Depending on the structure and requirements of plastic products, the structure of injection molds also varies. Common injection mold structures include single-parting surface injection molds, multi-parting surface injection molds, oblique guide pin side-core pulling injection molds, oblique pin inner-core pulling injection molds, and hot runner injection molds.
1. Single-Parting Surface Injection Mold
A single-parting surface injection mold, also known as a two-plate injection mold, is commonly used in large gate injection molding. This type of mold has a simple structure and is highly practical for plastic molding, making it widely used. However, its disadvantage is that the gate is large, often requiring an additional step to remove it, and it leaves gate marks on the product surface. Therefore, it is suitable for injection products where surface appearance is not a primary concern.
2. Multi-Parting Surface Injection Mold
A multi-parting surface injection mold has two or more parting surfaces, the most common being a double-parting surface. The double-parting surface injection mold, often called a three-plate mold, is typically used for products with pinpoint gates and is hence also referred to as a small gate mold. This mold type is widely applied, primarily for single-cavity or multi-cavity molds with pinpoint gates, molds with lateral parting mechanisms set on the fixed mold side, and molds that require sequential parting due to special plastic part structures.
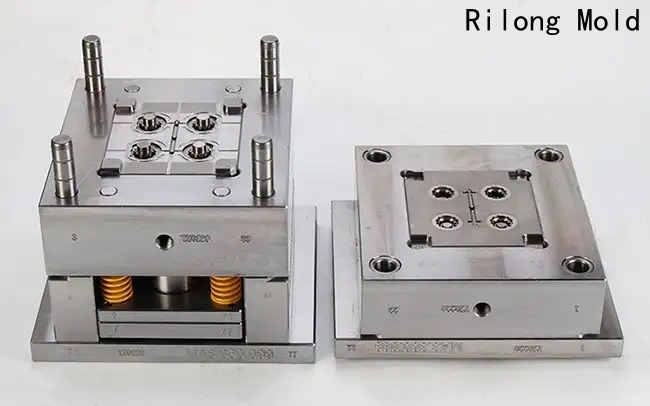
The first parting operation aims to remove the solidified runner material, while the second parting separates the feeding port from the runner material and the plastic part, eliminating the need for additional runner material removal after ejection.
3. Oblique Guide Pin Side-Core Pulling Injection Mold
When the sidewall of a plastic part has through-holes, recesses, or protrusions, the molding components must be designed to move laterally. The entire mechanism that drives the core to move sideways is called the side-core pulling mechanism or lateral core-pulling mechanism. There are various types of side-core pulling mechanisms, including oblique guide pin side-core pulling, hydraulic core pulling, and pneumatic core pulling. Among them, the oblique guide pin side-core pulling mechanism is the most common, as shown in Figure 3.25. During mold opening, the oblique guide pin first drives the slide block outward. Once the side core is completely released from the product, the ejection mechanism begins to operate and ejects the molded part.
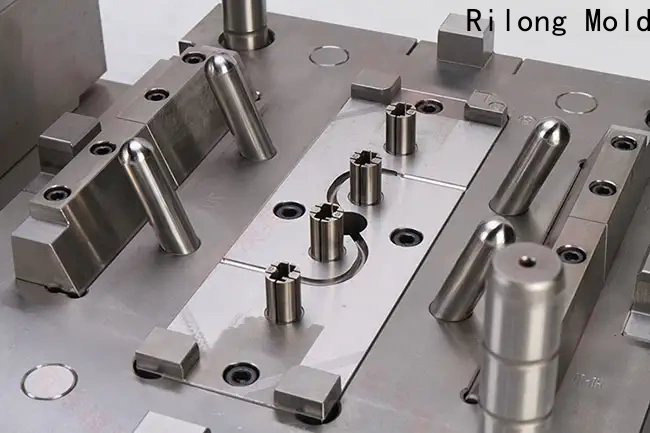
4. Oblique Pin Inner-Core Pulling Injection Mold
When the interior of a product has undercuts, oblique pins are required to mold these features. Molds equipped with oblique pins for internal core pulling are collectively referred to as oblique pin inner-core pulling injection molds. These molds have a relatively complex structure, requiring additional oblique pin mechanisms within the mold. During mold opening, the front and rear molds first separate. Then, the injection molding machine’s ejection mechanism pushes the mold’s ejector plate in the demolding direction. At this stage, the oblique pin gradually withdraws from the undercut area of the product. Once fully released, the ejector mechanism of the mold ejects the molded product.
