1. PA performance
PA is also a crystalline plastic (nylon is a tough, angular, translucent or milky white crystalline resin). As an engineering plastic, the molecular weight of nylon is generally 15,000-30,000. There are many varieties. Commonly used nylon 6, nylon 66, nylon 1010, nylon 610, etc. are used in injection molding.
Nylon has toughness, wear resistance and self-lubrication. Its advantages are high mechanical strength, good toughness, fatigue resistance, smooth surface, high softening point, heat resistance, low friction coefficient, wear resistance, self-lubrication, shock absorption and sound absorption, oil resistance, weak acid resistance, alkali resistance and general solvent resistance, good electrical insulation, self-extinguishing, non-toxic, odorless, and good weather resistance.
The disadvantages are high water absorption, poor dyeability, affecting dimensional stability and electrical properties. Fiber reinforcement can reduce water absorption, so that it can work under high temperature and high humidity. Nylon has a very good affinity with glass fiber (can be used for a long time within 100°C), corrosion resistance, light weight of parts, and easy molding. The main disadvantages of PA are: easy to absorb water, strict injection molding technology requirements, poor dimensional stability, and because of its high specific heat, the product is hot.
PA66 is the variety with the highest mechanical strength and the most widely used in the PA series. It has high crystallinity, so its rigidity, hardness and heat resistance are high. PA1010 was first created in my country in 1958, is translucent, has a low specific gravity, is more elastic and flexible, has lower water absorption than PA66, and has reliable dimensional stability.
Among nylons, nylon 66 has the highest hardness and rigidity, but the worst toughness. Various nylons are ranked by toughness as follows: PA66<PA66/6<PA6<PA610<PA11<PA12 The flammability of nylon is ULS44-2, the oxygen index is 24-28, the decomposition temperature of nylon is>299℃, and it will spontaneously combust at 449~499℃. Nylon has good melt fluidity, so the wall thickness of the product can be as small as 1mm.
2. Process characteristics of PA
2.1. PA is hygroscopic and must be fully dried before processing. The water content should be controlled below 0.3%. If the raw materials are dried well, the finished products will have high gloss. Otherwise, they will be relatively rough. PA will not gradually soften as the temperature rises, but will soften in a narrow temperature range close to the melting point. The melting point is very obvious, and once the temperature is reached, it will flow (unlike PS, PE, PP and other materials).
The viscosity of PA is much lower than that of other thermoplastics, and its melting temperature range is narrow (only about 5°C). PA has good fluidity, is easy to mold, and is also easy to flash. The nozzle is prone to “drooling”, and the glue needs to be larger.
PA has a high melting point and a high solidification point. The molten material in the mold may solidify at any time due to the temperature dropping below the melting point, which hinders the completion of the molding. Therefore, high-speed injection must be used (especially for thin-walled or long-process parts). Nylon molds must have sufficient exhaust measures.
When PA is in a molten state, it has poor thermal stability and is easy to degrade. The barrel temperature should not exceed 300℃, and the heating time of the melt in the barrel should not exceed 30 minutes. PA has high requirements for mold temperature. The high and low mold temperature can be used to control its crystallinity to obtain the required performance.
The mold temperature of PA material is better at 50-90℃, the processing temperature of PA1010 is preferably 220-240℃, and the processing temperature of PA66 is 270-290℃. PA products sometimes need to be “annealed” or “humidity-adjusted” according to quality requirements.
2.2.PA12 Before processing polyamide 12 or nylon 12, the humidity should be kept below 0.1%. If the material is stored in the air, it is recommended to dry it in 85℃ hot air for 4~5 hours. If the material is stored in a closed container, it can be used directly after 3 hours of temperature balance. Melting temperature 240~300C; for ordinary characteristic materials, do not exceed 310C, and for flame-retardant materials, do not exceed 270C.
Mold temperature: 30~40C for unreinforced materials, 80~90C for thin-walled or large-area components, and 90~100C for reinforced materials. Increasing the temperature will increase the crystallinity of the material. Accurate control of mold temperature is very important for PA12. Injection pressure: up to 1000bar (low holding pressure and high melting temperature are recommended). Injection speed: high speed (better for materials with glass additives).
Runners and gates: For materials without additives, the runner diameter should be around 30mm due to the low viscosity of the material. For reinforced materials, a large runner diameter of 5~8mm is required. The runner shape should be all circular. The injection port should be as short as possible.
