We have gained extensive experience in waterproof sealing, and below are several successful cases that we hope will help you and your team explore the most suitable solution for your products.
Case 1: Polycarbonate Case with K31 FIPFG Sealant For this product, we used K31 FIPFG (Form-In-Place Foam Gasket) sealant applied to a polycarbonate case part and compressed by an aluminum die-cast rear part. After the material components react, the foam gasket becomes tack-free and can be installed into mating components. The sealing function is achieved by compressing approximately 30–60% of the cured foam gasket, ensuring an IP67 waterproof rating.
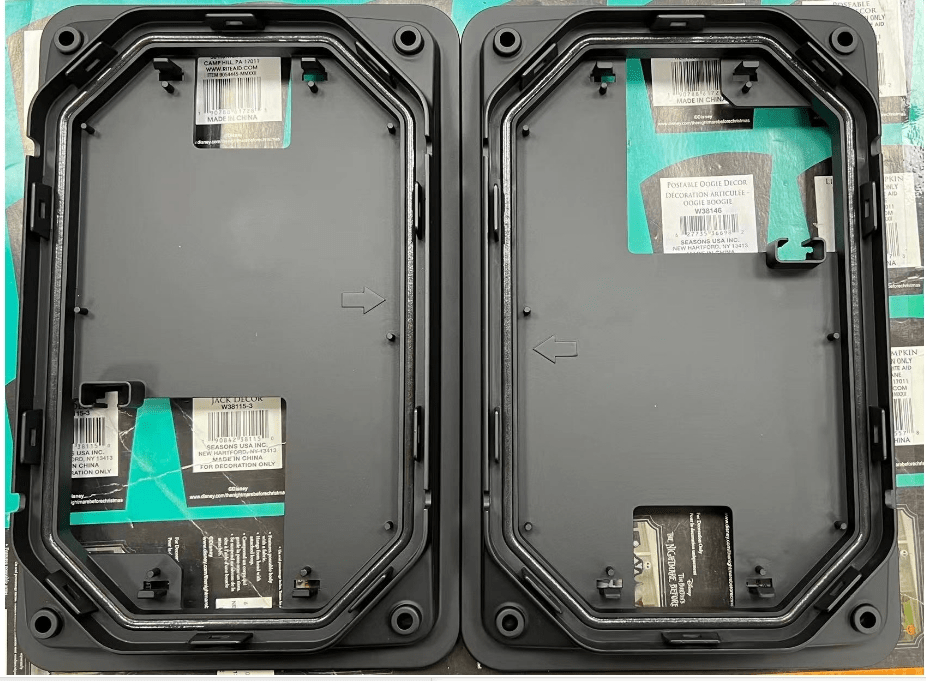
Case 2: Marine-Grade Display Cover – UV, Saltwater, and Vibration Resistance For display covers intended for marine applications, which are exposed to intense sunlight, corrosive saltwater, and harsh conditions, we carefully selected materials suited for outdoor and marine environments. Key properties include UV resistance, saltwater resistance, high flowability, and shock and vibration resistance. These factors are crucial in mold design, as they directly impact the final product’s performance and shrinkage. Additionally, ensuring the planarity of sealing surfaces is essential for a reliable seal, especially when dealing with glass screens or LCDs. Screw inserts must be over-molded with care to avoid cracks, stains, or defects, ensuring seamless integration with the housing.
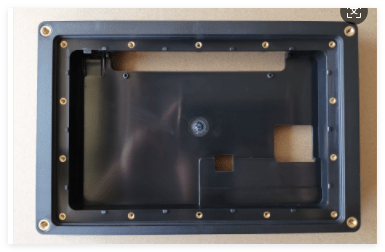
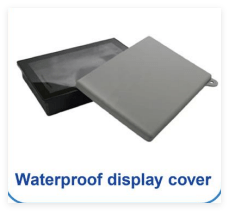
Case 3: Overmolding of Plastic and Stainless Steel with Waterproofing Solution In this case, we initially attempted ultrasonic welding to join a plastic base part with a stainless steel component. However, due to the weight of the base, the product was damaged during transportation. To address this, we worked closely with the customer to redesign the structure, replacing ultrasonic welding with a screw-locking mechanism and incorporating a silicone gasket for improved waterproofing.
