Injection molding is a widely used manufacturing process for producing high-quality plastic parts. A critical part of ensuring the success of this process is polishing. Polishing impacts the final appearance, durability, and functionality of the molded parts, making it an essential step in mold preparation.
Types of Polishing in Injection Molding
There are two primary methods for polishing molds used in injection molding: manual polishing and machine polishing. Each method offers distinct benefits and is used based on the complexity and quality requirements of the project.
Manual Polishing
Manual polishing involves skilled technicians using specialized tools to polish the mold surfaces by hand. This method allows for precise control and is ideal for intricate mold designs or areas that are difficult for machines to reach.
- Benefits:
- High precision for complex geometries
- Better results in corners, edges, and small features
- High polishing standards (e.g., mirror-like finishes for high-end products)
Manual polishing is often used for molds that require high polishing for products with cosmetic or aesthetic requirements, such as medical devices, optical parts, and consumer goods.
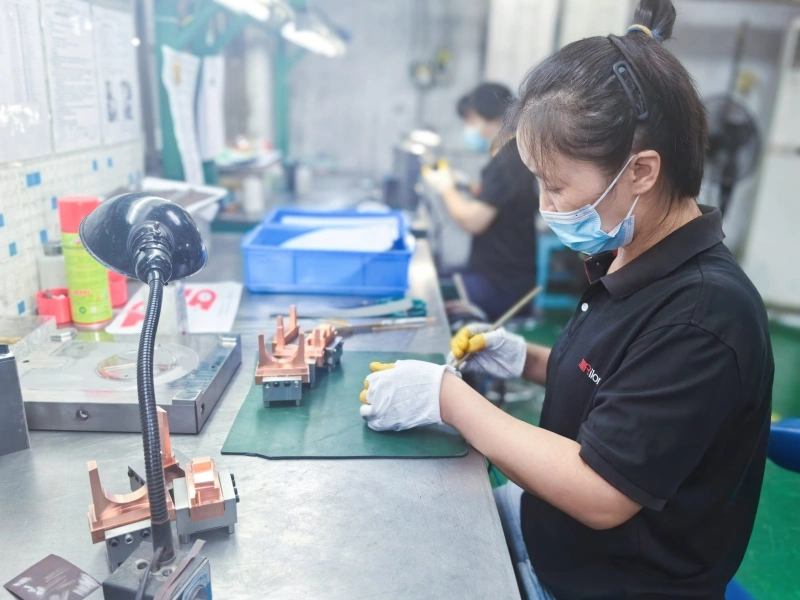
Machine Polishing
Machine polishing uses automated tools to polish large, flat, or simple surfaces. This process is faster and more efficient than manual polishing and is ideal for large production runs where speed and consistency are prioritized.
- Benefits:
- Increased efficiency and lower costs for large volumes
- Consistent results on simple or less intricate mold designs
- Suitable for standard finish requirements
Manual Polishing vs. Machine Polishing
While machine polishing is excellent for high-volume production, it may not achieve the same level of detail or finish quality as manual polishing. In contrast, manual polishing ensures that molds with complex shapes or tight tolerances are polished to perfection, especially when high polishing standards are required.
The choice between manual and machine polishing in injection molding largely depends on the specific part requirements, production scale, and surface quality expectations.
Why Polishing is Critical in Injection Molding
Polishing not only improves the appearance of plastic parts but also enhances the mold’s performance and longevity. A well-polished mold reduces wear and tear, helps in releasing parts from the mold smoothly, and prevents defects such as flow lines or blemishes.
Conclusion
Whether it’s manual or machine polishing, the goal is to create a mold that produces high-quality parts with the desired surface finish. For projects requiring precision, manual polishing remains the best option, while machine polishing is ideal for high-volume production with standard finishes.
At Rilong Precision Mold, we offer comprehensive polishing services as part of our injection molding process, ensuring top-tier quality for every project. Contact us today to learn more about how we can meet your injection molding needs.