In the plastic injection molding industry, molds are the core equipment for producing high-quality plastic parts. The maintenance and management of molds directly impact production efficiency, product quality, and production costs. However, mold failures are inevitable, and understanding the common causes and how to prevent these issues is crucial for businesses.
Today, we will explore the common causes of mold failures and share how proper maintenance and management can extend the mold’s lifespan and prevent unnecessary losses in production.
1. Material Defects
One of the primary causes of mold failures is the use of substandard materials. Poor-quality or unsuitable raw materials can cause cracks, deformation, and even failure to properly inject plastic.
Prevention: Choose reliable suppliers to ensure the materials meet relevant quality standards and conduct necessary physical property testing.
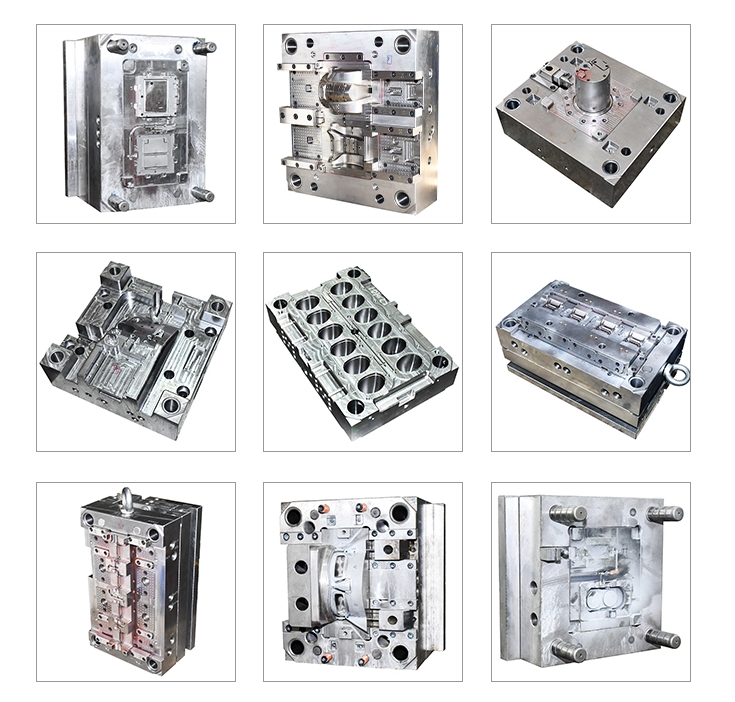
2. Improper Cooling System
An improperly designed cooling system can lead to hot spots, uneven cooling, and even cause plastic parts to deform. Insufficient cooling also affects production efficiency, leading to early mold wear.
Prevention: Ensure the mold’s cooling system is properly designed with evenly distributed cooling channels to avoid localized overheating.
3. Mold Wear
Over time, molds are subject to wear and tear, resulting in a loss of precision. This is especially true under high-intensity and high-temperature conditions, where wear can accelerate and affect the quality of the produced parts.
Prevention: Regularly inspect the mold for wear and carry out timely repairs or replacements. Using high-quality mold steel can slow down the wear process.
