In modern manufacturing, achieving fast and secure connections between plastic components is a constant challenge. Traditional fastening methods like screws are time-consuming and labor-intensive, while adhesives can pose environmental and reliability concerns. Ultrasonic welding is revolutionizing the way plastic parts are joined—efficiently, cleanly, and reliably.
What is Ultrasonic Welding?
Ultrasonic welding is a technique that uses high-frequency vibrations (typically 20–40 kHz) to generate localized heat through friction. This heat causes the plastic interface to melt and fuse within seconds—no adhesives, screws, or solvents required. Welded joints typically reach 80–95% of the parent material’s strength.
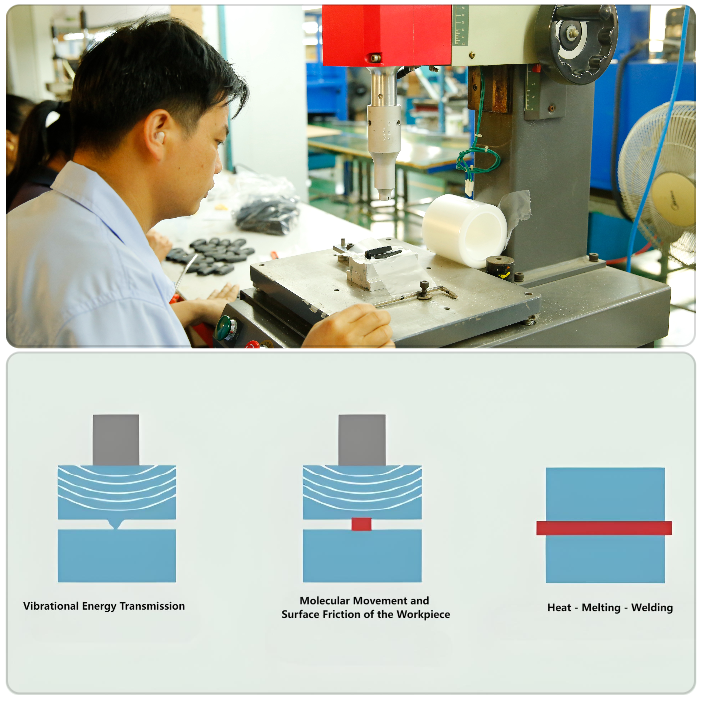
Key Advantages
- Fast Process: Welds completed in just 0.1–3 seconds
- Eco-Friendly: No chemicals, fumes, or emissions
- High Strength: Strong, durable, and reliable joints
- Cost-Efficient: No consumables, low energy usage
Real-World Application Cases
Case 1: Underwater Tracker for Marine Application
Challenge: A UK client required a waterproof housing for an underwater tracker device, capable of withstanding high pressure at 40 meters depth.
Solution: Ultrasonic welding was used to seal the plastic housing, ensuring robust and reliable waterproof performance.
工艺: The welded samples were sent to a specialized test lab for pressure testing. The enclosure had to withstand 5 bar (73 PSI) to meet the underwater operational requirements.
Result:
*Successfully deployed in 40-meter-deep underwater environments
*Passed third-party pressure and sealing verification
*Approved for mass production

Case 2: Ultrasonic Welding of LED Cover to Housing – Achieving IP67 Protection
Challenge: A customer required a robust and waterproof assembly for an outdoor LED HMI control module. The PC LED cover needed to be securely sealed to the plastic housing while meeting the IP67 dust and water resistance standard.
Difficulty: Ensuring both structural integrity and reliable sealing. Traditional methods such as snap-fits or adhesive bonding were insufficient to meet the sealing requirements.
Solution: Ultrasonic welding was used to precisely position and fuse the LED cover to the housing. By optimizing the welding energy and joint design, the surface texture remained intact while achieving strong bonding and excellent sealing performance.
