With extensive expertise in processing a wide range of common materials, Rilong ensure reliable supply through our dedicated material warehouse, eliminating shortages and guaranteeing seamless production for our customers.
ABS
It’s synthesized from acrylonitrile, butadiene and styrene. Its properties depend mainly on the ratio of the three monomers and the molecular structure in the two phases. This can have great flexibility in product design, and thus produce hundreds of ABS materials of different quality in the market. These different qualities provide different properties such as medium to high impact resistance, low to high finish and high temperature distortion. ABS material has superior workability, appearance characteristics, low creep and excellent dimensional stability as well as high impact strength.
① Application scope:
Automotive parts (instrument panel, wheel cover, etc.), refrigerator, high-strength tools (mixer, food processor, lawn mower, etc.), telephone housing, plastic keyboard, etc
② Injection molding process conditions:
Drying treatment: ABS material has hygroscopicity, which requires drying treatment before processing. It is recommended to dry at 80 to 90℃ for at least 2 hours. The material humidity should be less than 0.1%.
Melting temperature: 210 ~ 280℃; Recommended temperature: 245 ° C
Mold temperature: 25 ~ 70℃. (Mold temperature will affect the finish of plastic parts, low temperature will lead to low finish).
Injection pressure: 500 ~ 1000bar.
Injection speed: medium to high speed.

PA6
The chemical and physical properties of PA6 are similar to that of PA66. However, its melting point is lower and the process temperature range is wide. Its impact resistance and solubility are better than PA66, but its hygroscopicity is also stronger. Because many quality characteristics of plastic parts are affected by hygroscopicity, this should be fully considered when using PA6 to design products. In order to improve the mechanical properties of PA6, various modifiers are often added, and glass fiber is the most common additive. PA6 shrinks between 1 and 1.5 percent. Adding a glass fiber can reduce the shrinkage to 0.3% (but slightly more perpendicular to the process). The shrinkage rate of forming assembly is mainly affected by the crystallinity and hygroscopicity of materials. The actual shrinkage rate is also related to the design of plastic parts, thickness and other process parameters.
① Application scope:
It is widely used in structural components because of its good mechanical strength. Because of its good wear resistance, it is also used in the manufacture of bearings.
② Injection molding process conditions:
Drying treatment: Since PA6 absorbs water easily, special attention should be paid to drying before processing. If the material is supplied in a waterproof package, the container should remain closed. If the humidity is greater than 0.2%, it is recommended to to dry at a temperature above 80℃ for 16 hours. If the material has been exposed to air for more than 8 hours, vacuum drying at 105℃ for more than 8 hours is recommended.
Melting temperature: 230~280℃, 250~280℃ for reinforced varieties.
Mold temperature: 80~90℃.
Injection pressure: generally between 750 and 1250bar (depending on material and product design).
Injection speed: high speed (slightly lower for enhanced materials).
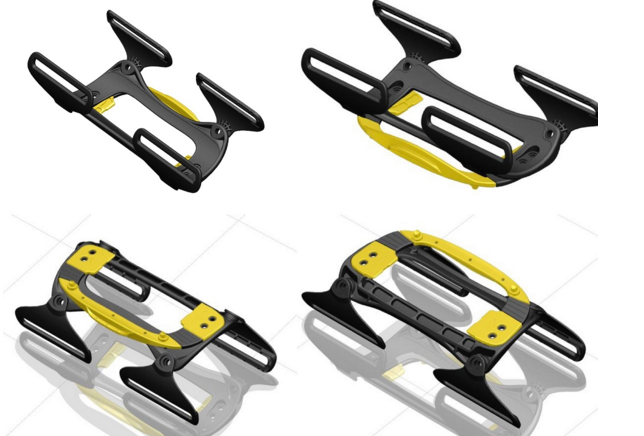
PC
PC is a kind of amorphous material, has a particularly good impact strength, thermal stability, gloss, antibacterial properties, flame retardant properties and pollution resistance. The OTched Izod impact stregth of PC is very high, and the shrinkage rate is very low, generally 0.1%~0.2%. PC has good mechanical properties, but poor flow characteristics, so the injection process of this material is more difficult. In the selection of what quality PC materials, to the final expectations of the product as the benchmark. If plastic parts require high impact resistance, then use low flow rate of PC material; Instead, a PC material with a high flow rate can be used to optimize the injection process.