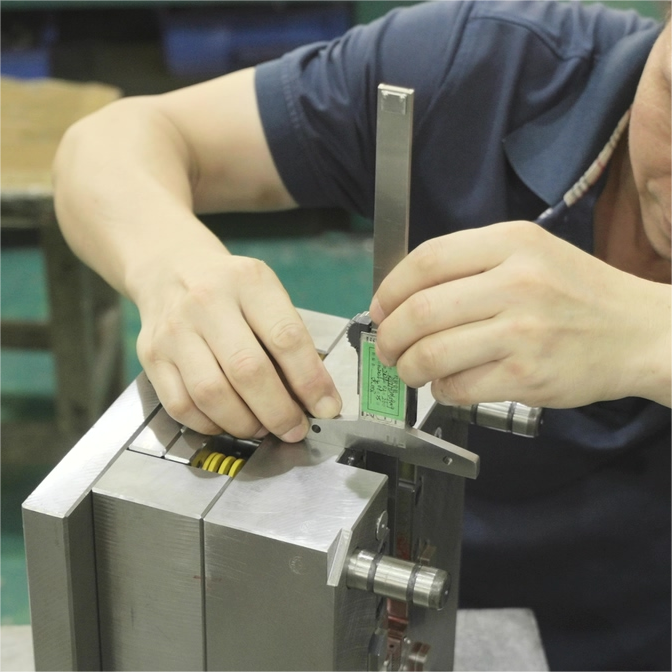
4. Poor Mold Design
Mold design defects are a common cause of failures. Poorly designed molds may lead to unwanted voids, warping, or even failure to eject the part.
Prevention: Use advanced simulation software (such as mold flow analysis) during the design phase to conduct thorough design assessments and ensure the mold meets production requirements.
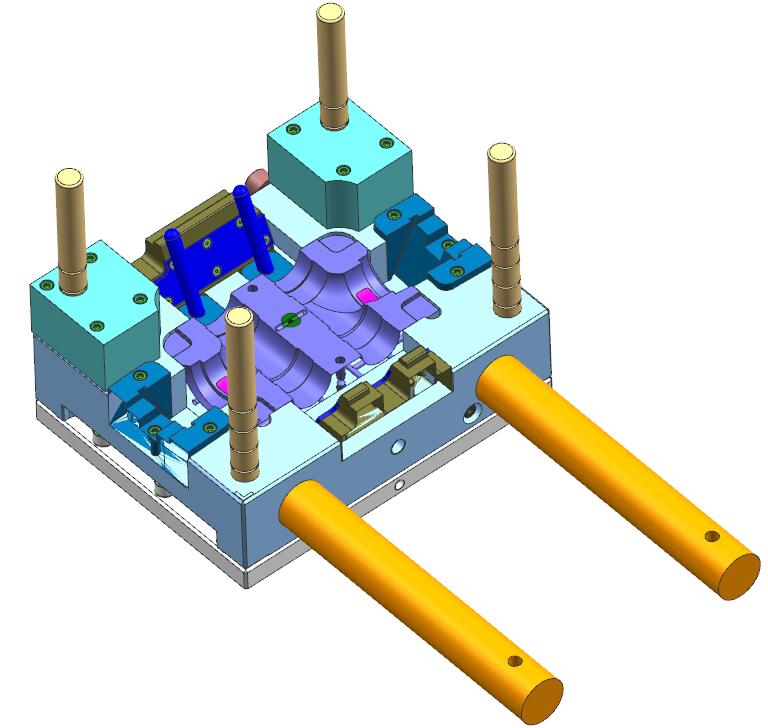
5. Improper Injection Pressure
Excessive or insufficient injection pressure can lead to mold failures. Too high pressure may deform or even break the mold, while too low pressure can result in short shots.
Prevention: Set appropriate injection pressures based on the plastic material and mold requirements, and monitor the process in real-time.
6. Incorrect Equipment Settings
Incorrect equipment settings, especially errors in temperature, pressure, and time, can result in unstable mold performance and affect production efficiency.
Prevention: Operators should follow standard operating procedures (SOP) when setting up the injection molding machine, regularly calibrating equipment to ensure optimal parameters.
7. Contamination
If molds are contaminated with dust, impurities, or moisture, it can affect the molding process and even cause clogging or corrosion of the mold.
Prevention: Maintain a clean production environment and regularly inspect molds to ensure their surfaces are free of contaminants.
