在注塑行业,特别是在处理特殊材料和大尺寸产品时,存在显著的隐性成本和挑战。许多人可能没有意识到,注塑不仅仅是一个简单的生产过程;它涉及大量的准备、调整和微调,以确保产品质量和稳定性。这在试生产阶段尤为明显,工厂面临巨大的压力。
- 特殊材料的挑战
特殊材料,例如耐高温、玻璃纤维填充树脂或其他功能性塑料,通常具有更高的熔点和较差的流动性。这些特性要求在成型过程中进行更精确的温度控制和注射压力。
这些材料的采购和加工成本也更高,设备需要更加专业和精细的调整。
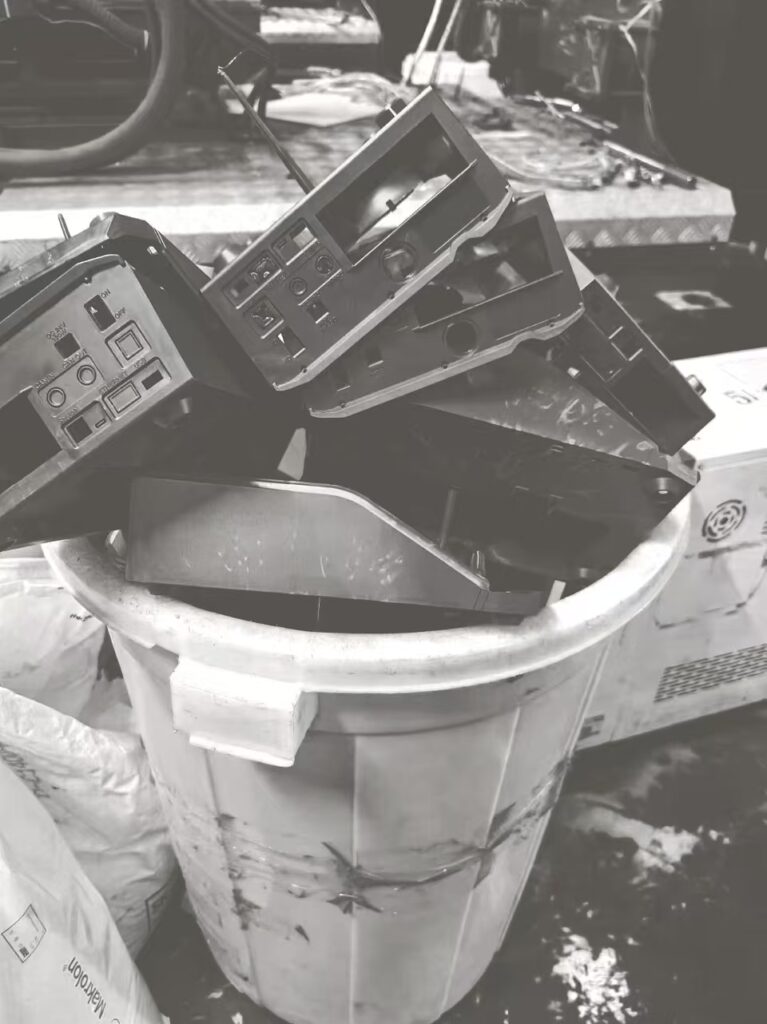
2. 大尺寸产品的复杂性
对于较大的产品,注塑机的选择和调整变得更加复杂。大型设备不仅消耗更多能源,需要更多维护,还需要更长的时间来确保稳定运行。
随着产品尺寸的增加,模具的设计和制造也变得更加复杂,通常需要多次修改和调整。
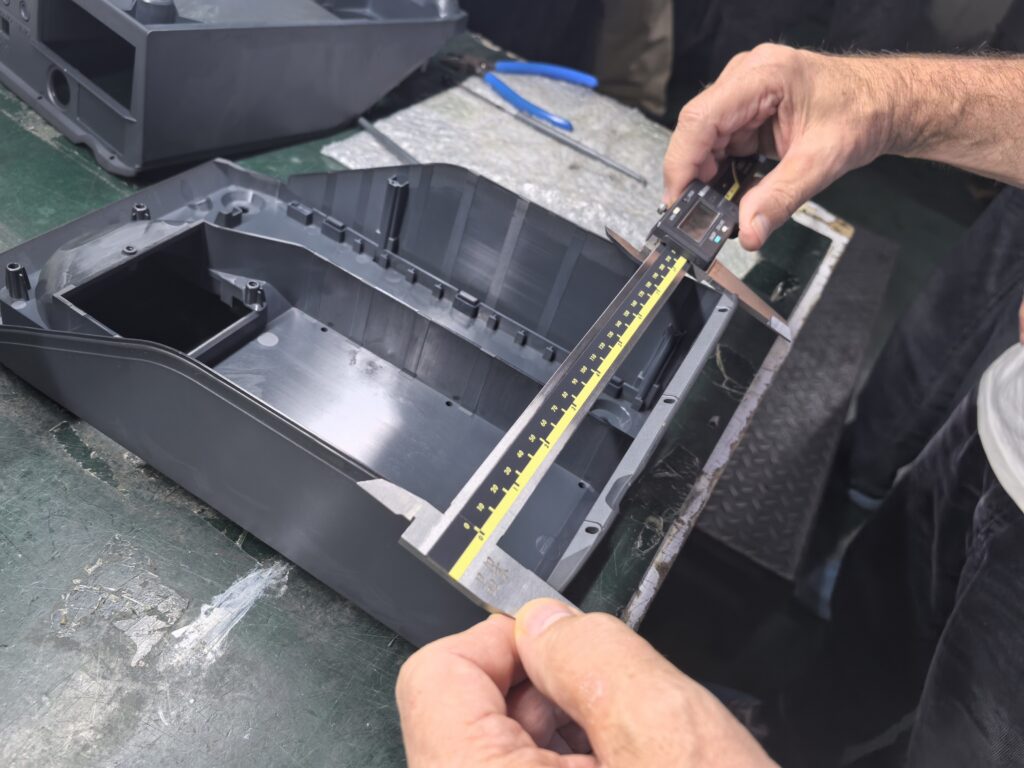
3. 试生产的成本