① Application scope:
Electrical equipment (computer components, connectors, etc.), appliances (food processors, refrigerator components, etc.), transportation industry (Linghting housing, instrument panel, etc)
② Injection molding process conditions:
Drying treatment: PC material has hygroscopicity, drying before processing is very important. The recommended drying condition is 100℃ to 120℃ for 3 to 4 hours. Humidity before processing must be less than 0.02%.
Melting temperature: 260~340℃.
Mold temperature: 70~120℃.
Injection pressure: Use high injection pressure whenever possible.
Injection speed: use low-speed injection for smaller gate types and high-speed injection for other gate types.
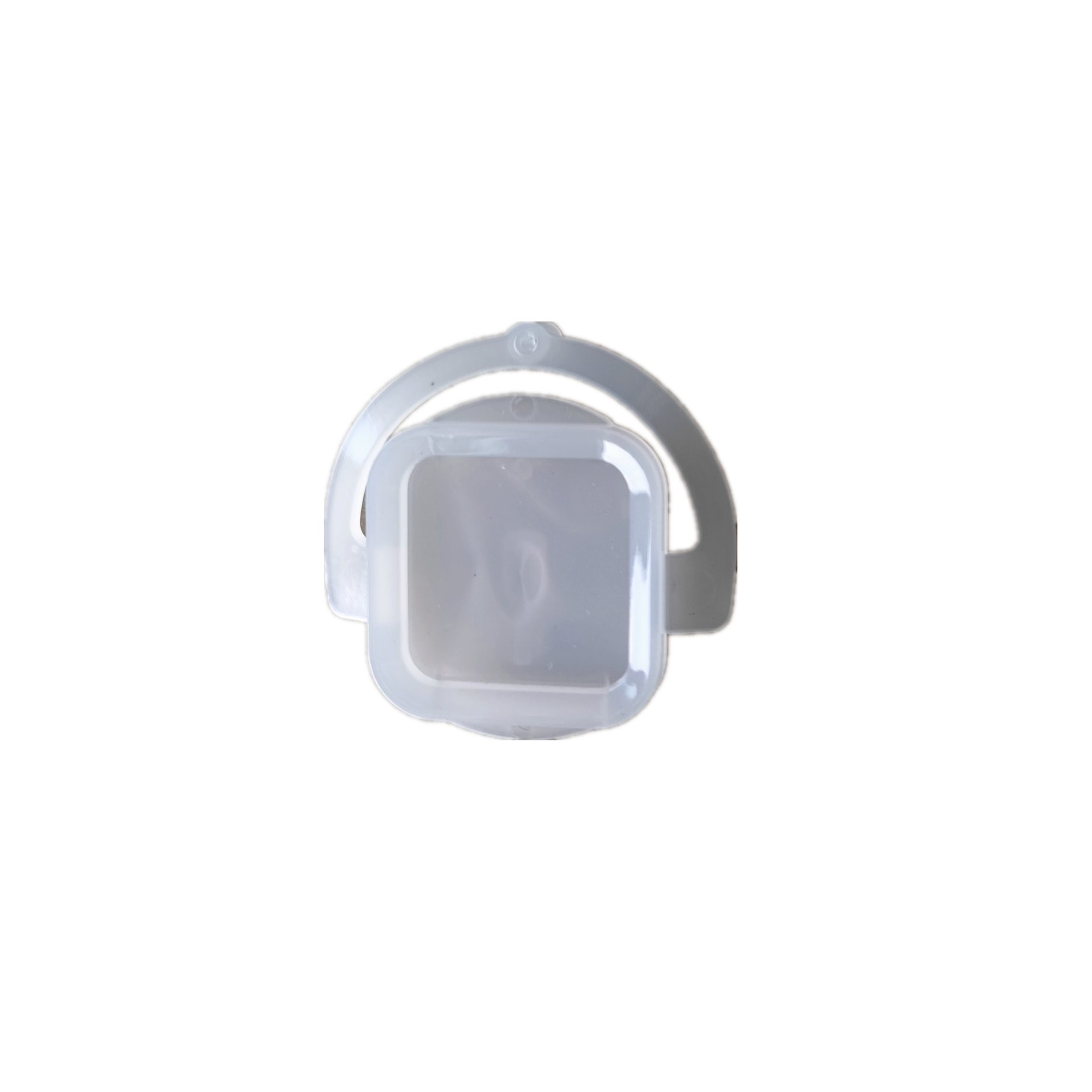
PC/ABS
① Typical application range:
Computer and business machine housings, electrical equipment, auto parts (instrument panels, interior finishes, and wheel covers).