Result:
*More compact and durable product structure, suitable for outdoor and humid environments
*Successfully passed IP67 sealing tests
*No adhesive required – eco-friendly and eliminates seal aging issues
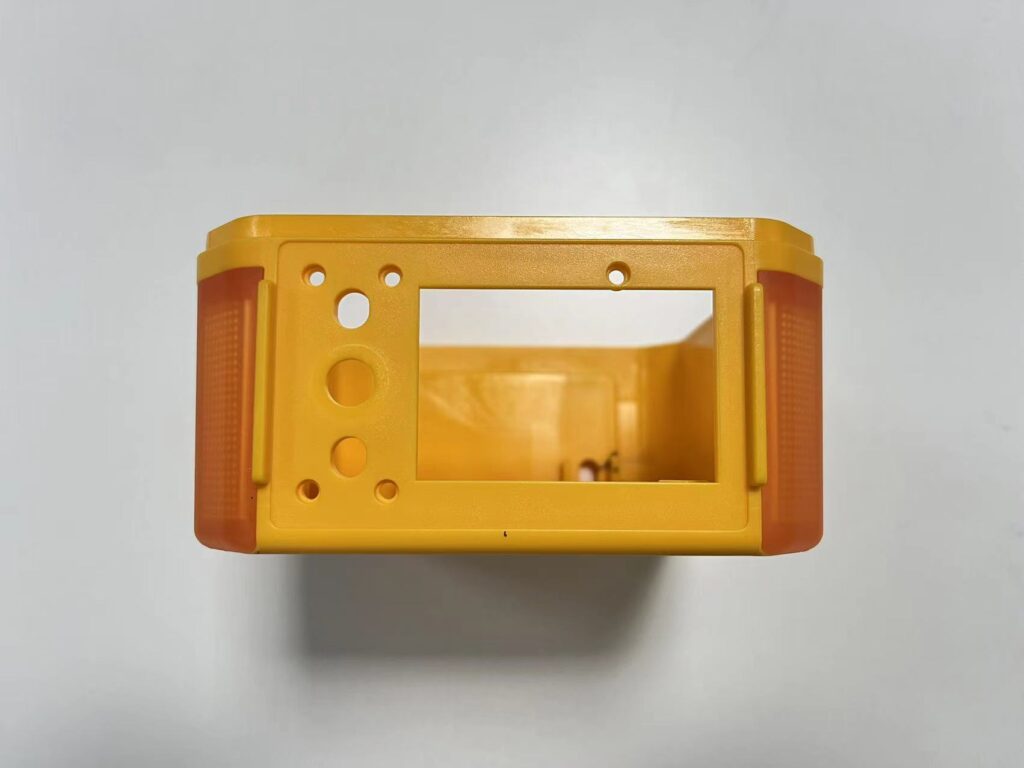
Case 3: Ultrasonic Welding of Transparent Display Window to Telephone Housing
Challenge: In the assembly of an HMI telephone unit, a transparent PC display window needed to be precisely mounted into the plastic housing. It was critical to ensure clear visibility without adhesive marks, fogging, or misalignment.
Solution: Ultrasonic welding was used to achieve a strong and seamless bond between the optical window and the housing. By carefully controlling the welding energy and joint design, the process ensured a distortion-free and clean finish.
Result:
*Improved assembly consistency and significantly reduced defect and rework rates
*Maintained high optical clarity with no fogging or adhesive residue
*Clean and precise weld lines for a refined appearance
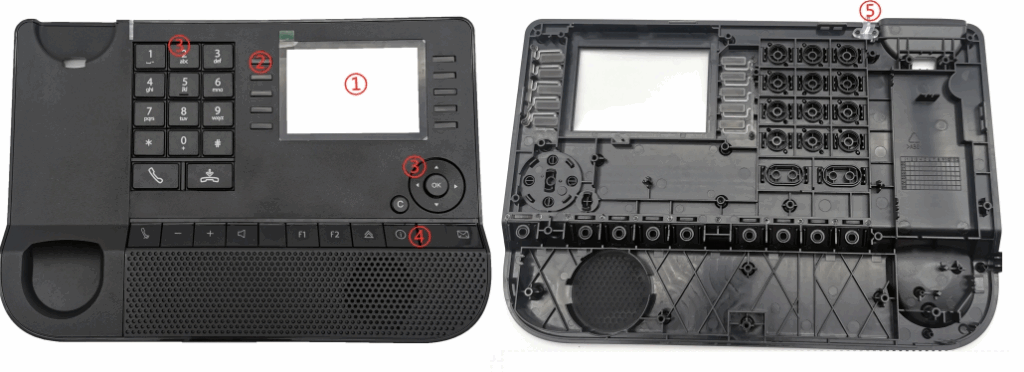
Material Compatibility Overview
Material Type | Weldability | Common Applications |
---|---|---|
ABS | Excellent | Automotive interiors, appliance housings |
PC | Good | Transparent containers, optical parts |
PS | Excellent | Packaging, toys |
PP | Moderate | Food containers, piping |
Note: Weldability may vary depending on material combinations and should be evaluated on a case-by-case basis.
With extensive experience in ultrasonic welding, we offer tailored solutions based on product structure, material properties, and performance requirements.
If you have a suitable project or idea, please feel free to contact us—we’re here to support you with professional guidance and reliable technical solutions.