You’ve probably heard this before: “Moldflow Analysis saves time, cost, and prevents defects.” But how exactly does it work? Let’s break it down.
🧠 You’re the Customer, and You’re Curious…
“Every supplier tells me moldflow is important. They say it saves cost, shortens development time, avoids mold damage.
But I still wonder — how does this actually happen? Is this just technical talk to impress me? Or does it really make a difference?”
Let’s walk you through the real logic, real benefits, and real impact of moldflow analysis — in a way that makes sense whether you’re an engineer or a sourcing manager.
📌 What Is Moldflow Analysis, in Simple Terms?
Moldflow analysis is a simulation of how molten plastic flows inside a mold cavity during injection molding.
Think of it as a virtual test shot — but done before we cut steel or make any real mold.
With this simulation, we can:
- Optimize the gate location and flow path
- Predict how the plastic fills the cavity
- Find where air traps, weld lines, or short shots may occur
- Evaluate pressure, temperature, and cooling behavior
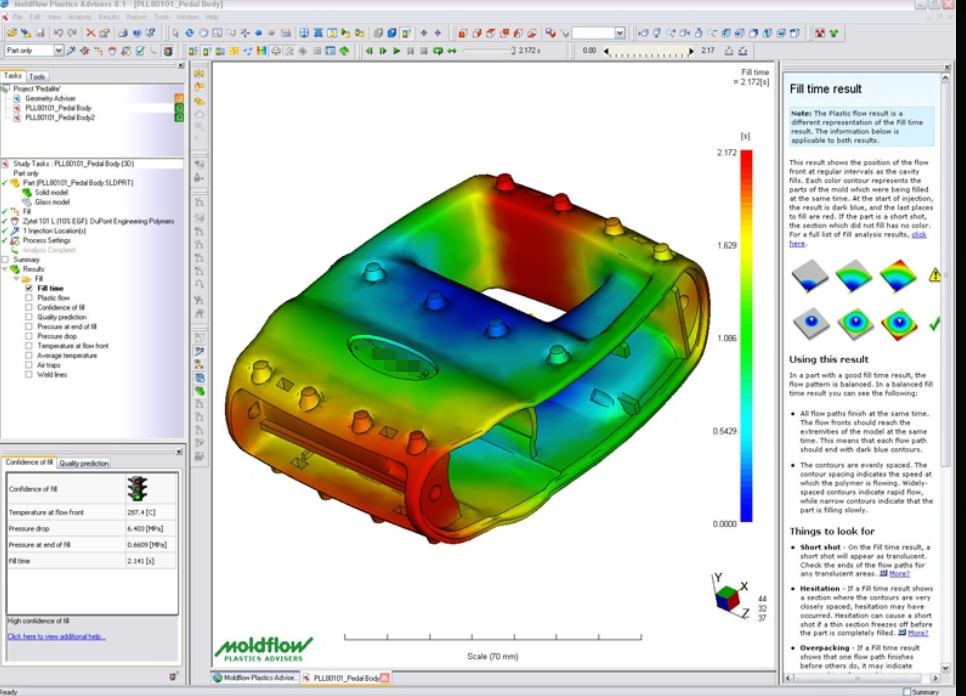
🔍 What Problems Can Moldflow Reveal Before They Happen?
Issue | What It Looks Like | How Moldflow Helps |
---|---|---|
Short Shot | Incomplete filling | Simulates flow to ensure full cavity fill |
Weld Line | Weak joint line | Predicts position to adjust design or gate |
Warpage | Part deformation | Simulates shrinkage and stress |
Air Trap | Burn marks or voids | Predicts trapped air zones for better venting |
Uneven Cooling | Sink marks or distortion | Shows temperature balance, suggests cooling channel changes |
💡 When Do We Run Moldflow?
The best time is before mold fabrication — during the DFM (Design for Manufacturability) review.
It’s even better if we can do it while finalizing your 3D part design, so we can:
- Reduce rework during mold trial
- Recommend wall thickness adjustments
- Optimize parting line or gate positioning
🚀 Real Business Benefits — Not Just Engineering Jargon
✅ Faster Time to Market
Avoid unnecessary rework or mold modification. First trial → Ready to go.
✅ Lower Project Cost
Fewer mold revisions = lower tooling cost = higher ROI.
✅ Higher Quality Parts
Better control over flow, stress, shrinkage = better product consistency.
✅ More Professional Development Process
You gain confidence that we understand your part — from concept to production.
📈 How You Can Use Moldflow to Your Advantage
When your supplier provides a moldflow report, you should expect:
- A clear visual of filling simulation
- Marked areas of risk: weld lines, air traps, sink
- Gate location justification
- Design recommendations, not just charts
This helps you as the customer:
- Trust that your supplier knows what they’re doing
- Make design decisions faster
- Communicate more clearly across your team
🤝 Our Commitment: Moldflow for Every Project
We include moldflow simulation in every tooling project — not just to impress you with tech, but because we know:
Every defect we prevent at the design stage saves weeks and thousands of dollars down the line.
Ready to Build Smarter, Not Just Faster?
Let’s start with a conversation — show Rilong your design, and we’ll show you how to improve it before steel is cut.