②Injection mold process conditions:
Drying: drying before processing is necessary. The humidity should be less than 0.04%, the recommended drying condition is 90~110℃, 2~4 hours.
Melting temperature: 230~300℃.
Mold temperature: 50~100℃.
Injection pressure: depends on the plastic part.
Injection speed: As high as possible.
③ Chemical and physical properties:
PC/ABS has the comprehensive characteristics of BOTH PC and ABS. For example, ABS has easy machining characteristics and PC has excellent mechanical characteristics and thermal stability. The ratio of the two will affect the thermal stability of PC/ABS materials. The PC/ABS hybrid material also shows excellent flow characteristics.
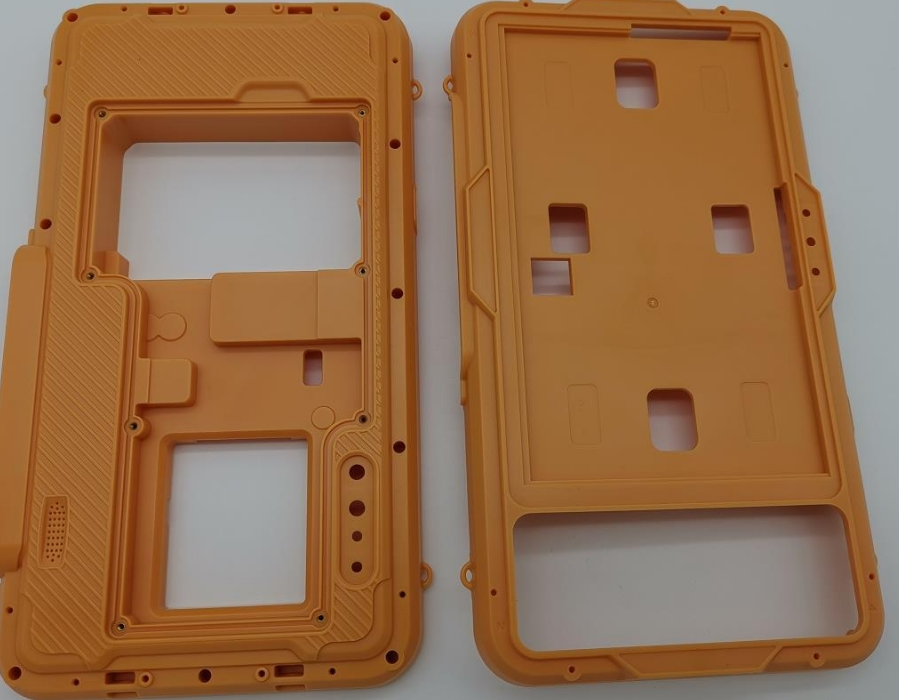
PP
It is a semi-crystalline material. It is harder than PE and has a higher melting point. Since homopolymer PP is very brittle when the temperature is above 0℃, many commercial PP materials are random copolymers with 1~4% ethylene or clamp copolymers with a higher ratio of ethylene content. Copolymer TYPE PP material has a lower thermal distortion temperature (100℃), low transparency, low gloss, low rigidity, but has a stronger impact strength. The strength of PP increases with the increase of ethylene content. The veka softening temperature of PP is 150℃. The material has good surface stiffness and scratch resistance due to its high crystallinity. There is no environmental stress cracking problem in PP. Generally, PP is modified by adding glass fiber, metal additives or thermoplastic rubber. The MFR of PP ranged from 1 to 40. Low MFR PP materials have better impact resistance but lower tensile strength. For the same MFR material, copolymer type strength is higher than homopolymer type. Due to crystallization, shrinkage of PP is quite high, generally 1.8~2.5%. And the directional uniformity of shrinkage rate is much better than PE-HD and other materials. Adding 30% glass additives can reduce shrinkage to 0.7%. Homopolymer and copolymer PP materials have excellent hygroscopicity resistance, acid and alkali corrosion resistance, resistance to dissolution. However, it is not resistant to aromatic hydrocarbon (such as benzene) solvents, chlorinated hydrocarbon (carbon tetrachloride) solvents, etc. PP also unlike PE still has oxidation resistance at high temperature.