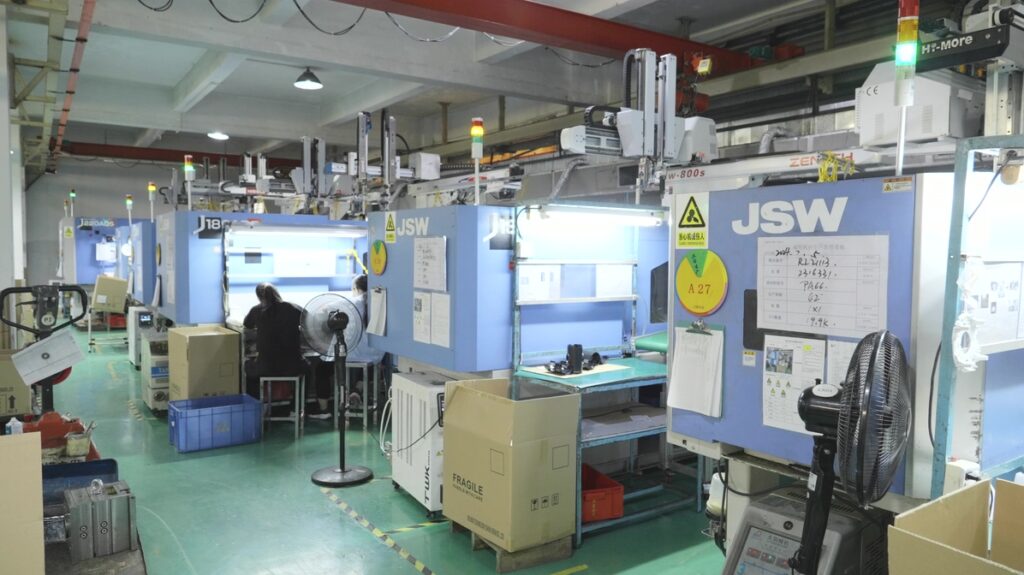
8. Tool Damage
Long-term use of mold tools (such as inserts, ejector pins, nozzles, etc.) without maintenance can lead to damage, causing mold failure.
Prevention: Regularly inspect and replace mold tools as necessary.
9. High-Temperature Issues
If a mold is exposed to excessively high temperatures for extended periods, it can cause wear, deformation, or material aging.
Prevention: Regularly monitor the mold’s operating temperature to prevent overheating. Use cooling systems when necessary to maintain stable temperatures.
10. Mold Clamping Issues
Improper mold clamping forces can cause incomplete parts or excessive flash.
Prevention: Ensure that the mold clamping system is operating properly to avoid insufficient or uneven clamping forces.
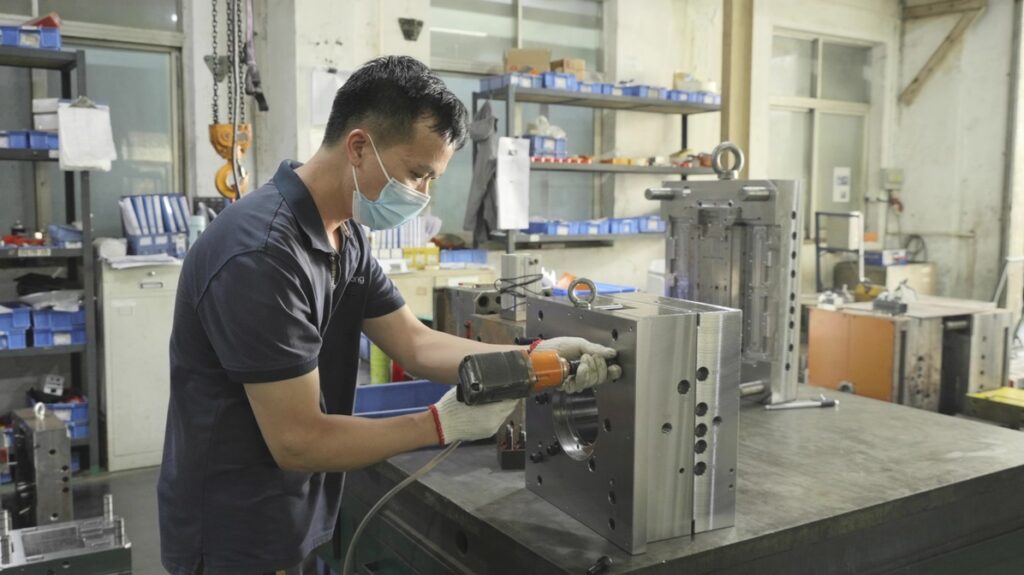
11. Ejection Problems
If the mold’s ejection system is poorly designed or damaged, the parts may become stuck in the mold, making ejection difficult.