Various forms of gates can be used. Do not use small gates for large plastic parts to avoid excessive pressure or shrinkage on the plastic parts. The gate thickness should be equal to the thickness of the plastic part. If a submerged gate is used, the recommended minimum diameter is 0.8mm. Hot runner molds are very effective, but require precise temperature control to prevent material leakage or solidification at the nozzle. If a hot runner is used, the gate size should be smaller than that of a cold runner.
2.3.PA6 Polyamide 6 or Nylon 6: Since PA6 easily absorbs moisture, special attention should be paid to drying before processing. If the material is supplied in waterproof packaging, the container should be kept closed. If the humidity is greater than 0.2%, it is recommended to dry in hot air above 80C for 16 hours. If the material has been exposed to air for more than 8 hours, it is recommended to vacuum dry at 105C for more than 8 hours.
Melting temperature: 230~280C, 250~280C for reinforced varieties. Mold temperature: 80~90C. Mold temperature significantly affects crystallinity, which in turn affects the mechanical properties of plastic parts. Crystallinity is important for structural parts, so a mold temperature of 80~90C is recommended.
For thin-walled, long-flow plastic parts, a higher mold temperature is also recommended. Increasing mold temperature can increase the strength and rigidity of plastic parts, but it reduces toughness. If the wall thickness is greater than 3mm, it is recommended to use a low-temperature mold of 20~40C. For glass-reinforced materials, the mold temperature should be greater than 80C. Injection pressure: generally between 750~1250bar (depending on the material and product design).
Injection speed: high speed (slightly lower for reinforced materials). Runner and gate: Since the solidification time of PA6 is very short, the location of the gate is very important. The gate aperture should not be less than 0.5*t (where t is the thickness of the plastic part). If a hot runner is used, the gate size should be smaller than that of a conventional runner, because the hot runner can help prevent the material from solidifying prematurely. If a submerged gate is used, the minimum gate diameter should be 0.75mm.
2.4.PA66 If the material is sealed before processing, then there is no need to dry it. However, if the storage container is opened, it is recommended to dry it in hot air at 85°C. If the humidity is greater than 0.2%, vacuum drying at 105°C for 12 hours is also required.
Melting temperature: 260~290°C. 275~280°C for products with glass additives. Melting temperature should be avoided above 300°C. Mold temperature: 80°C is recommended. Mold temperature will affect crystallinity, which will affect the physical properties of the product.
For thin-walled plastic parts, if a mold temperature below 40°C is used, the crystallinity of the plastic part will change over time, and annealing is required to maintain the geometric stability of the plastic part. Injection pressure: usually 750~1250bar, depending on the material and product design. Injection speed: high speed (slightly lower for reinforced materials).
Runner and gate: Since the solidification time of PA66 is very short, the location of the gate is very important. The gate aperture should not be less than 0.5*t (where t is the thickness of the plastic part). If a hot runner is used, the gate size should be smaller than that of a conventional runner because the hot runner can help prevent the material from solidifying prematurely. If a submerged gate is used, the minimum gate diameter should be 0.75mm.
3. Typical application range:
3.1. PA12 Polyamide 12 or Nylon 12 Application range: Water meters and other commercial equipment, cable sleeves, mechanical cams, sliding mechanisms and bearings, etc.
3.2. PA6 Polyamide 6 or Nylon 6 Application range: Due to its good mechanical strength and stiffness, it is widely used in structural parts. Due to its good wear resistance, it is also used to manufacture bearings.
3.3. PA66 Polyamide 66 or Nylon 66 Application range: Compared with PA6, PA66 is more widely used in the automotive industry, instrument housings and other products that require impact resistance and high strength.
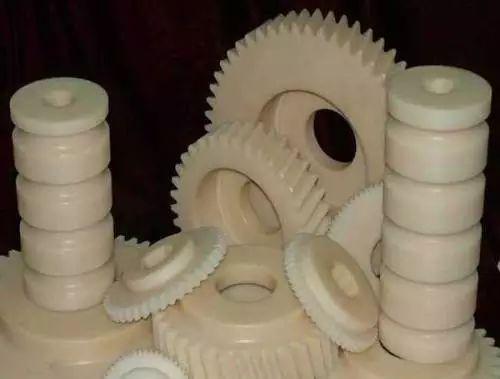