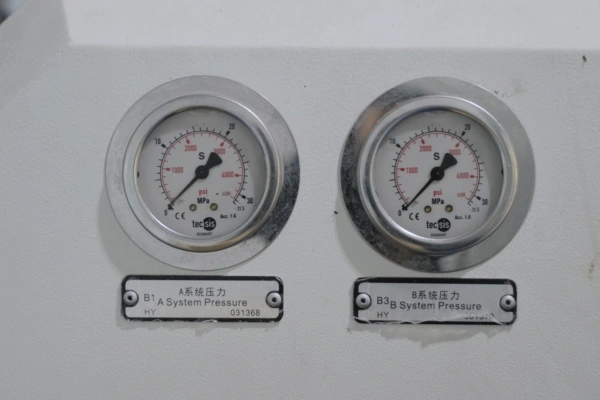
Stage 3: We used an intermittent holding pressure method to reduce product density. The first part involved using low pressure to allow the product to cool before the second holding phase. While this was a good idea in theory, we discovered that prolonged holding time led to cooling the material head, making it difficult to maintain pressure in the second phase. After discussions, we decided to shorten the length of the straight runner and modify the mold to make the runner shorter and deeper. This alleviated some issues, but we still experienced broken pins, so we had to mix methods from the first and second phases, which still wasn’t satisfactory.
Stage 4: We employed a reverse flow method. We knew that the straight runner’s gate had a long sealing time, so after the holding pressure ended, we increased material withdrawal to reduce the pressure at the nozzle. This created high cavity pressure and low nozzle pressure, causing the material to flow back and fill the void. This method worked well. The reverse flow method combined high holding pressure but for a short time, withdrawal, and cooling time before the melt, leading to successful results. Ultimately, cavity pressure was low, ejection speed was fast, and there were no voids, which was perfect. However, the method was intricate and difficult to control. For instance, if the holding time should be 1.8 seconds, even a slight extension of 0.5 seconds could cause issues. Due to the complexity, it was not recommended for mass production.
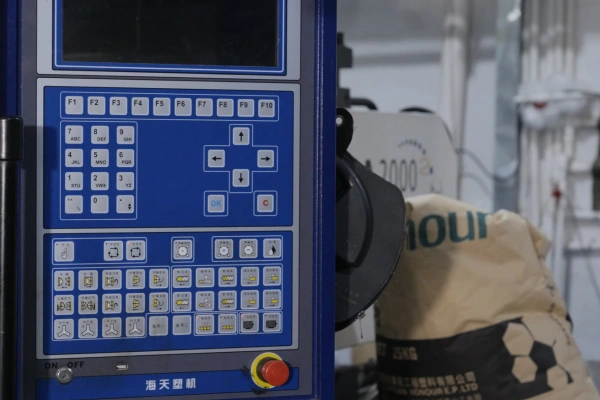
Stage 5: We attempted to modify the mold for in-mold cutting, but this failed as well because the cutter positioning was poor for achieving a flush cut at the gate.
Stage 6: We decided to switch to a hot runner system, which we are using now. You might wonder why we only considered the hot runner at this stage. If it were simple, we would have implemented it from the first phase. The main reason was the material; flame-retardant ABS has a drawback of easily generating black specks, which are difficult to clean, and hot runners combined with flame-retardant ABS produce white products, making it even easier to develop these impurities, which posed significant challenges for production. However, for production stability and technical consistency, the final solution was to replace the straight runner with a hot runner.
This case study illustrates that improving injection molding processes often involves finding the most appropriate solution rather than the theoretically optimal one. In product development, especially when dealing with special materials, process adjustments are crucial and unavoidable.