Prevention: Consider ejection angles in mold design, ensuring the ejection system operates smoothly and regularly maintaining it.
12. Corrosion
Molds that are in constant contact with moisture or chemicals can corrode, affecting the mold’s precision and service life.
Prevention: Use corrosion-resistant materials and regularly clean and maintain molds to prevent rust. Store molds in a dry environment.
13. Insufficient Maintenance
If molds are not regularly inspected and maintained, failures are more likely to occur. Without proper care, molds can wear out prematurely, increasing production cycles.
Prevention: Develop and implement a strict mold maintenance plan, regularly inspecting, cleaning, and lubricating the molds.
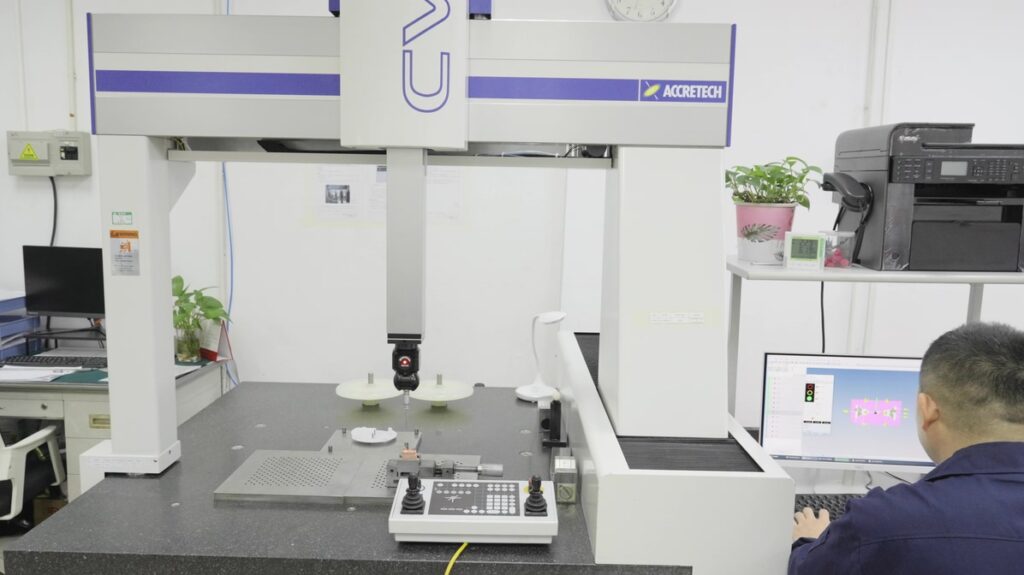
Choose Rilong for Professional Mold Design and High-Quality Assurance
In the plastic injection molding process, the precision and reliability of molds are crucial. By understanding the common causes of mold failures and how to prevent them, businesses can improve production efficiency, reduce costs, and ensure product quality. Rilong Precision Mold Manufacturing has over 30 years of industry experience and is dedicated to providing high-precision, reliable mold design and manufacturing services.
Whether you need precision injection molds, two-color molds, overmolding molds, or custom designs, Rilong can provide you with the most professional solutions. Our mold design team will work closely with you from design to trial, ensuring that every requirement is perfectly met.
立即联系我们 to get professional mold solutions and optimize your production while enhancing your competitiveness!