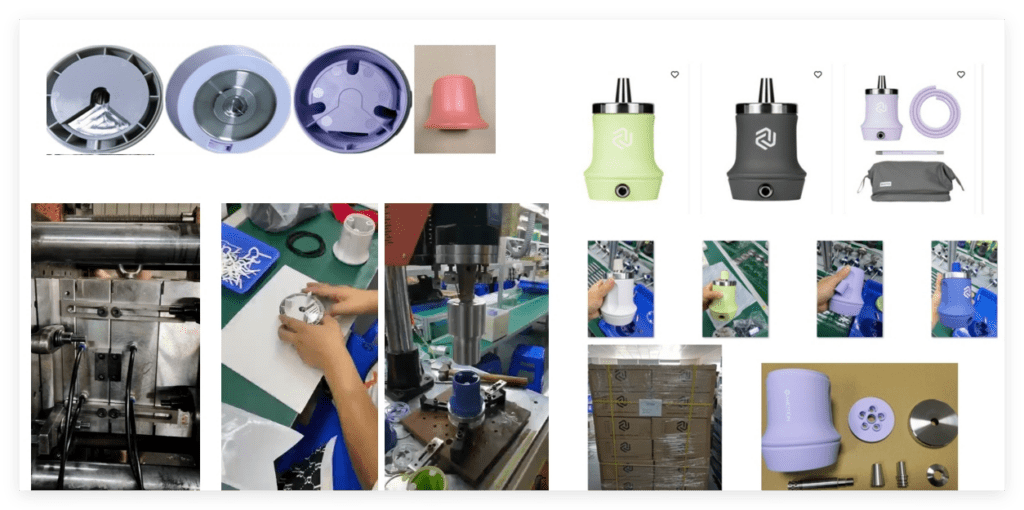
Case 4: TPU Rubber Caps with Overmolding and Ultrasonic Welding This case features purple TPU rubber caps over-molded with a white top cover. The nuts are molded directly into the cap, and ultrasonic welding is used for the light guide column. The plastic key caps are glued onto the purple rubber pad, and UV treatment is applied to the printed characters to increase durability, ensuring they can withstand up to 1 million uses.
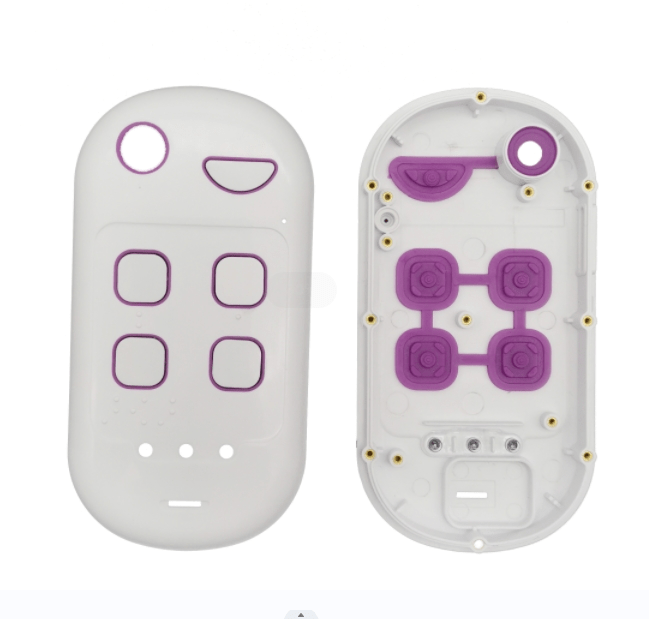