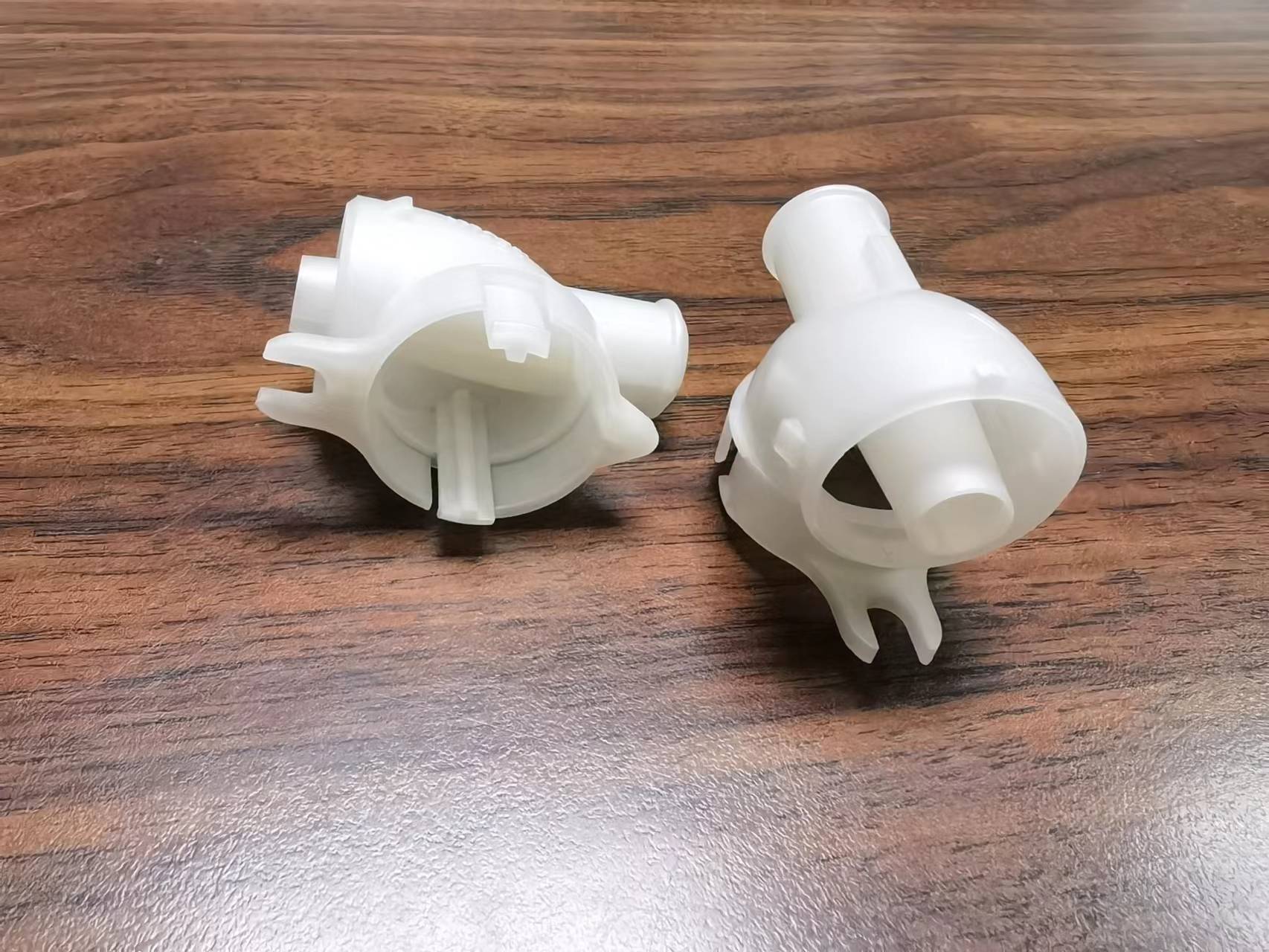
If you’re unsure which plastic material best suits your product, our team is here to help. With years of experience serving diverse industries and working with a wide range of materials, we provide expert material selection and manufacturing recommendations—tailored to your specific needs.