In the realm of manufacturing, injection molding stands tall as one of the most versatile and efficient processes for producing plastic parts. From the humble plastic bottle to intricate automotive components, injection molding plays a pivotal role in shaping modern industry. But what exactly is injection molding, and how does it work? Let’s dive into the fundamentals of this fascinating manufacturing technique.
Understanding Injection Molding: At its core, injection molding is a manufacturing process used to produce parts by injecting molten material into a mold cavity. The process typically involves several key steps:
- Mold Design: The first step in injection molding is designing the mold. This involves creating a precise cavity that mirrors the desired shape of the final part. Mold design factors such as part geometry, cooling channels, and material flow are carefully considered to ensure optimal results.
- Material Selection: Once the mold is designed, the next step is selecting the appropriate material for the job. Injection molding materials range from commodity plastics like polyethylene and polypropylene to engineering-grade polymers such as ABS, nylon, and polycarbonate. Material properties such as strength, flexibility, and heat resistance dictate suitability for specific applications.
- Melting and Injection: With the mold and material in place, the injection molding machine heats the selected material to its melting point, forming a viscous liquid. The molten material is then injected into the mold cavity under high pressure, filling the space and taking the shape of the mold.
- Cooling and Solidification: Once the mold cavity is filled, the molten material undergoes a cooling process. Cooling channels within the mold help dissipate heat, allowing the material to solidify and take on the desired shape. Proper cooling is crucial for achieving dimensional accuracy and preventing defects.
- Ejection: After the material has cooled and solidified, the mold opens, and the newly formed part is ejected from the cavity. Ejection mechanisms such as pins, ejector plates, or air blasts help release the part from the mold without damaging its delicate features.
Applications of Injection Molding: Injection molding finds widespread use across various industries due to its versatility and efficiency. Common applications include:
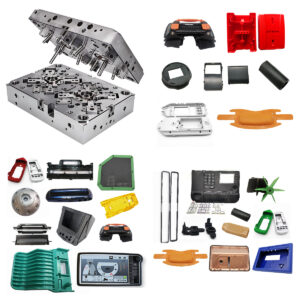
- Consumer Products: From household items like utensils and containers to electronic devices and toys, injection molding enables the mass production of consumer goods with consistent quality and precision.
- Automotive Components: Injection-molded parts play a vital role in automotive manufacturing, from interior trim pieces to under-the-hood components. The process offers cost-effective solutions for producing complex geometries and lightweight parts.
- Medical Devices: The medical industry relies on injection molding for manufacturing disposable syringes, surgical instruments, and device housings. The ability to produce sterile, high-precision parts makes injection molding indispensable in medical device manufacturing.
- Aerospace and Defense: In aerospace and defense applications, injection molding is used to produce lightweight, high-strength components such as interior panels, housings, and structural parts.
Advantages of Injection Molding: Injection molding offers several key advantages over alternative manufacturing processes:
- High Efficiency: Injection molding allows for high-volume production with minimal waste, making it a cost-effective solution for mass manufacturing.
- Design Flexibility: The versatility of injection molding enables the production of intricate part geometries with tight tolerances, opening up new possibilities for product design.
- Material Variety: With a wide range of thermoplastic and thermoset materials available, injection molding offers flexibility in material selection to meet specific performance requirements.
- Consistent Quality: Injection molding ensures uniformity and repeatability in part production, resulting in consistent quality across large production runs.
Conclusion: As a cornerstone of modern manufacturing, injection molding continues to revolutionize the way we design and produce plastic parts. By mastering the fundamentals of injection molding, manufacturers can unlock a world of possibilities for creating innovative products with speed, precision, and efficiency. Whether it’s producing everyday consumer goods or critical components for high-tech industries, injection molding remains at the forefront of manufacturing excellence.