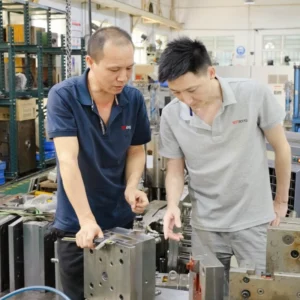
Injection molding is a highly versatile and efficient manufacturing process, but like any process, it’s not without its challenges. From surface imperfections to dimensional inaccuracies, injection molding defects can arise for various reasons, impacting part quality and production efficiency. In this blog, we’ll explore some of the most common injection molding defects, their causes, and strategies for troubleshooting and prevention.
Identifying Common Injection Molding Defects:
- Warping: Warping occurs when uneven cooling causes differential shrinkage across the part, resulting in distortion or deformation. Common causes of warping include inadequate cooling, improper mold temperature control, and uneven wall thickness.
- Sink Marks: Sink marks are depressions or dimples on the surface of the part caused by localized shrinkage during cooling. Factors contributing to sink marks include inadequate packing pressure, insufficient cooling time, and thick sections in the part design.
- Flash: Flash refers to excess material that escapes from the mold cavity, typically around the parting line or between mold components. Causes of flash include excessive injection pressure, worn or damaged molds, and insufficient clamping force.
- Short Shots: Short shots occur when the mold cavity is not completely filled with molten material, resulting in incomplete parts. Common causes of short shots include inadequate injection pressure, air entrapment, and improper gating or venting.
- Burn Marks: Burn marks are discolorations or black spots on the surface of the part caused by overheating or degradation of the material. Factors contributing to burn marks include excessive barrel temperature, prolonged residence time, and poor ventilation.
Troubleshooting and Prevention Strategies:
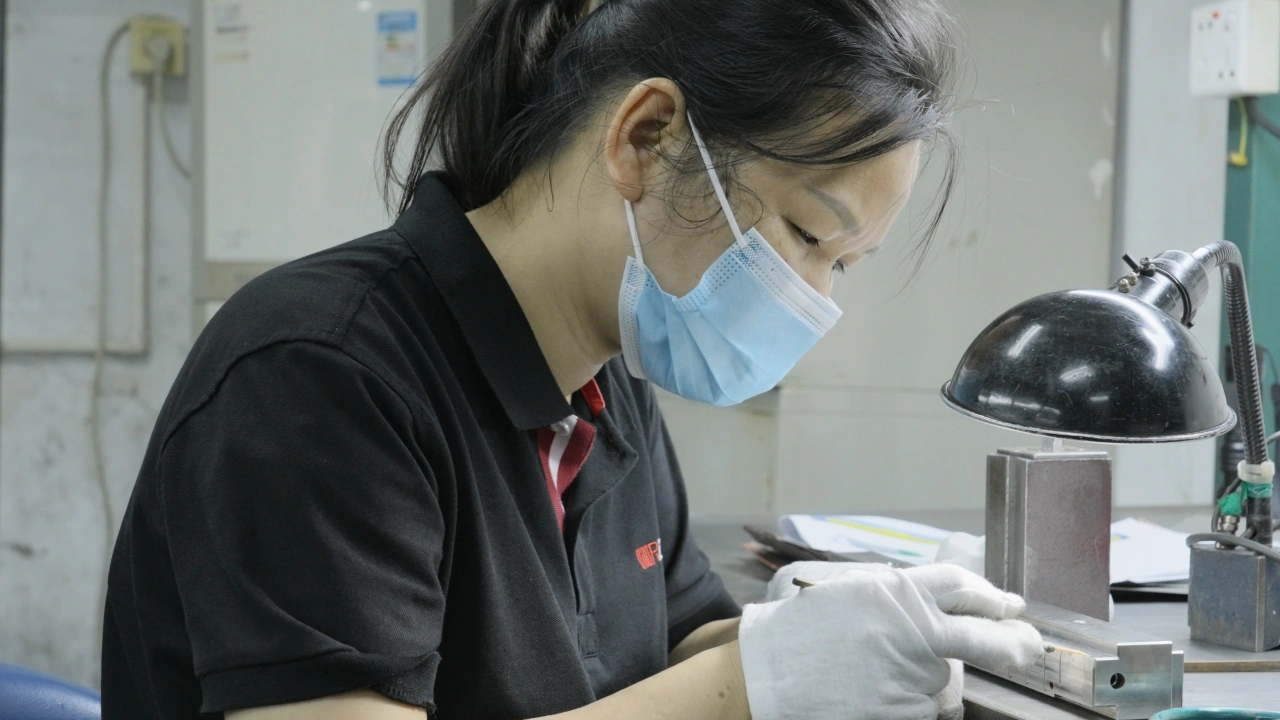
- Optimize Process Parameters: Fine-tuning injection molding parameters such as temperature, pressure, and cycle time can help alleviate many common defects. Conducting systematic process optimization trials and utilizing process monitoring technologies can help identify optimal settings for achieving desired part quality.
- Improve Mold Design: Ensuring proper mold design with adequate cooling channels, appropriate draft angles, and uniform wall thickness can minimize defects such as warping, sink marks, and flash. Collaborating with experienced mold designers and engineers can help optimize mold designs for improved performance and efficiency.
- Enhance Material Selection: Selecting the right material for the application and understanding its processing characteristics can help mitigate defects related to material properties. Conducting material testing and qualification prior to production can help identify potential issues and ensure compatibility with the injection molding process.
- Implement Quality Assurance Measures: Implementing robust quality assurance measures, such as regular mold maintenance, in-process inspection, and quality control checks, can help identify and address defects early in the production process. Utilizing advanced inspection techniques, such as automated vision systems and dimensional metrology, can help ensure consistent part quality and adherence to specifications.
Conclusion: Injection molding defects can pose challenges for manufacturers, impacting part quality, production efficiency, and profitability. By understanding the causes of common defects and implementing proactive troubleshooting and prevention strategies, manufacturers can optimize their injection molding processes and achieve higher levels of quality, consistency, and reliability. With continuous improvement and a focus on quality assurance, injection molding remains a highly effective manufacturing solution for producing high-quality plastic parts.