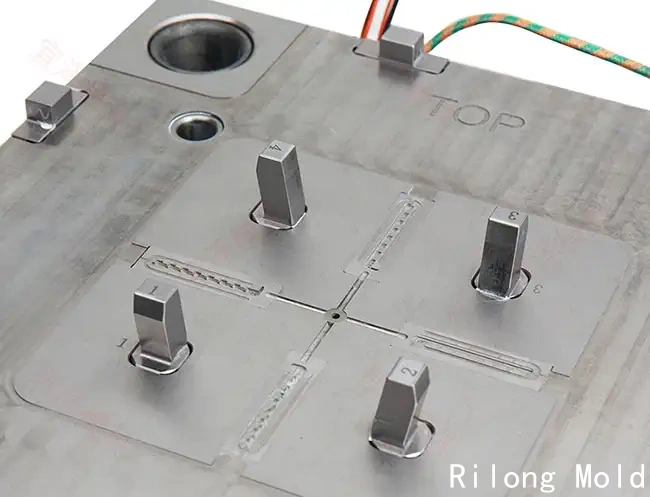
5. Hot Runner Injection Mold
With the rapid development of automated injection molding processes, hot runner injection molds are increasingly being adopted. The key difference between hot runner molds and conventional injection molds is that the plastic in the gating system does not solidify during the injection process and does not come off with the molded part during demolding. For this reason, hot runner molds are also called runnerless molds. The main advantages of hot runner injection molds include:
① Minimizing material waste, saving raw materials, and eliminating the need for cold runner removal.
② Reducing pressure loss in the feeding system, making full use of injection pressure, which helps ensure the quality of molded parts.
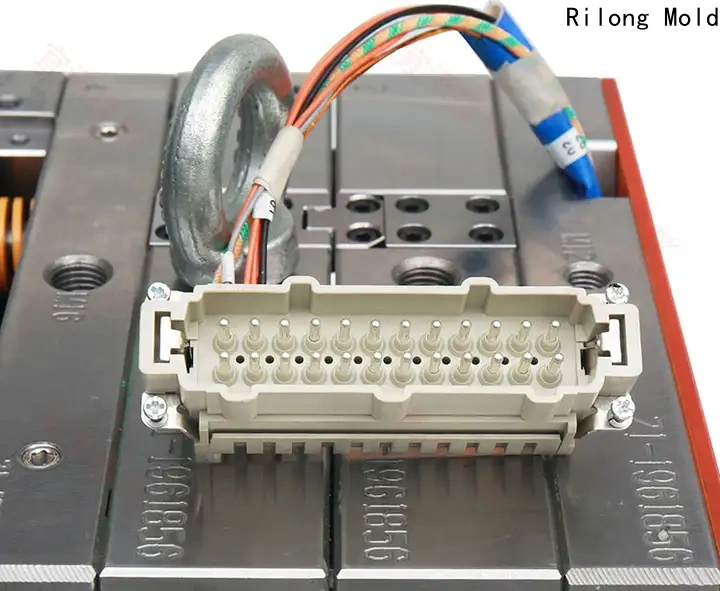
Hot runner injection molds are easy to identify as they typically have cables, connectors, and junction boxes on the mold, as shown in the image above. Due to their complex structure, high cost, and strict mold temperature control requirements, hot runner molds are best suited for mass production. The first parting operation aims to remove the solidified runner material, while the second parting separates the feeding port from the runner material and the plastic part, eliminating the need for additional runner material removal after ejection.