1. Performance of PP
PP is a crystalline polymer. Among commonly used plastics, PP is the lightest, with a density of only 0.91g/cm3 (smaller than water). Among general plastics, PP has the best heat resistance, with a heat deformation temperature of 80-100℃, and can be boiled in boiling water. PP has good stress cracking resistance and a high bending fatigue life, commonly known as “100-fold glue”.
The comprehensive performance of PP is better than that of PE materials. PP products are light, tough and chemically resistant. Disadvantages of PP: low dimensional accuracy, insufficient rigidity, poor weather resistance, easy to produce “copper damage”, it has post-shrinkage phenomenon, and after demolding, it is easy to age, become brittle and deform. PP has always been the main raw material for manufacturing fibers because of its coloring ability, wear resistance, chemical resistance and favorable economic conditions.
PP is a semi-crystalline material. It is harder than PE and has a higher melting point. Since homopolymer PP is very brittle above 0°C, many commercial PP materials are random copolymers with 1~4% ethylene or clamp copolymers with higher ethylene content. Copolymer PP materials have lower heat distortion temperature (100°C), low transparency, low gloss, and low rigidity, but have stronger impact strength. The strength of PP increases with the increase of ethylene content.
The Vicat softening temperature of PP is 150°C. Due to the high crystallinity, the surface stiffness and scratch resistance of this material are very good.
PP does not have environmental stress cracking problems. Usually, PP is modified by adding glass fiber, metal additives or thermoplastic rubber. The flow rate MFR of PP ranges from 1 to 40. Low MFR PP materials have better impact resistance but lower ductility. For materials with the same MFR, the strength of copolymers is higher than that of homopolymers.
Due to crystallization, the shrinkage rate of PP is quite high, generally 1.8~2.5%. And the directional uniformity of shrinkage rate is much better than that of materials such as HDPE. Adding 30% glass additive can reduce the shrinkage rate to 0.7%.
Both homopolymer and copolymer PP materials have excellent moisture absorption resistance, acid and alkali corrosion resistance, and solubility resistance. However, it has no resistance to aromatic hydrocarbon (such as benzene) solvents, chlorinated hydrocarbon (carbon tetrachloride) solvents, etc. PP is not as resistant to oxidation at high temperatures as PE.
2. Process characteristics of PP
PP has good fluidity at melting temperature and good molding performance. PP has two characteristics in processing:
First: The viscosity of PP melt decreases significantly with the increase of shear rate (less affected by temperature);
Second: The molecular orientation is high and the shrinkage rate is large. The processing temperature of PP is 220~275℃. It is better not to exceed about 275℃. It has good thermal stability (decomposition temperature is 310℃), but at high temperature (270-300℃), it may degrade if it stays in the barrel for a long time. Since the viscosity of PP decreases significantly with the increase of shear speed, increasing the injection pressure and injection speed will improve its fluidity, improve shrinkage deformation and sinking. Mold temperature (40~80℃), 50℃ is recommended.
The degree of crystallization is mainly determined by the mold temperature, which should be controlled within the range of 30-50℃. PP melt can pass through a very narrow mold gap and appear flashing. During the melting process, PP absorbs a large amount of melting heat (large specific heat), and the product is relatively hot after leaving the mold.
PP materials do not need to be dried during processing, and the shrinkage rate and crystallinity of PP are lower than those of PE. Injection speed usually uses high-speed injection molding to reduce internal pressure to a minimum. If defects appear on the surface of the product, low-speed injection molding at a higher temperature should be used. Injection pressure: can be as high as 1800bar.
Runner and gate: For cold runners, the typical runner diameter range is 4~7mm. It is recommended to use injection ports and runners that are round throughout. All types of gates can be used. The typical gate diameter range is 1~1.5mm, but gates as small as 0.7mm can also be used. For edge gates, the minimum gate depth should be half the wall thickness; the minimum gate width should be at least twice the wall thickness. PP materials can fully use hot runner systems.
PP has always been the main raw material for making fibers because of its coloring ability, wear resistance, chemical resistance and favorable economic conditions.
3. Typical application range:
Automotive industry (mainly using PP containing metal additives: fenders, vents, fans, etc.), appliances (dishwasher door linings, dryer vents, washing machine frames and covers, refrigerator door linings, etc.), daily consumer goods (lawn and gardening equipment such as lawn mowers and sprinklers, etc.).
Injection molded products are the second largest market for PP homopolymer, including containers, sealers, automotive applications, household items, toys, and many other consumer and industrial end-use applications.
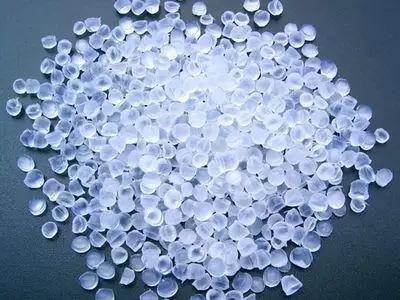