在试生产阶段,为了调整机器参数,会消耗大量的原材料。对于特殊材料而言,每次调整和优化都可能导致材料的浪费。
由于这些产品的复杂性,调整周期可能从半天持续到整整一天。这段时间,加上材料损耗,导致生产成本更高。
4. 高昂的人工和设备成本
注塑工厂不仅需要投入大量人力来进行机器调整和生产,而且操作员和工程师的劳动力成本也在不断上升。
大型设备的使用和维护需要巨额投资,这些设备的运营成本直接影响产品的定价。
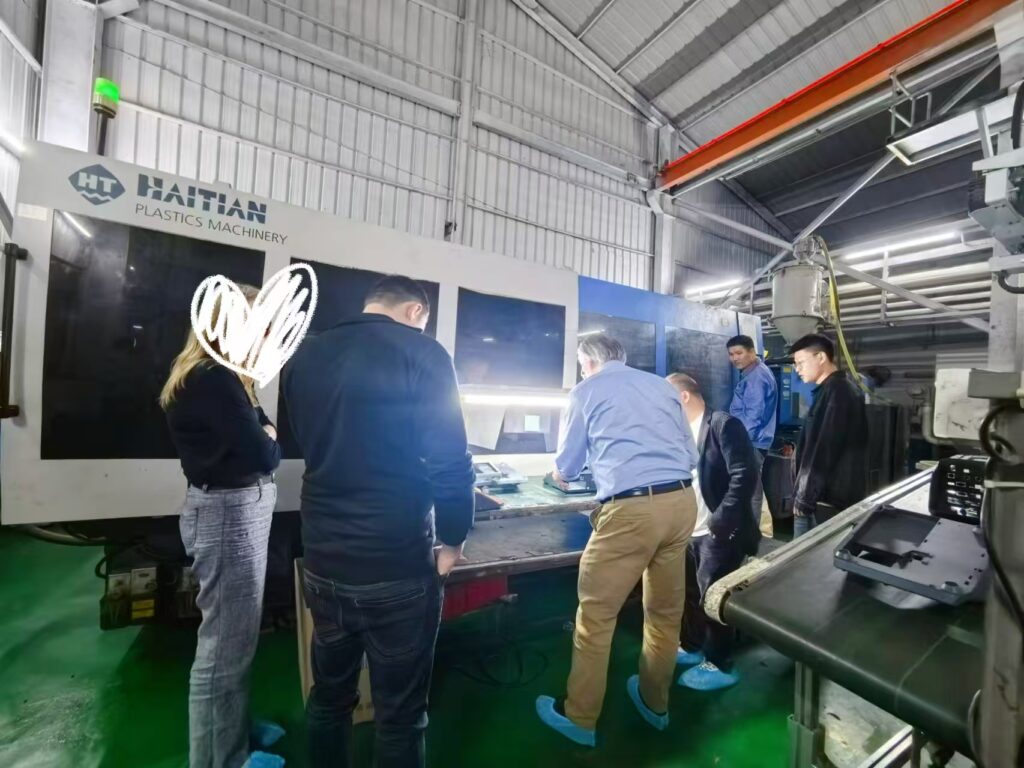
5. 小批量试订单的困境
在处理小批量试订单时,生产线的效率会大幅下降。由于注塑成本高昂且调整时间长,小订单通常难以盈利。工厂往往需要帮助客户进行小批量市场测试。
小批量生产不仅影响整体生产控制,而且从经济角度来看,往往无法覆盖成本,使工厂几乎无利润。
面对这些挑战,注塑工厂不仅需要管理高昂的成本,还必须专注于优化生产控制,以最大化效率并减少浪费。客户需要了解,在生产特殊材料和大尺寸产品时,合理的生产成本和时间投入对于确保产品质量和市场需求至关重要。